18 Chapter 24: Analyzing the Incident
Chapter Objectives:
- Explain the APIE process in hazardous materials incidents. [5.3.1]
- Define a hazardous materials incident. [4.2.1]
- Recognize ways that hazardous materials harm people. [4.2.1, 5.3.1, 5.5.1]
- Identify states of matter as they relate to hazardous materials. [5.2.1]
- Explain physical properties that aid in identifying potential hazards and predicting behaviour of hazardous materials. [5.2.1]
- Explain chemical properties that aid in identifying potential hazards and predicting behaviour of hazardous materials. [4.2.1, 5.2.1]
- Explain the role of the General Hazardous Materials Behaviour Model in predicting the behaviour of containers. [5.2.1]
- Identify the seven clues to the presence of hazardous materials. [4.2.1]
- Explain how pre-incident plans, occupancy types, and locations may indicate the presence of hazardous materials. [4.2.1]
- Recognize general container types and their associated behaviours and hazards. [4.2.1, 5.2.1]
- Describe ways that transportation placards, labels, and markings indicate the presence and hazards of hazardous materials. [4.2.1]
- Define the hazard classes. [5.2.1]
- Identify other markings and colours that indicate the presence of hazardous materials. [4.2.1]
- Describe ways written resources are used to identify hazardous materials and their hazards. [4.2.1, 5.3.1]
- Skill Sheet 24-1: Analyze a hazardous materials scenario to identify potential hazards. [5.2.1]
- Skill Sheet 24-2: Identify indicators and hazards present at a hazardous materials incident using approved reference sources. [4.2.1]
Chemical substances, materials, and products are stored, manufactured, used, and transported throughout the world every day. While these products have necessary and beneficial uses, many present considerable risks to the public and to the environment if they are uncontrolled or uncontained. Emergency incidents involving these products may differ from other emergencies in significant ways, and first responders must be trained to respond safely and effectively.
Now, what?
Let’s get learning!
Lesson 1
Outcomes:
- Explain the APIE process in hazardous materials incidents.
APIE Response Model
In order to offer guidance to first responders, a simple, 4-step response model can be used in hazardous materials incidents. Known by the acronym, APIE, these steps form a consistent problem-solving process that can be used at any incident, regardless of size or complexity (Figure 24.1).
APIE Response Model
Step 1: Analyze the incident – During this phase of the problem-solving process, personnel and responders attempt to understand the current situation. For example, first responders will attempt to identify the hazmat involved, what kind of containers are present, the number of materials released, the number of exposures, potential hazards, and other relevant information needed to plan a safe and effective response.
Step 2: Plan the initial response – During this phase, responders use the information gathered during the analysis phase to determine what actions need to be taken to mitigate the incident. For example, the Incident Commander (IC) will develop the Incident Action Plan and assign tasks to first responders.
Step 3: Implement the response – During this phase, responders perform the tasks determined in the planning stage. When implementing the response, responders direct actions to mitigate the incident.
Step 4: Evaluate progress – During this phase, which continues throughout the incident until termination, responders monitor progress to see whether the response plan is working. For example, first responders should report if their actions are completed successfully or if they notice changing conditions.
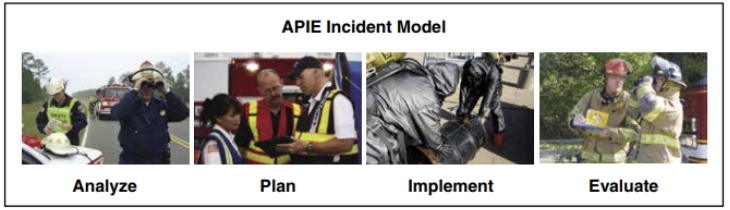
Awareness andOperations level responders generally have responsibilities in the analysis, planning, and implementation phases of a hazardous materials response. This chapter and the chapters that follow describe those responsibilities following the APIE model.
This chapter focuses on analyzing an incident through an understanding of the following:
- Recognizing hazards in hazardous materials incidents
- Understanding hazardous materials’ behaviour
- Identifying container types and the hazards associated with them
- Using written documents and other sources to learn important information about hazardous materials present at a scene.
Lesson 2
Outcomes:
- Define a hazardous materials incident.
What Is a Hazardous Materials Incident?
Substances that possess harmful characteristics are called hazardous materials (or hazmat) in the United States and dangerous goods in Canada and other countries. When particularly dangerous hazardous materials, including chemical, biological, radiological, nuclear, or explosive (CBRNE) materials, are used as weapons, they are sometimes referred to as weapons of mass destruction (WMD) because they have the potential to cause mass casualties and damage.
**NOTE: For simplicity, the term hazmat will be used in this manual in place of hazardous materials/WMD, except when WMDs are addressed directly. **
A hazardous materials incident is an emergency involving a substance that poses an unreasonable risk to people, the environment, and/or property. It may involve a substance (product or chemical) that has been (or could be) released from a container or a substance that is on fire.
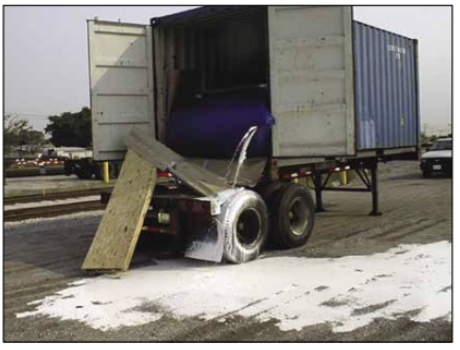
The following are potential causes of hazmat incidents:
- Human error
- Mechanical breakdowns/malfunctions
- Container failures (Figure 24.2)
- Transportation accidents
- Deliberate acts
- Chemical suicides WMD incidents
Hazmat incidents are often more complex than other types of emergency incidents. Often, hazardous materials/WMDs are involved in fires, explosions, and criminal or terrorist activities, complicating the emergency response.
Hazardous materials may:
- Present a variety of dangers, sometimes in small quantities.
- Be extremely difficult to contain and/or control.
- Require specialized equipment, procedures, and personal protective equipment (PPE) to mitigate safely.
- Be difficult to detect, requiring sophisticated monitoring and detection equipment to identify and predict their severity.
Lesson 3
Outcomes:
- Recognize ways that hazardous materials harm people.
- Identify states of matter as they relate to hazardous materials.
How Can Hazmat Hurt You?
Hazardous materials/WMD can hurt you in a variety of ways. They may affect your health if they contact or get into your body, or they may cause harm by their behaviour and/or physical properties if they burn or explode. To safely mitigate hazmat incidents, you must understand the variety of hazardous materials you may encounter, the potential health effects of the materials, and the physical hazards associated with them. Knowing some of these basic concepts will help prevent or reduce injury, loss of life, and environmental/property losses.
The following sections will address:
- Acute and chronic effects
- Routes of entry through which hazardous materials can contact and enter your body
- Specific mechanisms of harm caused by various hazardous materials
Acute vs Chronic
Many hazardous materials have potential health effects. Exposures to hazardous materials may be acute (single exposure or several repeated exposures to a substance within a short time period) or chronic (long-term, reoccur ring). Health effects can also be acute or chronic. Acute health effects are short-term effects that appear within hours or days, such as vomiting or diarrhea. Chronic health effects are long-term effects that may take years to appear, such as cancer.
Some harmful substances do not hurt the body right away. Delayed effects can occur hours or days later. For example, phosgene can cause serious health effects that may not become evident until many hours or days after exposure. In other cases, it may take years before a health issue arises.
In some cases, it may take many years for a chemical, agent, or substance to cause a disease such as cancer. Because of this delay (sometimes called latency period), it can be difficult to establish a direct chain of cause and effect between an exposure to a particular substance and the resulting disease.
Many substances (acetaldehyde, chloroform, progesterone, and polychlorinated biphenyls [PCBs]) are listed by the U.S. Department of Health and Human Services as reasonably anticipated to be carcinogens or suspected carcinogens because the body of evidence concerning their chronic effects is still being gathered and evaluated. In 2000, for example, diesel exhaust particulate was added to the list.
Our understanding of the health effects associated with chemical products and substances is often changing, and new products are continually being developed. First responders should keep in mind that the chronic health effects of substances may not be known for many years, and what is considered safe today, may not be tomorrow.
Routes of Entry
The following are the main routes of entry (aka routes of exposure) through which hazardous materials can enter the body and cause harm (Figure 24.3):
- Inhalation: Breathing hazardous materials in through your nose or mouth.
- Hazardous vapours, smoke, gases, liquid aerosols, fumes, and suspended dusts may be inhaled into your body.
- When a hazardous material presents an inhalation threat, respiratory protection is required.
- Inhalation is the most common exposure route.
- Ingestion: Eating or swallowing hazardous materials through your mouth.
- Deliberate ingestion: Intentionally putting something in your mouth like taking a pill.
- Accidental ingestion:Poor hygiene after handling hazardous material can cause this.
- For example: Chemical residue on your hands can be transferred to your food and then ingested while eating. (Hand washing is important to prevent accidental ingestion of hazardous materials.
- Particles can become trapped in your mucous membranes and ingested after being cleared from your respiratory tract.
- Absorption – Process of taking in materials through your skin or eyes.
- Some materials pass easily through your mucous membranes or areas where your skin is the thinnest, allowing the least resistance to penetration.
- Your eyes, nose, mouth, wrists, neck, ears, hands, groin, and underarms are the most common areas for absorption and many poisons are easily absorbed into your body in this manner.
- Poisons can still enter your body easily if you unknowingly touch a contaminated finger to your eye.
- Injection: Process of taking in materials through a puncture of your skin.
- Protection from injection must be a consideration when dealing with any sort of contaminated (or potentially contaminated) objects easily capable of cutting or puncturing your skin. Such items include:
- Broken glass Nails
- Sharp edges
- Tools like utility knives
- Protection from injection must be a consideration when dealing with any sort of contaminated (or potentially contaminated) objects easily capable of cutting or puncturing your skin. Such items include:
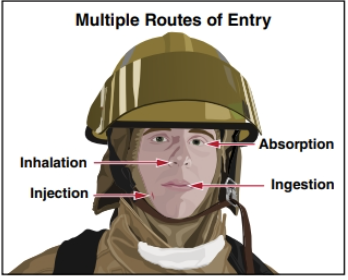
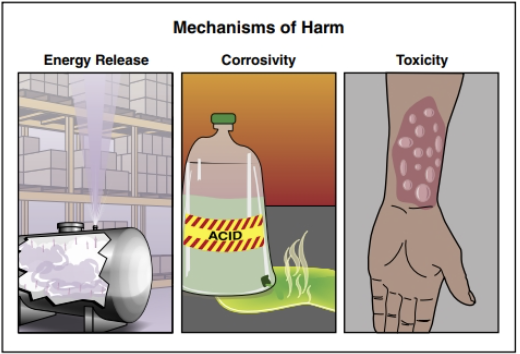
Three Mechanisms of Harm
Thehazardspresentedbyhazardousmaterialsandhazardousmaterialsincidentsmayvaryfromchemicalhazards(such as toxicity)to physical hazards(such as flammability).Some hazards, such as electrical hazards, may be unrelated to the hazmat itself.
Generally speaking, the three mechanisms of harm are (Figure 24.5):
- Corrosivity
- Toxicity
- Energy Release
Corrosives
Corrosives are chemicals that destroy or burn living tissues and have destructive effects by virtue of their corrosivity (ability to cause corrosion, particularly to metals). Corrosive materials can hurt you if they contact your skin or body, and they may also damage tools and equipment. With the exception of liquid and gas fuels, corrosives comprise the largest usage class (by volume) in industry.
Toxicity
Chemicals or biological substances that cause sickness, illness, or injury by doing damage on the molecular scale when in contact with the body are considered toxic. The degree to which a substance causes harm within the body is called its toxicity. A chemical injury at the site of contact (typically the skin and mucous membranes of the eyes, nose, mouth, or respiratory tract) is termed a local toxic effect. Irritant gases such as chlorine and ammonia can, for example, produce a localized toxic effect in the respiratory tract. Toxins can cause damage to organs or other parts of the body. Many toxins have fast-acting, acute toxic effects while others may have chronic effects that are not manifested for many years.
Energy release during hazmat incidents presents the greatest threat. Many hazardous materials will release energy due to their chemical or physical properties, and the way they are shipped and/or stored.
At hazmat incidents, you should always be aware of the following:
Heat: Heat hazards (also called thermal hazards) are common at hazmat incidents. Hazardous materials can cause temperature extremes such as with elevated-temperature materials or exothermic reactions (sudden release of heat energy). Fires and explosions involving flammable liquids and explosive materials can cause burns. Environmental factors such as hot weather can cause heat illnesses. Conversely, a lack of heat can also cause harm. For example, cryogenic liquids and liquefied gases are so cold that if contacted, they can cause damage and injuries. Cold atmospheric temperatures can complicate many hazmat operations, for example, decontamination.
Mechanical Energy: Mechanical energy is possessed by objects due to their position or motion. At hazard-ous materials incidents, emergency responders can be injured by flying or falling objects, such as the failure of a pressurized container, an explosive detonation, a shifting container, or the reactivity of the hazardous material itself. Friction injuries may occur as a result of skin or other portions of the body rubbing against an abrasive surface, such as protective clothing, causing raw skin (abrasions), blisters, and burns.
Pressure: Hazardous materials stored under pressure can release violently if their containers are damaged or mishandled. When released, these materials expand rapidly, spreading whatever chemical hazards they possess quickly over potentially large areas.
Electricity: Electrical hazards and electricity may be present at hazmat incidents in sources, including utilities, energized containers, and electrical equipment, such as portable generators and power tools.
Chemical: When hazardous materials undergo chemical reactions, they release chemical energy. For example, some materials react violently when exposed to water. However, not all chemical reactions result in flames or explosions. Some may release heat, some may use heat, and some may create new hazardous materials with hazards differing from the original materials.
Radiation: Radiation is energy that is emitted as particles or waves. The potential for radiation exposure exists at incidents at medical centres, certain industrial operations, nuclear power plants, and research facilities. There is also the potential for exposure during terrorist attacks.
States of Matter: Hazardous Materials
An uncontrolled hazmat release from a container can create many problems. The material’s physical and chemical properties affect how it behaves, determine the harm it can cause, and influence the effect it may have on all its contacts, including people, other living organisms, other chemicals, and the environment. A material’s physical and chemical properties also influence how a container will behave if it is damaged or ruptured.
First responders need to know how to collect hazard and response data that provide information about the substance’s physical and chemical properties. The proper resources can greatly assist the responder in determining the present hazards, estimating the potential harm, and predicting how the incident may progress.
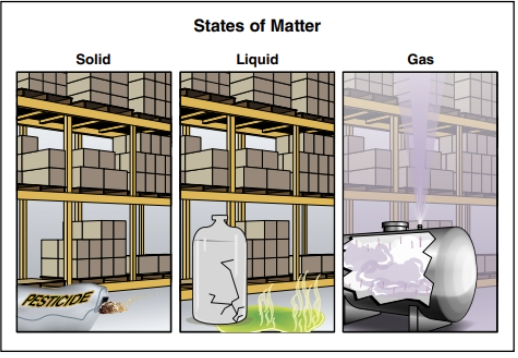
Matter is found in three states (Figure 24.6):
- Gas
- Liquid
- Solid
At a hazmat incident, try to identify the material’s physical state as early as possible, because gaseous, liquid, and solid hazardous materials behave differently. This behaviour influences the material’s potential hazards. Once you understand how matter behaves in each state, you can better predict where the hazardous material is going, what exposures it may affect, and what those effects may be (Figure 24.7). The material’s state of matter will indicate how mobile that material may become and can help determine if there will be far-reaching hazardous properties.
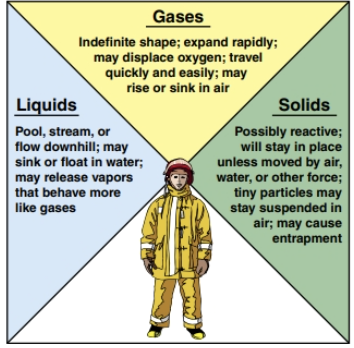
Awareness of hazardous material mobility helps rescuers determine control zones and evacuation distances. The Emergency Response Guidebook (ERG) establishes separate initial isolation distances based solely on the involved product’s state of matter:
- Solids – 75 feet (25m)
- Liquids – 240 feet (50m)
- Gases – 330 feet (l00m)
In general, solids are the least mobile and gases have the greatest mobility. Liquids may be mobile depending on the properties of the substance. A substance’s state may change if the temperature changes. A solid may change to a liquid if the temperature increases. You should consider the temperature’s effect on a substance if the incident is located outside because air temperature and weather factors can strongly influence a substance’s state of matter and subsequently its behaviour (Figure 24.8).
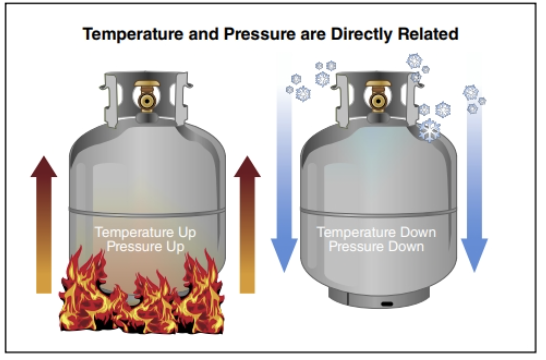
Gaseous Hazmat
Incidents involving gases are potentially the most dangerous for emergency responders. Many hazmat-related injuries are due to the inhalation of vapours or gases.
Gaseous materials could have many variables and hazards, such as:
- May have an odour (such as chlorine)
- May be colourless, odourless, and/or tasteless (such as car-bon monoxide)
- May be separately, or any combination of: toxic (such as phosgene), corrosive (such as ammonia), or flammable (such as methane, natural gas)
- May have high pressure in excess of 15,000 psi (103 000 kPa) (such as liquid helium)
- May be extremely cold upon release and/or may have a large expansion ratio if liquefied
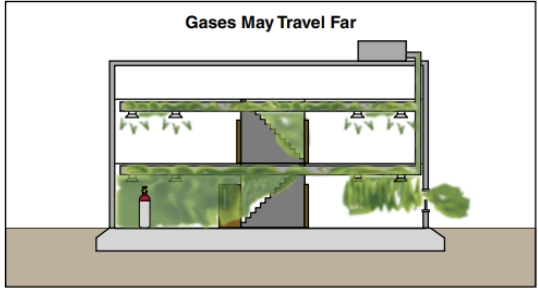
Gases have an undefined shape and volume and keep expanding if uncontained. As a result, it is difficult to detect where they are, where they are not, and where they may be go ing (Figure 24.9). A gas leak in a building has many potential directions to spread. Depending on ventilation and other factors, the gas may spread:
- Throughout the building
- To other buildings
- Through access shafts
- Into the soil
- Into the street, where it will drift wherever the wind may take it
- Gases are difficult (if not impossible) to contain for mitigation purposes. Compressed gases and liquefied gases expand rapidly when released, potentially threatening large areas (Figure 24.10). If a gas is invisible and/or has little or no odour, it may be impossible to detect without specialized detection equipment, such as a combustible gas detector or another instrument (Figure 24.11).
**NOTE:Research has shown that 1- and 2-ton quantities of chlorine and anhydrous ammonia released in an open area may initially spread in a 360° radius before being dispersed downwind. **
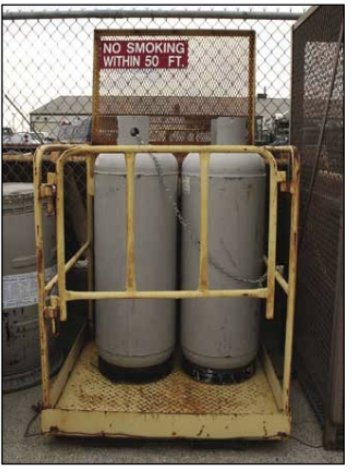
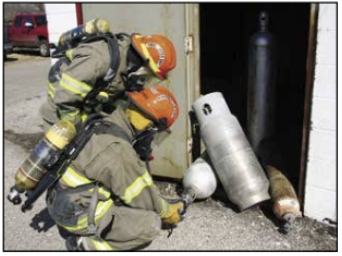
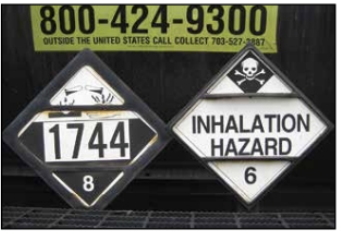
Materials kept under pressures and/or temperatures higher or lower than ambient conditions may change state upon release. The ratio that a gas will expand (expansion ratio) from its liquid state is a significant factor in mitigating a hazmat incident involving materials under specific conditions (especially cryogenic liquids and liquefied gases).
If a hazardous material is a gas, it will be present in the air and present a breathing/inhalation hazard. Some gases may also present a contact hazard (Figure 24.12). In general, if an incident involves a gas, it has the potential to be much harder to mitigate and affect larger areas than incidents involving other states of matter. Incidents involving gas require complex and difficult actions to protect responders and the public.
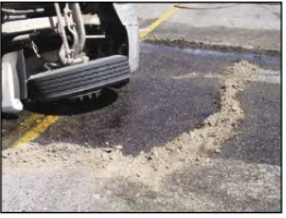
Liquid Hazmat
Liquids are usually visible, even if their vapours are not, so it may be easier to detect their presence and determine the hazard area (Figure 24.13). Liquids typically do not travel as far as gases unless they spill into a path or channel, such as a storm drain, stream, river, or other waterway, that transports liquids quickly and efficiently (Figure 24.14). Responders may be able to predict the paths that spilled liquids will most likely follow.
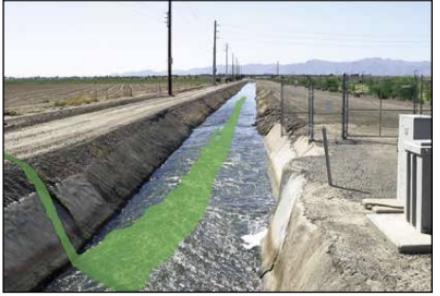
Liquids will flow or pool according to surface contours and topography, permitting opportunities for containment or confinement. Liquids present a splash or contact hazard (Figure 24.15). Liquids may pose unique challenges to responders because they may take on the additional characteristics of a gas by emitting vapours (Figure 24.16). The conversion of liquid to vapour increases both the hazardous material’s mobility and the challenges responders face when dealing with the material.
Vapours from liquids may travel much like gases, although typically not as far from their source, and they may be much more difficult to detect than the liquid itself.
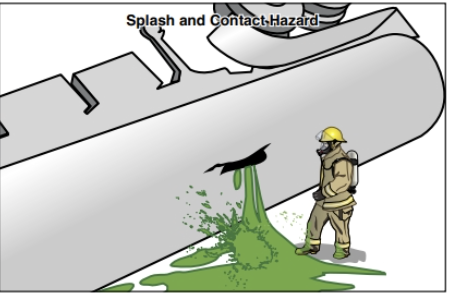
Be cautious and alert to vapours from liquids as they may be:
- Contact hazards
- Inhalation hazards
- Flammable
- Corrosive
- Toxic

Solid Hazmat
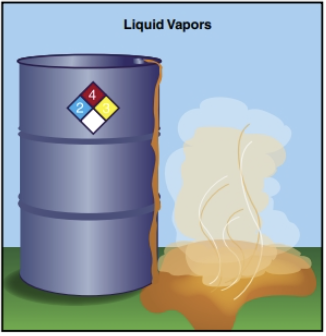
Solids are the least mobile of the three states of matter. They typically will remain in place unless acted upon by exterior forces, such as wind, water, and gravity (Figure 24.17). The particle size of solids, such as dusts, fumes, or powders, may influence their behaviour. Larger particles will probably settle out of the air fairly quickly. Smaller particles may remain suspended longer and travel further than larger particles. Micron is the unit of measure typically used to express particle size.
Solids may have the following dangerous properties:
- Inhalation or contact hazards
- Small, combustible particles that, if ignited, may explode
- Entrapment hazard in the form of loose solids confined to large containers (Figure 24.18)
- Flammable, reactive, radioactive, corrosive, toxic

You can usually detect a solid visually, unless it has microscopic particles. This visibility makes detecting the presence of solids easier than detecting gases or vapours from liquids. Solids such as dry ice, elemental iodine and naphthalene may sublimate/sublime (transition directly from a solid to a gas). Sublimating materials present the same hazards and concerns as liquids that emit vapours. With some exceptions, incidents involving solid materials are confined to limited areas, with less likelihood of undetected travel. Solid incidents may require less complicated mitigation and protective actions than gas and liquid incidents. This response depends on the chemical and physical properties of the material involved.
Lesson 4
Outcomes:
- Explain physical properties that aid in identifying potential hazards and predicting behaviour of hazardous materials.
Physical Properties
Physical properties are the characteristics of a material that do not involve the chemistry or chemical nature of the material. Physical properties describe how a material behaves in relation to physical influences, such as temperature and pressure, or how a material behaves when mixed with, or compared to, another material.
Materials can be characterized by the following physical properties:
- Vapour pressure
- Boiling point
- Solubility/miscibility
- Specific gravity
- Melting point/freezing point/sublimation
- Vapour density
- Persistence
- Appearance and odour
Vapour Pressure
Vapour pressure is the pressure exerted by a saturated vapour above its own liquid in a closed container. More simply, it is the pressure produced or exerted by the vapours released by a liquid. Vapour pressure can be viewed as the measure of the tendency of a substance to evaporate.

Vapour pressures reported in reference materials may use any of the following units:
- Pounds per square inch (psi)
- Kilopascals (kPa)
- Bars
- Millimeters of mercury (mmHg) (used in older-style mate-rial safety data sheets [MSDS])
- Atmospheres (atm)
- Hectopascals (hPa) (used on new GHS safety data sheets [SDS])
Be aware of the following facts regarding vapour pressure:
- Materials with a vapour pressure over 760 mmHg will be gases under normal conditions.
- The higher the temperature of a substance, the higher its vapour pressure will be (Figure 24.19).
- The vapour pressure of a material at 100°F (38°C) will always be higher than the vapour pressure of the same material at 68°F (20°C).
- Higher temperatures provide more energy to a liquid, which allows more liquid to escape into a gaseous form. The gas rises above the liquid and exerts a downward pressure.
- Atmospheric pressure is the baseline measurement for pressure.
- The lower the boiling point (the temperature at which a liquid turns to a gas) of a material, the higher its vapour pressure will be. If a material has a low boiling point, it requires less heat to change from liquid into a gas.
**NOTE: Water requires a lot of heat to boil (212°F [100°C]), but some substances boil at room temperature (68°F [20°C]). **
Boiling Point
Boiling point is the temperature at which a liquid changes to a gas at a given pressure. Boiling point is usually expressed in degrees Fahrenheit (Celsius) at sea level air pressure (Figure 24.20). For mixtures, the initial boiling point or boiling-point range may be given. Flammable materials with low boiling points generally present special fire hazards.

A boiling liquid expanding vapour explosion (BLEVE) (also called violent rupture) can occur when a liquid within a container is heated, causing the material inside to boil or vaporize (such as in the case of a liquefied petroleum gas tank exposed to a fire). If the resulting increase in internal vapour pressure exceeds the vessel’s ability to relieve (or retain) the excess pressure, the container can fail catastrophically. As the vapour is released, it expands rapidly and ignites, sending flames and pieces of tank flying. BLEVEs most commonly occur when flames contact a tank shell above the liquid level or when insufficient water is applied to keep a tank shell cool.
Melting Point/Freezing Point/Sublimation
Melting point is the temperature at which a solid substance changes to a liquid state at normal atmospheric pressure. An ice cube melts at just above 32°F (0°C) — its melting point. Freezing point is the temperature at which a liquid becomes a solid at normal atmospheric pressure. Water freezes at 32°F (0°C) — its freezing point. Some substances will actually sublimate or change directly from a solid into a gas without going into a liquid state in between (Figure 24.21). Dry ice (solid-state carbon dioxide) and mothballs sublimate rather than melt.
Temperatures change throughout the day due to weather patterns and exposure to the sun. A material that begins the day as a solid may change to a liquid if heated sufficiently. Since materials are typically easier to control as a solid than a liquid, this may affect mitigation strategies.

Vapour Density
Vapour density is the weight of a given volume of pure vapour or gas compared to the weight of an equal volume of dry air at the same temperature and pressure. A vapour density less than one indicates a vapour lighter than air; while a vapour density greater than one indicates a vapour heavier than air. Lighter than air gases and vapours will rise, while heavier than air gases and vapours will sink (Figure 24.22). Examples of materials with a vapour density less than one include helium, neon, acetylene, and hydrogen. Gases with a vapour density less than one will rise quickly and spread to a wide geographical area. Most gases have a vapour density greater than one; they will sink in relation to ambient air and will displace oxygen at low elevations. Heavier vapours and gases are likely to concentrate in low places along or under floors; in sumps, sewers, and manholes; and in trenches and ditches where they may create fire or health hazards (Figure 24.23).
Examples of common materials with a vapour density greater than one include:
- Propane
- Butane
- Hydrogen sulfide
- Ethane
- Chlorine
- Sulfur dioxide
Vapour density varies with the temperature of the vapour or gas. Hot vapours will rise, but unless totally dispersed, they will sink once they have cooled. Cold vapours are dense and will stay low but will rise when they warm. Personnel cannot precisely predict the spread of vapours from the vapour density because topography, weather conditions, and the vapour mixture with air affect vapours. However, knowing the vapour density gives a general idea of what to expect from a specific gas or vapour.
**NOTE:All vapours and gases will mix with air, but the lighter materials (unless confined) tend to rise and dissipate.**

Solubility/Miscibility
Solubility in water expresses the percentage of a material (by weight) that will dissolve in water at ambient temperature. A substance’s solubility affects whether it mixes in water. Solubility information can be useful in determining spill cleanup methods and extinguishing agents. When a non-water-soluble liquid such as a hydrocarbon (gasoline, diesel fuel, pentane) combines with water, the two liquids remain separate (Figure 24.24). When a water-soluble liquid such as a polar solvent (alcohol, methanol, methyl ethyl ketone [MEK]) combines with water, the two liquids mix.
**NOTE: Emergency responders may find that some materials, such as hydrocarbons (gasoline, oil), will initially float, bu
t will sink over time. Degradation, chemical reactions, exposure, and time will all affect materials and change their characteristics. **

Water solubility is also an important contributor for symptom development. Irritant agents that are water soluble usually cause early upper respiratory tract irritation, resulting in coughing and throat irritation. Partially water-soluble chemicals will penetrate into the lower respiratory system and cause delayed (12 to 24 hours) symptoms that include breathing difficulties, pulmonary edema, and coughing up blood.
Miscibility describes the ability of two or more gases or liquids to mix with or to dissolve into each other. Two liquids or gases are miscible if they mix or dissolve into each other in any proportion. Typically, two materials that do not readily dissolve into each other are considered immiscible. For example, water and fuel oil are immiscible. Immiscible materials can create a hazard because oil (which weighs less than water) will float on top of water and could ignite and burn.
Specific Gravity
Specific gravity is the ratio of the density (mass per volume) of a material to the density of a standard material, usually an equal volume of water, at standard conditions of pressure and temperature. If a volume of a material weighs 8 pounds (3.6 kg), and an equal volume of water weighs 10 pounds (4.5 kg), the material is said to have a specific gravity of 0.8. Materials with specific gravities less than one will float in (or on) water. Materials with specific gravities greater

than one will sink in water. Most Flammable Liquids Float on Water Solubility plays an important role in specific gravity. Highly soluble materials will mix or dissolve more completely in water (distributing themselves more evenly throughout), rather than sinking or floating (without dissolving) according to their specific gravities. Most (but not all) flammable liquids have specific gravities less than one and will float on water (Figure 24.25). An important consideration for fire-suppression activities is that flammable liquids will float on water.

Persistence and Viscosity
The persistence of a chemical is its ability to remain in the environment. Chemicals
that remain in the environment for a long time are more persistent than chemicals that quickly dissipate or break down (Figure 24.26). Persistent nerve agents will remain effective at their point of dispersion (release) for a much longer time than non-persistent nerve agents.

Viscosity is the measure of the thickness or flowability of a liquid at a given temperature (Figure 24.27). Numerical values sometimes describe viscosity, with higher numbers indicating higher viscosity. Viscosity deter-mines the ease with which a product will flow; it is greatly affected by temperature. Usually, the hotter a liquid, the thinner or more fluid it becomes. Likewise, the cooler a liquid, the thicker or less fluid it becomes. Liquids with high viscosities, such as heavy oils, have to be heated to increasetheir fluidity. Viscous materials tend to be more persistent and may have a lower vapour pressure. Examples of materials with differences in viscosity are acetone, water, oil, and honey. First responders use viscous materials to reference the way the viscosity of these materials will affect decontamination or collection.
Appearance and Odour
A safety data sheet (SDS) typically contains a description of the material’s appearance (such as physical state or color) and odor. Referring to the SDS could allow first responders to quickly gain important information about the state of matter and potential behaviour of the substance or material.

Appearance may help you detect a substance/material. You should evaluate a change in appearance, which may indicate a change in the behaviour of the substance or material. For many industrial products, the colour listed on the SDS may represent an “average,” and the product shipped may vary significantly in colour and still be the same product. In other instances, a significant difference in colour may also show contamination or high levels of impurities that may have their own hazards.
Responders detecting a chemical via odour could indicate that they are too close. Some chemicals have little or no odour, while others have a strong characteristic odour (Figure 24.28). Some characteristic odours can help identify a material. The smell of natural gas, based on an additive, mercaptan, is similar to that of rotten eggs or sewage. An unexpected odor may be a warning that a substance has escaped from its container
The ability to smell or sense an odour is highly dependent on the individual. Odour threshold is the concentration (in air) at which the “average person” can smell a particular compound. Some people can smell a given compound at an extremely low level. Other people may not be able to smell a particular compound even at very high concentrations in the air. Never use odours to determine safe or unsafe areas; some highly toxic products may cause significant damage at a concentration below the odour threshold. Responders spending too much time exposed to some compounds may become desensitized to the smell of a chemical and may no longer be able to determine its presence.
Lesson 5
Outcomes:
- Explain chemical properties that aid in identifying potential hazards and predicting behaviour of hazardous materials.
Chemical Properties
Chemical properties describe the chemical nature of a material and the behaviours and interactions that occur at a molecular level. Based upon its chemical properties, a hazardous material may present a wide variety of hazards. The hazards may vary from chemical hazards (such as toxicity) to physical hazards (such as flammability). This section describes the variety of hazards that arise from hazardous materials’ chemical properties. This section also includes information on biological hazards. Flammability Most hazardous materials incidents involve flammable materials. Flammable materials can damage life and prop-erty when they ignite, burn, or explode. Use a hazard’s flammability to help determine incident strategies and tactics.
- A flammable hazard depends on properties, including its:
Flash point • Autoignition temperature (sometimes called the autoignition point) - Flammable (explosive or combustible) range

Flash point is the minimum temperature at which a liquid or volatile solid gives off sufficient vapours at its lower explosive limit (LEL) to form an ignitable mixture with air near its surface. At its flash point, a material’s vapours will flash in the presence of an ignition sour
ce but will not continue to burn. Do not confuse flash point with fire point. Fire point is the temperature at which a liquid or volatile substance gives off enough vapours to support continuous burning. A material’s fire point is usually only a few degrees higher than its flash point (Figure 24.29).
Only the vapours burn. The liquid or volatile solid that produces the vapours does not burn. As the liquid’s temperature increases, it emits more vapours. Vapours are emitted below the flash point but not in sufficient quantities to ignite. A substance will not burn if it is not at its flash point temperature. Flammable gases have extremely low flash points so they are flammable all the time.
Autoignition Temperature
The autoignition temperature of a substance is the minimum temperature to which the fuel in air must be heated to initiate self-sustained combustion without initiation from an independent ignition source. This temperature, also known as the ignition temperature, is the point at which a fuel spontaneously ignites. All flammable materials have autoignition temperatures, and these are considerably higher than the flash and fire points. For example, the autoignition temperature of gasoline is about 536°F (280°C), but the flash point of gasoline is -45°F (-43°C). This difference means that at -45°F (-43°C), gasoline will temporarily ignite if a match is waved through its vapours, whereas at 536°F (280°C) it ignites all by itself. The terms autoignition temperature and ignition temperature are often used synonymously; they are always the same temperature. However, the NFPA defines these terms separately.

Flammable, Explosive, or Combustible Range
The flammable, explosive, or combustible range is the percentage of the gas or vapour concentration in air that will burn or explode if ignited. The lower explosive limit (LEL) or lower flammable (explosive) limit (LFL) of a vapour or gas is the lowest concentration (or lowest percentage of the substance in air) that will produce a flash of fire when an ignition source is present. At concentrations lower than the LEL, the mixture is too lean to burn. The upper explosive limit (UEL) or upper flammable limit (UFL) of a vapour or gas is the highest concentration (or highest percentage of the substance in air) that will produce a flash of fire when an ignition source is present. At higher concentrations, the mixture is too rich to burn (Figure 24.30). Within the upper and lower limits, the gas or vapour concentration will burn rapidly if ignited. Atmospheres within the flammable range are particularly dangerous. Table 24.1 provides the flammable ranges for some selected materials (NIOSH, 2016).
Corrosivity
Corrosives are commonly divided into two broad categories: acids and bases (bases are sometimes called alkalis or caustics). However, some corrosives (such as hydrogen peroxide) are neither acids nor bases. The corrosivity of acids and bases is often measured or expressed in terms of pH (Figure 24.31).
Acids and bases have the following characteristics:
- Acid: Any chemical that ionizes (dissociates) to yield hydrogen ions (hydronium) in water.
- Acids have pH values of 0 to 6.9. An acid may cause severe chemical burns to flesh and permanent eye damage.
Figure 24.31 pH measures acidity and alkalinity. - Contact with an acid typically causes immediate pain.
- Hydrochloric acid, nitric acid, and sulfuric acid are examples of common acids.
- Acids have pH values of 0 to 6.9. An acid may cause severe chemical burns to flesh and permanent eye damage.
- Base (alkalis): A water-soluble compound that chemically dissociates in water to form a negatively charged hydroxide ion.
- Bases react with an acid to form a salt by releasing an unshared pair of electrons to the acid or by receiving a proton (hydrogen ion) from the acid.
- Bases have pH values of 7.1 to 14.
- A base breaks down fatty skin tissues and can penetrate deeply into the body.
- Bases tend to adhere to the tissues in the eye, which makes them difficult to remove.
- Bases often cause more eye damage than acids due to the longer duration of exposure.
- Contact with a base does not normally cause immediate pain.
- A common sign of exposure to a base is a greasy or slick feeling of the skin, which is caused by saponification, the breakdown of fatty tissues.
- Examples of bases include caustic soda, potassium hydroxide, and other alkaline materials commonly used in drain cleaners.
Reactivity
The chemical reactivity of a substance de-scribes its relative ability to undergo a chemical reaction with itself or other materials. As a result, Reactivity Triangle pressure buildup, temperature in-crease, and/or formation of noxious, toxic, or corrosive by-products may occur. Reactive materials commonly react vigorously or violently with air, water, heat, light, each other, or other materials.

Many first responders are familiar with the fire tetrahedron or the four elements necessary to produce combustion: oxygen, fuel, heat, and a chemical chain reaction. Fire is just one type of chemical reaction. A reactivity triangle can be used to explain the basic components of many (though not all) chemical reactions: an oxidizing agent (oxygen), a reducing agent (fuel), and an activation energy source (often, but not always, heat) (Figure 24.32).
All reactions require some energy to get them started (Figure 24.33) (commonly referred to as activation energy). How much energy is needed depends on the particular reaction. In some cases, heat from an external source provides the energy-added heat from an external source (such as when starting a fire with a match). In some instances, radio waves, radiation, or another waveform of energy may provide the activation energy to the molecules, such as when food is heated in a microwave oven. In other reactions, the energy could come from a shock or pressure change such as changes that might occur when nitroglycerin is jostled.

Reactions that have low-activation energies need little help to begin reacting. Materials that are generally classified as water-reactive typically react with water easily at room temperature because the ambient temperature is sufficient to start the reaction. First responders may see terms such as light-sensitive, heat-sensitive, or shock-sensitive on SDSs and/or manufacturers’ labels, indicating that those products have an increased susceptibility to those sources of activation energy. See Table 24.2 for a summary of the different ways in which chemicals can be reactive (U.S. EPA “CAMEO”, 2016). This table supplies the definition and chemical examples of nine re-active hazard classes.

The oxidizing agent in the reactivity triangle provides the oxygen necessary for the chemical reaction. Strong oxidizers are materials that encourage a strong reaction (by readily accepting electrons) from reducing agents (fuels). The greater the concentrations of oxygen present in the atmosphere, the hotter, faster, and brighter a fire will burn. The same principle appliesto oxidation reactions — in general, the stronger the oxidizer, the stronger the reaction. Many organic materials ignite spontaneously when they come into contact with a strong oxidizer. An asphalt roadway could explode if liquid oxygen (a cryogenic liquid) spills on it and is ac-companied by sufficient activation energy (from shock or friction such as someone stepping on it) (Figure 24.34). The reducing agent in the fire tetrahedron acts as the fuel source for the reaction. It combines with the oxygen (or losing electrons to the oxidizer) in such a way that energy is being released. Oxidation-reduction (redox) reactions can be extremely violent and dangerous because they release a tremendous amount of energy. Some reducing agents (fuels) are more volatile than others.
** NOTE: Wood is not as prone to undergo rapid oxidation (it will not burn as easily) as a highly flammable liquid such as MEK. **

Polymerization is a chemical reaction in which simple molecules combine to form long chain molecules. Catalysts will increase the rate of polymerization and decrease the activation energy necessary for further polymerization. Examples of catalysts include light, heat, water, acids, or other chemicals. Uncontrolled polymerization often results in a tremendous release of energy. Materials that may undergo violent polymerization if subjected to heat or contamination are designated with a P in the blue and yellow sections of the Emergency Response Guidebook (ERG) (Figure 24.35).
** NOTE: Potential for polymerization may not be included on any type of reference material other than the ERG, and the ERG may not be fully inclusive of all polymerizing materials. The ERG is discussed in great detail in a later section of this chapter. **
Inhibitors are materials that are added to products that easily polymerize in order to control or prevent an undesired reaction. Inhibitors increase the needed activation energy. They may be exhausted over a period of time or when exposed to circumstances or unexpected contamination that causes them to be consumed more rapidly, such as exposure to heat or other reaction triggers. Shipments of polymerizing materials may become unstable if delayed during transport or involved in accidents. For example, time-sensitive inhibitors are added to liquid styrene before it is shipped in order to prevent the styrene from polymerizing during transport (Figure 24.36).

If containers holding the styrene rupture or emergency responders add water, the inhibitor becomes exhausted, and the polymerization reaction begins. The sudden loss of containment due to polymerization is a chemical process that may not require an external heat source. Under emergency conditions, reactive materials can be extremely destructive and dangerous. Keep people and equipment upwind, uphill, and back a safe distance or in protected locations until pertinent facts are established and definite plans can be formulated. With advances in modern technology, more and more reactive and unstable materials are being used for various processes, and you must be prepared to deal with them. Radioactivity In addition to recognizing radioactive material packaging, first responders need to understand basic protection strategies if radioactive materials or radiation are present at an incident. Radiation comes in different forms, some more energetic than others (Figure 24.37). The least energetic form of radiation is non-ionizing radiation such as visible light and radio waves. The most energetic (and hazardous) form of radiation is ionizing radiation.
The following sections will address:
- Types of ionizing radiation
- Radioactive material
- exposure and contamination


Types of Ionizing Radiation Ionizing radiation can be divided into four types: alpha, beta, gamma, and neutron. (Figure 24.38):
- Alpha: Energetic, positively charged alpha particles (helium nuclei) emitted from the nucleus during radio-active decay that rapidly lose energy when passing through matter (Figure 24.39).
Figure 24.39 During radioactive decay, alpha particles are emitted from the nucleus of an atom, forming a new element. - They are commonly emitted in the radioactive decay of some manmade elements and the heaviest radioactive elements such as uranium and radium.
- Alpha particles do not travel far in open air; you may have to get very close to the source for the equipment to detect particles.
- Details:
- Alpha particles lose energy rapidly when travelling through matter and do not penetrate deeply.
- They can cause damage over a short path through human tissue.
- They are usually completely blocked by the outer, dead layer of the human skin, so alpha-emitting radioisotopes are not a hazard outside the body. However, they can be very harmful if the material emitting the alpha particles is ingested or inhaled.
- Alpha particles can be stopped completely by a sheet of paper.
- Beta: Fast-moving, positively charged protons or negatively charged electrons emitted from the atom’s nucleus during radioactive decay. Humans are exposed to beta particles from manufactured and natural sources such as tritium, carbon-14, and strontium-90.
- Details:
- Beta particles penetrate further than alpha particles but cause less damage over equally traveled distances.
- Beta particles are capable of penetrating the skin and causing radiation damage; however, as with alpha emitters, beta emitters are generally more hazardous when inhaled or ingested.
- Beta particles travel appreciable distances in air but can be reduced or stopped by a layer of clothing, a thin sheet of metal, or thick Plexiglass.
- Detection distances for beta particles vary based on the activity of the source.
- Compared to alpha radiation, beta radiation will travel farther.
- Shielding beta emitters with dense metals can result in the release of X-rays (Bremsstrahlung radiation).
- Details:
- Gamma: High-energy photons (weightless packets of energy like visible light and X-rays).
- Gamma rays of-ten accompany the emission of alpha or beta particles from a nucleus.
- They have neither a charge nor a mass but are penetrating.
- One source of gamma radiation in the environment is naturally occurring potassium-40.
- Common industrial gamma emitting sources include cobalt-60, iridium-192, and cesium-137.
- Details:
- Gamma radiation can easily pass completely through the human body or be absorbed by tissue. It constitutes a radiation hazard for the entire body.
- Gamma radiation levels vary depending on the isotope and activity (Figure 24.40).
Figure 24.40 Activity refers to the number of atoms in a radioactive material that will decay and emit radiation in a second. The higher the number, the more radiation that is emitted. - Materials such as concrete, earth, and lead may be useful as a shield against radiation.
- Standard fire fighting protective clothing provides no protection against gamma radiation.
- Neutron: Particles that have a physical mass but have no electrical charge.
- Neutrons are highly penetrating.
- Fission reactions produce neutrons along with gamma radiation.
- Neutron radiation can be measured in the field using specialized equipment.
- Details:
- Soil moisture density gauges, often used at construction sites, are a common source of neutron radiation.
- Neutrons may also be encountered in research laboratories or operating nuclear power plants.
- Shielding from neutron radiation requires materials with high amounts of hydrogen, such as oil, water, and concrete.
X-rays and gamma rays are high energy electromagnetic radiation commonly referred to as photons.The hazards of these types of radiation are directly correlated to their activity. For the purposes of this manual, they are identical and should be treated the same. Machines such as those found in medical facilities and airports are almost exclusively the sole source of terrestrial X-ray radiation. Since machines can only produce X-rays when powered on, the chances of encountering X-rays at a hazardous materials incident are rare.
Radioactive Material Exposure and Contamination
Radioactive materials (RAM) emit ionizing radiation. Incidents involving radioactive materials are uncommon because they are strictly governed in use, packaging, and transportation. However, there is some concern that radioactive materials could be used in a terrorist attack.
Radiation exposure occurs when a person is near a radiation source and is exposed to the energy from that source. Exposure and damage are not necessarily related. A first responder will need to know the types of radiation that will cause damage and what proximity or level of exposure will cause what kinds of harm (Figure 24.41).
A person may receive a dose of radiation based upon the length of exposure, energy, and type of source (alpha, beta, gamma, or neutron). Exposure to radioactive material does not make a person or object radioactive. Damage is often described in terms of dosage, indicating the amount of energy absorbed by matter.
Radioactive contamination occurs when radioactive material is deposited on surfaces, skin, clothing, or any place where it is not desired. Radiation does not spread; radioactive material and contamination spread.
Exposure to radiation alone does not contaminate a person. Contamination only occurs when the radioactive material remains on a person or the person’s clothing after coming into contact with a contaminant. A person can become contaminated externally, internally, or both. Radioactive material can enter the body via one or more routes of entry. An unprotected person contaminated with radioactive material receives radiation exposure until the source of radiation (radioactive material) is removed. Radiation detectors capable of detecting alpha and beta contamination can detect radioactive contamination.
Note the following examples:
- A person is externally contaminated (and receives external exposure) when radioactive material is on the skin or clothing.
- A person is internally contaminated (and receives internal exposure) when radioactive material is breathed, swallowed, or absorbed through wounds.
- The environment is contaminated when radioactive material is spread about or is unconfined.
- Environmental contamination is another potential source of external exposure.
** NOTE: Some contamination, such as alpha contamination, often requires the detector to be almost touching the source. Radiation Health Hazards The effects of ionizing radiation occur at the cellular level. **
Radiation Health Hazards
The effects of ionizing radiation occur at the cellular level. Ionizing radiation can negatively affect the normal operation of the cells that compose human organs.
Radiation may cause damage to any material by ionizing the atoms in that material. When atoms are ionized, the chemical properties of those atoms are altered. This change in chemical properties can result in a change in the chemical behavior of the atoms and/or molecules in the cell. If a person receives a sufficiently high dose of radiation and many cells are damaged, this may cause observable health effects, including genetic mutations and cancer.
The biological effects of ionizing radiation depend on how much and how fast a radiation dose is received. The two categories of radiation doses are acute and chronic.
Acute doses
Exposure to radiation received in a short period of time is an acute dose. Acute exposures are usually associated with large doses. Some acute doses of radiation are permissible and have no long-term health effects. However, high levels of radiation received over a short time can produce serious health effects, including reduced blood count, hair loss, nausea, vomiting, diarrhea, and fatigue. Extremely high levels of acute radiation exposure such as those received by victims of a nuclear bomb can result in death within a few hours, days, or weeks.
Chronic doses
Small amounts of radiation received over a long period of time. The body is better equipped to handle a chronic dose of radiation than an acute radiation dose. After a chronic dose, the body has enough time to replace dead or nonfunctioning cells with healthy ones. Chronic doses do not result in the same detectable health effects seen with acute doses. However, chronic exposure to radiation causes cancer. Examples of chronic radiation doses include the everyday doses received from natural background radiation, and those received by workers in nuclear and medical facilities. First responders at most hazmat incidents are unlikely to encounter exposures that cause any health effects, especially if proper precautions are taken. Even at terrorist incidents, it is unlikely that first responders will encounter dangerous or lethal doses of radiation.

Protection from Radiation
Because radiation is invisible, it may be difficult to determine if it is involved in an incident. Class 7 radioactive materials packages should have the appropriate placard or label in transport (Figure 24.42). If responders note their presence at an incident, they should initiate radiation detection and monitoring. Responders should con-duct radiation monitoring if an incident is a suspected terrorist attack or explosion. While most incidents involving radioactive materials present minimal risks to emergency responders, it is still necessary to take appropriate precautions to prevent unnecessary exposures.
One basic protection strategy uses time, distance, and shielding (Figure 24.43):
- Time: Decrease the amount of time spent in areas where there is radiation.
-
Figure 24.43 For protection, responders should limit the time they are exposed to radiation, increase their distance from the radiation source, and use shielding. At a minimum, the time required includes:
- Entering the zone
- Staying within the zone
- Exiting the zone
-
- Distance: Know your dose rate to know the safe distances from the radioactive material. Increase the distance from a radiation source.Doubling the distance from a point source divides the dose by a factor of four. This calculation is sometimes referred to as the inverse square law. When the radius doubles, the radiation spreads over four times as much area, so the dose is only one-fourth as much (Figure 24.44).This calculation is only a rule of thumb, and the information must be supplemented with information from your meter.
- If sheltered in a contaminated area, keep a distance from exterior walls and roofs.
- Shielding: Create a barrier between responders and the radiation source with a building, earthen mound, or vehicle.
- Buildings, especially those made of brick or concrete, provide considerable shielding from radiation.
- For example, exposure from fallout is reduced by about 50 percent inside a one-story building and by about 90 percent at a level below-ground.
Figure 24.44 Doubling the distance from a radiation source divides the dose by a factor of four.
- For example, exposure from fallout is reduced by about 50 percent inside a one-story building and by about 90 percent at a level below-ground.
- Buildings, especially those made of brick or concrete, provide considerable shielding from radiation.
** NOTE: Using time, distance, and shielding to limit exposure to radiation is sometimes referred to as the ALARA (As Low As Reasonably Achievable) method or principle. **
Toxicity
Toxic materials may be absorbed into the bloodstream and distributed to other parts of the body, producing systemic effects. Many pesticides absorb through the skin, distribute to other sites in the body, and produce adverse effects such as seizures or cardiac and pulmonary problems. Exposure to toxic materials can result not only in the development of a single systemic effect but also in the development of multiple systemic effects or a combination of systemic and local effects. Some of these effects may be delayed in a range anywhere between seconds and decades. Table 24.3 gives types of chemical toxins, their target organs, and chemical examples.
Following exposure to a toxic substance, the likelihood of an adverse health effect occurring and the severity of the effect depend on the following:
- Toxicity of the chemical or biological substance
- Exposure pathway or route
- Nature and extent of the exposure
- Person’s susceptibility to illness or injury, affected by such factors as their age or other health concerns (including chronic diseases)
The following are some specific toxic chemical hazard categories:

Asphyxiants
Asphyxiants prevent access to sufficient volumes of oxygen. They can be divided into two classes; simple and chemical. Simple asphyxiants are gases that displace oxygen. These gases may dilute or dis-place the oxygen concentration below the level required to sustain life. Chemical asphyxiants are materials that prohibit the body’s cells from using oxygen.
Some chemical asphyxiants may be used in terrorist attacks:
- Irritants: Irritants cause temporary, sometimes severe, inflammation to the eyes, skin, or respiratory system (Figure 24.45).
- Irritants often attack the body’s mucous membranes, such as the surfaces of the eyes or the linings of the nose, mouth, throat, and lungs.
-
Figure 24.46 Exposure to some pesticides may cause convulsions. Courtesy of Rich Mahaney. Convulsants: Convulsants cause convulsions (involuntary muscle contractions).
- Convulsants can kill if the victim asphyxiates or succumbs to exhaustion while convulsing.
- Examples of convulsants include strychnine, organophosphates, carbamates, and infrequently used drugs such as picrotoxin (Figure 24.46).
- Carcinogens: Carcinogens are known, or suspected, to cause cancer.
- While exact exposure data is unknown for most carcinogens, exposures to only small amounts of some substances may have long-term consequences.
- Disease and complications can occur as many as 10 to 40 years after exposure.
- Statistics reveal 1 in 3 firefighters will be diagnosed with cancer during their career. Another 45% of firefighters will have cancer diagnosed within seven years of retirement.
- Meta studies in the U.S. and Australia show firefighters have an elevated risk of suffering from leukemia and testicular cancer (114%-202% respectively) to name just two.
- Known or suspected carcinogens include:
- Arsenic
- Asbestos
- Benzene
- Many plastics
- Nickel
- Polyvinyl chloride
- Some chlorinated hydrocarbons
- Some pesticides
- Allergens and sensitizers: Allergens cause allergic reactions in people or animals.
- Sensitizers are chemicals that cause a substantial proportion of exposed people or animals to develop an allergic reaction after one or more exposures to the chemical.
- Some individuals exposed to a material may not be abnormally affected at first but may experience significant and dangerous effects when exposed to the material again.
- Common examples of sensitizers and allergens include latex, bleach, and urushiol (the chemical found in the sap of poison ivy, poison oak, and poison sumac).
While the heat energy from a fire is a danger to anyone directly exposed to it, exposure to toxic smoke can cause both acute and chronic health effects. Smoke is an aerosol comprised of gases, vapour, and solid particulates. Fire gases, such as carbon monoxide, are generally colourless, while vapour and particulates give smoke its varied colours. Most components of smoke are toxic and many are carcinogenic. Almost all present a significant threat to human life.
The materials that compose smoke vary from fuel to fuel. Generally, consider all smoke toxic and carcinogenic. In addition to the gases listed below, fires and smoke may expose responders to a wide range of potentially carcinogenic substances such as asbestos, soot, and creosote.
Three of the more common products of combustion are:
- Carbon monoxide (CO): a chemical asphyxiant that is a byproduct of the incomplete combustion of organic (carbon-containing) materials. This gas is probably the most common product of combustion encountered in structure fires. Exposure to it is frequently identified as the cause of death for civilian fire fatalities and for firefighters who have run out of air in their SCBAs.
- Hydrogen cyanide (HCN): produced in the combustion of materials containing nitrogen, is also commonly encountered in smoke, although at lower concentrations than CO. HCN also acts as a chemical asphyxiant. HCN is a significant byproduct of the combustion of polyurethane foam, which is commonly used in furniture and bedding.
- Carbon dioxide (CO2 ): a product of complete combustion of organic materials. It acts as a simple asphyxiant by displacing oxygen. Carbon dioxide also increases respiratory rate.
** NOTE: For more information on combustion byproducts, review the information in Chapter 4, Fire Dynamics. **
Biological Hazards
Biological (or etiological) hazards are microorganisms, such as viruses or bacteria (or their toxins), that may cause severe, disabling disease or illness. Many of these hazards can be transferred from the blood or other bodily fluids of an infected individual. Additionally, some biological hazards cause illness through their toxicity. Always wear appropriate PPE to prevent potential transmission.

Types of biological hazards include:
- Viruses: Viruses are the simplest types of microorganisms that can only replicate themselves in the living cells of their hosts (Figure 24.47). Viruses do not respond to antibiotics.
- Bacteria: Bacteria are microscopic, single-celled organisms. Bacteria may cause disease in people either by invading the tissues or by producing toxins (poisons).
- Rickettsias: Rickettsias are specialized bacteria that live and multiply in the gastrointestinal tract of arthropod carriers (such as ticks and fleas).
- They are smaller than most bacteria, but larger than viruses. Like bacteria, they are single-celled organisms with their own metabolisms, and they are susceptible to broad-spectrum antibiotics.
- However, like viruses, they only reproduce in living cells. Most rickettsias spread only through the bite of infected arthropods (such as ticks) and not through human contact.
- Two types of rickettsia have been weaponized as bioterrorism agents.
- Biological toxins: Biological toxins are produced by living organisms; however, the biological organism itself is usually not harmful to people (Figure 24.48).

Infectious diseases are caused by the reproduction and spread of microorganisms (pathogens) in the body. They may be contagious. Exposure to biological hazards may occur in biological and medical laboratories, agricultural facilities, or when dealing with people or animals who are carriers of such diseases. Some of these diseases are carried in body fluids and are transmitted by contact with the fluids. For instance, in 2014, health care providers in Dallas, TX, were infected with a naturally occurring strain of Ebola after contact with one patient exposed in the outbreak in Africa.
Examples of diseases associated with biological hazards or threats are:
- Malaria
- Ebola
- Tuberculosis
- Hepatitis B
- Influenza
- Typhoid
- Measles

First responders may also be exposed to biological agents used as weapons in terrorist attacks and criminal activities. These biological attacks could produce death and disease in people, animals, and plants. The 2001 anthrax attacks in the United States were an example of a biological attack. Biological attacks use weaponized forms of disease-causing organisms and/or their toxins.
Examples of potential biological weapons include:
- Smallpox (virus) (Figure 24.49)
- Anthrax (bacteria)
- Botulism (toxin from the bacteria Clostridium botulinum)
Lesson 6
Outcomes:
- Explain the role of the General Hazardous Materials Behaviour Model in predicting the behaviour of containers.
General Hazardous Materials
Behaviour Model An uncontrolled release from a container can expose people, animals, and the environment to many hazards. When first responders collect information about the physical and chemical properties of released hazardous materials, they can:
- Determine the present hazards
- Estimate potential harm
- Predict how the incident may progress
The same material physical and chemical properties that create hazards upon release will influence how a container will behave when damaged or ruptured. First responders need to know how to account for these factors when attempting to understand the problem posed by a hazmat incident.
In order for first responders to protect themselves and others, they must understand how a hazardous mate-rial and its container are likely to behave in any given situation. This behaviour typically follows a general pattern. The General Hazardous Materials Behaviour Model, often referred to as the General Emergency Behaviour Model (GEBMO), describes this general pattern. This model is based on Ludwig Benner Jr.’s definition of hazardous materials as “things that can escape from their containers and hurt or harm the things that they touch.”
The model assumes that hazardous materials incidents have the following common elements:
- Material or materials presenting hazards to people, the environment, or property
- Container or containers that have failed or have the potential to fail
- Exposure or potential exposure to people, the environment, and/or property
Given these three elements (material(s), container, and exposure), a common sequence generally occurs (Figure 24.50):
- Stress: The container undergoes physical, thermal, or other types of damage that reduces its ability to function and leads to breach or failure.
- Breach: The container becomes open to the environment.This opening depends on its construction material, type of stress that it undergoes, and pressure inside the container at the time that it fails. A breach or failure of the container may be partial (as in a puncture) or total (as in disintegration).
- Release: When a container breaches or fails, contents, stored energy, and pieces of the container may be expelled into the environment (release). A release always involves the hazardous material product and may (depending on the product, container, and incident conditions) involve the release of energy and container parts.
- Dispersion/engulf: This occurs as the hazardous material inside the container and any stored energy release and move away from the container. Patterns of dispersion are influenced by chemistry, physics, environmental factors, and the chemical and physical characteristics of the product.
- Exposure/contact: Anything (such as persons, the environment, or property) that is in the area of the release is exposed to the hazardous material.
- Harm: Depending on the container, hazardous material, and energy involved, exposures may result in harm or damage.
Stress

Container stress is caused by thermal energy, chemical energy, and mechanical energy:
- Thermal energy: Excessive heat or cold could cause intolerable expansion, contraction, weakening (loss of temper), or consumption of the container and its parts.
- Thermal stress may increase internal pressure and reduce container shell integrity, resulting in sudden failure. Thermal stress may result from the heating or cooling of the container.
- A container undergoing excessive heat may be:
- Extremely close to flames
- Undergoing the operation of a relief device
- Making noises of expansion or contraction
Figure 24.51 The appearance of frost is an indicator that a container is under thermal stress. Courtesy of Barry Lindley. - Subject to changing environmental conditions (such as increased temperature)
- A container succumbing to cold may exhibit:
- Excessive frosting (Figure24.51)
- Visible cold vapours (white clouds)
- Changes in steel structure (smooth to grainy)
- Pools of cold liquid
- Chemical energy: Uncontrolled reactions/interactions of the container and its contents.
- Chemical reactions/ interactions could result in the following:
- Sudden or long-term deterioration of the container.
- Excess heat and/or pressure, causing deteriorationof the container.
- Corrosive or other incompatible interactions between the hazardous materials and the container material.
Figure 24.52 Chemical reactions may cause a container to bulge, which is a sign of significant stress. Courtesy of Barry Lindley. - Visible corrosion or other degradation of container surfaces, including bulging, cracking, and/or popping noises (Figure 24.52).
- The interior of a container may experience chemical stress with no visible indication from the exterior.
- Chemical reactions/ interactions could result in the following:
- Mechanical energy: Physical application of energy could result in container/attachment damage.
- Mechanical stress may:
- Change the shape of the container (crushing) (Figure 24.53).
- Reduce the thickness of the container surface (abrading or scoring).
- Crack or produce gouges.
- Unfasten (sheer) or disengage valves and piping, or penetrate the container wall
- Common causes of mechanical stress include collision, impact, or internal overpressure.
- Clues of mechanical stress include physical damage, the mechanism of injury (forces placed on the container), or operation of relief devices.
- Mechanical stress may:

According to U.S. Department of Transportation (DOT) records, from 2006-2014, nearly 41 percent of all reported hazmat incidents were attributed to container failure. Responders may encounter one or all three of the stressors at any hazmat incident. For instance, heat (thermal stress) can initiate or speed a chemical reaction while weakening a container and increasing its internal pressure. Similarly, a mechanical blow can initiate a violent chemical reaction in an unstable chemical while simultaneously damaging the container.
When evaluating container stress, consider the following:
- Type of container
- Product in the container
- Type and amount of stress
- Potential duration of the stress
Container stress may involve a single factor or several stressors acting on the container simultaneously. Preventing container failure may require reducing or eliminating the factors placing stress on a container. Those factors may be readily visible, such as a collision or a fire impinging on a container surface, or they may not be directly observable and must be predicted based on conditions or other indirect indicators. If the container has already failed, think about other containers that may be exposed and evaluate the impact of product contact with hazardous materials. The material’s state of matter will affect the stress experienced by containers. For example, containers holding gases are inherently subject to stress. Heating or cooling may increase or reduce this stress. These containers may fail catastrophically and/or BLEVE if they are damaged or subjected to additional stress (such as heat from a fire or even hot daytime temperatures). Liquid containers, especially those holding liquids with high vapour pressures, may also fail when subjected to fires. Liquid containers may also transport materials that polymerize. The stress created by an uncontrolled polymerization (chemical stress) may cause container failure. This failure may be explosive. Most solids containers will be damaged via mechanical stressors rather than the physical properties of the materials contained in them. Exceptions would include reactive materials such as explosives, oxidizers, peroxides, and water reactive materials.
Breach
When a container is stressed beyond its limits of recovery, it opens or breaches and releases its contents. Different container types breach in different ways based on a variety of factors (including internal pressure). The type and extent of breach depends upon the type of container and the stress applied. First responders should try to predict the type of damage that may result from the stress that is being or has been applied. The nature of a breach is a major factor in planning offensive product control operations.

Types of breaches include:
- Disintegration: Occurs in containers that are made of a brittle material (or that have been made more brittle by some form of stress). The container suffers a general loss of integrity. Examples of disintegration include a glass bottle shattering or an exploding grenade (Figure 24.54).
- Runaway cracking: Breaks the container into two or more relatively large pieces (fragmentation) or large tears (Figure 24.55). A crack develops in a container and continues to grow rapidly. Runaway cracking often occurs in closed containers, such as drums, tank cars, or cylinders. Runaway linear cracking is commonly associated with BLEVEs.
Figure 24.55 This container experienced a runaway linear crack. Courtesy of Barry Lindley. - Attachments (closures) open or break: May fail, open, or break off when subjected to stress, leading to a total failure of a container (Figure 24.56). When evaluating an attachment (such as a pressure-relief device, discharge valve, or other related equipment) that failed, first responders should consider the entire system and the effect of failure at a given point.
- Puncture: Occurs when foreign objects penetrate through a container, such as forklifts puncturing drums and couplers puncturing a rail tank car (Figure 24.57).
- Split or tear: Containers may also breach through a split, such as
Figure 24.56 Damage to attachments is a common breach. Courtesy of Barry Lindley. a welded seam on a tank or when a drum fails. Mechanical or thermal stressors may cause splits or tears, such as when a seam on a bag of fertilizer rips (Figure 24.58).

Release
When a container fails, its contents, energy, and the container itself (whole or in pieces) may release. If a cylinder of pressurized, flammable gas suffers an attachment failure at the valve due to mechanical stress, the product releases along with a substantial amount of energy (because of stored pressure), which rapidly accelerates the valve and/or cylinder in the opposite direction from the release. Depending on the situation, this release can occur quickly or over an extended time period.

Generally, large amounts of stored chemical/mechanical energy result in a more rapid release, presenting a greater risk to first responders.
Releases are classified according to how fast they occur:
- Detonation: Instantaneous and explosive release of stored chemical energy of a hazardous material. The duration of a detonation can be measured in hundredths or thousandths of a second. An explosion is an ex-ample of a detonation. This re
lease could result in fragmentation, disintegration, or shattering of the container; extreme overpressure; and considerable heat release.
-
Figure 24.59 Rapid relief occurs when pressurized hazmat is released through properly operating safety devices. Violent rupture: Immediate release of chemical or mechanical energy caused by runaway cracks. Violent ruptures occur within a timeframe of one second or less. These releases result in ballistic behaviour of the container and its contents and/or localized projection of container pieces/parts and hazardous material. A BLEVE is an example of a violent rupture.
- Rapid relief: Fast release of a pressurized hazardous material through properly operating safety devices. This action may occur in a period of several seconds to several minutes. Damaged valves, damaged piping, damaged attachments, or holes in the container can result in rapid relief (Figure 24.59).
- Spill/leak: Slow release of a hazardous material under atmospheric or head pressure through holes, rips, tears, or usual openings/attachments. Spills and leaks can occur in a period lasting from several minutes to several days.
Dispersion and Engulfment
The dispersion of material is sometimes referred to as engulfment (Figure 24.60). Dispersion of the hazardous material, energy, and container components depends on the type of release, which include:
-
Figure 24.60 Engulfment occurs when a product disperses, forming a danger zone. A solid, liquid, or gas/vapour
- Mechanical, thermal, or chemical energy and ionizing radiation
- Product characteristics and environmental conditions (such as weather and terrain)
- Physical/chemical properties
- Prevailing weather conditions
- Local topography
- Duration of the release
- Control efforts of responders
The shape and size of the dispersing hazardous material also depends on how the material emerges from its container — whether as an instantaneous “puff,” a continuous plume, or a sporadic fluctuation. The outline of the dispersing hazardous material, sometimes called its dispersion pattern, can be described in a number of ways.

Common dispersion patterns include:
- Hemispheric: Semicircular or dome-shaped pattern of airborne hazardous material that is still partially in contact with the ground or water. A hemispheric release generally results from a rapid release of energy (such as detonation, deflagration, and violent rupture).
- The following elements are common to hemispheric releases (Figure 24.61):
- Energy: Generally travels outward in all directions from the point of release.
- Dispersion of energy: Affected by terrain and cloud cover. Solid cloud cover can reflect the detonation shock wave, increasing the explosion impact.
- Energy release: May propel the hazardous material and container parts; however, this dispersion may not be hemispherical. Large container parts generally (but not always) travel in line with the long axis of the container.
- The following elements are common to hemispheric releases (Figure 24.61):
- Cloud: Ball-shaped pattern of the airborne hazardous material that collectively rises above the ground or water (Figure 24.62).
Figure 24.62 A cloud is a pattern of an airborne hazardous material where the material has collectively risen above the ground or water. - Gases, vapours, and finely divided solids that release quickly (puff release) can disperse in cloud form under minimal wind conditions.
- Terrain and/or wind effects can transform a cloud into a plume.
- Plume: Irregularly shaped pattern of an airborne hazardous material where wind and/or topography influence the downrange course from the point of release (Figure 24.63).
- Dispersion of a plume (generally composed of gases and vapours)
is affected by vapour density and terrain (particularly if vapour density is greater than 1) as well as wind speed and direction.
- Figure 24.64, provides several general guidelines in regards to plume modelling behaviour in urban environments.
Figure 24.63 A plume is an irregularly shaped pattern of an airborne hazardous material influenced by wind and/or topography in its downrange course. - Other plume dispersion elements include the following:
- Puff release: When all of the material is released at one time, the concentration of gas or vapour in the cloud or plume decreases over time.
- Ongoing release: Concentration increases over time until the leak stops or all of the product releases; then it decreases.
- Dispersion of a plume (generally composed of gases and vapours)
- Cone: Triangular-shaped pattern of a hazardous material with a point
source at the breach and a wide base downrange (Figure 24.65).
- An energy release may be directed (based on the nature of the breach) and may project solid, liquid, or gaseous material in a three-dimensional cone-shaped dispersion.
- Examples of cone-shaped dispersions include container failures in a BLEVE or a pressurized liquid or gas release.
- Stream: Surface-following pattern of liquid hazardous material that is affected by gravity and topographical contours (Figure 24.66). Liquid releases flow downslope whenever there is a gradient away from the point of release.
- Pool: Three-dimensional (including depth), slow-flowing liquid dispersion. Liquids assume the shape of their container and pool in low areas (Figure 24.67).
- As the liquid level rises above the confinement provided by the terrain, the substance flows outward from the point of release. If there is a significant gradient or confinement due to terrain, this flow forms a stream.
- Irregular: Irregular or indiscriminate deposit of a hazardous material,
Figure 24.65 A cone is a triangular-shaped pattern of a hazardous material with a point source at the breach and a wide base. such as that carried by contaminated vehicles or responders (Figure 24.68).
- In the event of a release, facility pre-incident surveys may contain plume dispersion models to help estimate the size of an endangered area.
- Computer software such as CAMEO (Computer-Aided Management of Emergency Operations), ALOHA (Area Locations of Hazardous Atmospheres), and HPAC (Hazard Prediction and Assessment Capability) can also assist in the prediction of plume dispersion patterns.
- First responders may consult the ERG for isolation and evacuation distances.




Exposure/Contact

As a container releases, it risks dispersing its contents and the container itself on different types of exposures: people, the environment, and property. In some cases, you can use the ERG to estimate the size of an endangered area. Some hazardous materials may present a threat to one specific exposure type, such as marine pollutants that threaten fish and other marine plants and animals. Others present a threat to all types. When you evaluate the severity of exposures, consider the hazards present, concentration of the material, and duration of contact. Consider the following exposures in hazard and risk assessment (Figure 24.69):
- People: Includes responders and others in the path of a hazardous material.
- Environment: Includes the air, water, ground, and life forms other than humans. The potential effect on the environment varies with the location in which the product is released, as well as its characteristics.
- Property: Includes things threatened directly by the hazardous material or the energy liberated at the time of release. Contacts (impingements) are associated with the following general timeframes:
- Immediate: Milliseconds, seconds (deflagration, explosion, or detonation)
- Short-term: Minutes, hours (gas or vapour cloud)
- Medium-term: Days, weeks, months (lingering pesticide)
- Long-term: Years, generations (permanent radioactive source)
Harm
Harm is defined as injury or damage caused by exposure to a hazardous material. The three mechanisms of harm in a hazardous materials incident were explained earlier:
- Energy release (thermal, mechanical, chemical, pressure, electrical, radiological)
- Corrosivity
- Toxicity Seven
Lesson 7
Outcomes:
- Identify the seven clues to the presence of hazardous materials.
- Explain how pre-incident plans, occupancy types, and locations may indicate the presence of hazardous materials.
Clues to the Presence of Hazardous Materials
Awareness level personnel and first responders must be able to analyze all incidents in order to detect and identify the presence of hazardous materials. Incidents involving hazmat can be controlled only when the personnel involved have sufficient information to make informed decisions. The time and effort devoted to identifying the contents of buildings, vehicles, and containers result in greater safety for first responders and the community. Historically, first responders’ failure to recognize hazardous materials at accidents, fires, spills, and other emer-gencies has caused unnecessary injuries and deaths. Once hazmat is detected, first responders can use a number of resources to identify it and its potential hazards. With that information, first responders can initiate appropriate response actions and perform them confidently. Some hazmat identification clues are easily visible at a distance while others require responders to be much closer. The closer you need to be in order to identify the material, the greater your chances of being in an area where you could be exposed to its harmful effects. In general, distance often equates to safety when hazmat is involved.
The following are the seven clues to the presence of hazardous materials:
- Occupancy types, locations, and pre-incident surveys
- Container shapes
- Transportation placards, labels, and markings
- Other markings and colours (non-transportation)
- Written resources
- Senses
- Monitoring and detection devices

The order of the clues also represents, in general, an increasing level of risk to responders (Figure 24.70). For example, using monitoring and detection equipment to identify hazmat is more likely to place responders in dangerous areas than using occupancy types or container shapes to provide information. Firefighters certified to NFPA 1001, Fire Fighter I should be able to identify hazardous materials based upon clues 1-6. Pre-incident Plans, Occupancy Types, and Locations Simply stated, hazardous materials may be found anywhere. Not all locations or occupancies are as obvious as the local chemical manufacturing plant, and you may have little or no warning when hazmat is transported through your area by road, rail, or waterway. However, pre-incident surveys and a structure’s occupancy type may provide the first clue that hazmat is involved in an incident. The location and occupancy may also be an indicator that terrorism is involved. In today’s world, a new and emerging problem is clandestine laboratories and illegal or legal grow operations. These laboratories may be located in any occupancy or location, including vehicles, campgrounds, and hotel rooms. These labs may be haphazardly assembled and are often booby-trapped.
The sections that follow will address:
- Pre-incident plans that identify where hazardous materials are used, stored, and transported
- Occupancy types which are likely to have hazardous materials
- Locations where hazmat incidents often occur
- Analyzing the Incident
Pre-incident Plans
Because hazmat incidents can be quite volatile, first responders may need to make decisions quickly and accurately. Conducting pre-incident surveys (also called pre-plans) and being familiar with local emergency response plans can simplify and reduce on-site decisions. With the groundwork laid, first responders can concentrate on the situation and operate more safely and efficiently. Preplanning reduces oversights, confusion, and effort duplication, and it results in a desirable outcome.
Furthermore, pre-incident surveys identify the following items:
- Exposures such as people, property, and environment
- Hazmat types, quantities, dangers, and locations
- Building features such as the location of fixed fire suppression systems
- Site characteristics
- Possible access/egress difficulties
- Inherent limitations of response organizations when trying to control certain types of hazmat emergencies
- Twenty-four hour telephone numbers of responsible parties and site experts
- Site or occupancy response capability
Planning is an ongoing process that includes reviewing surveys and updating them regularly. Preincident sur-veys are not always accurate, however, because inventories, businesses, and other factors may change without notice. Compliance with existing reporting rules and regulations cannot be guaranteed. Always expect to find the unexpected.
Occupancy Types
Certain occupancies are likely to have hazardous materials, including the following:

- Fuel storage facilities
- Gas/service stations and convenience stores
- Paint supply stores
- Plant nurseries, garden centres, and agricultural facilities
- Pest control and lawn care companies
- Medical facilities
- Photo processing laboratories
- Dry cleaners
- Plastics and high-technology factories
- Metal-plating businesses
- Mercantile concerns such as hardware stores, groceries stores, certain department stores
- Chemistry (and other) laboratories in educational facilities (including high schools)
- Lumberyards
Figure 24.72 Common household chemical products include gasoline, motor oil, paint, and insect repellant. - Feed/farm stores
- Veterinary clinics
- Print shops
- Warehouses
- Industrial and utility plants
- Port shipping facilities (with changing cargo hazards) (Figure 24.71)
- Treatment storage disposal (TSD) facilities
- Abandoned facilities that may have contained or used hazardous materials
- Big box retail stores
- Shipping depots
- Military installations

Residential occupancies have hazardous chemicals, such as drain cleaners, pesticides, fertilizers, paint products, flammable liquids (gasoline), swimming pool chemicals, propane tanks for gas grills, and other common household chemical products (Figure 24.72). Propane tanks often provide heating fuel, and farms may have dangerous products such as pesticides and anhydrous ammonia. Any building with a fume hood exhaust stack (or stacks) on the roof, such as a research and development company or medical office building, probably has a functioning laboratory inside (Figure 24.73). Locations Hazmat transportation accidents may be more likely to occur in certain areas. Places where hazmat is transferred or handled, such as trucking warehouses, are also likely locations for hazmat accidents.
These locations include:
- Ports
- Docks or piers
- Railroad sidings
- Airplane hangars
- Truck terminals
Consult with local law enforcement officials to identify and determine potential problem spots or areas based on traffic studies. Each transportation mode has particular locations where accidents may occur more frequently:
-
Figure 24.74 Locations that experience more transportation accidents in general, such as railway bridges and trestles, are also more likely to be involved in hazmat incidents. Courtesy of Phil Linder. Roadways
- Designated truck routes
- Blind intersections
- Poorly marked or poorly engineered interchanges
- Areas frequently congested by traffic
- Heavily traveled roads
- Sharp turns
- Steep grades
- Highway interchanges and ramps
- Bridges and tunnels
- Railways
- Depots, terminals, and switch or classification yards
- Sections of poorly laid or poorly maintained tracks
- Steep grades and severe curves
- Shunts and sidings
- Uncontrolled crossings
- Loading and unloading facilities
- Bridges, trestles, and tunnels (Figure 24.74)
- Waterways
- Difficult passages at bends or other threats to navigation
- Bridges and other crossings
- Piers and docks
- Shallow areas
- Locks
- Loading/unloading stations
- Airways
- Fuelling ramps
- Repair and maintenance hangars
- Freight terminals
- Crop duster planes and supplies
- Pipelines
- Exposed crossings over waterways or roads
- Pumping stations
- Construction and demolition sites
- Intermediate or final storage facilities

First responders should also pay attention to the water level in rivers and tidal areas.
Be aware of the following facts:
- Many accidents occur because flow volume and tidal conditions were not considered. These flow and tidal variances affect clearance under bridges, many of which also have pipelines, water mains, gas lines, and the like attached to them.
- Occupancies in low-lying areas that may be affected by flood conditions must have a contingency plan to isolate and protect hazardous materials (Figure 24.75).
- Tidal and flow conditions are constantly changing. Areas that were once considered safe may become compromised by change of tide direction, flow rate, and back eddies.
- Once a hazardous material reaches an outside water source, it becomes a moving incident and is extremely difficult to contain, confine, and mitigate.
First responders should be familiar with the types of hazmat shipments that come through their jurisdictions. For example, farming communities may be more likely to see tanks of anhydrous ammonia passing through, whereas a port serving an industrial complex with many refineries might see more petroleum products.
Lesson 8
Outcomes:
- Recognize general container types and their associated behaviours and hazards.

Container Types and Behaviour
Once you recognize that a location or occupancy may have hazardous materials, the presence of certain storage vessels, tanks, containers, packages, or vehicles can confirm their presence with certainty. These containers can provide useful information about the materials inside, so it is important for you to recognize the shapes of the different containers and packaging in which hazardous materials are stored and transported (Figure 24.76). Depending on the container and packaging type, hazardous material behaviour can vary.
Some basic generalizations may be made about a hazmat incident based on the type(s) of container involved. For example, if the incident involves a pressure container, any product released is likely to be a gas or a liquid that rapidly evaporates and expands into a gas or vapour. Once released, the hazardous material will behave like a gas depending on its properties and the environmental conditions at the scene. Table 24.4 provides a basic overview of the four major types of containers and their relationship to aspects of the General Behaviour Model.
In addition to the general container shapes, first responders should be familiar with the basic concepts of pressure and their measurements:
- Pounds per square inch (psi), kilopascal (kPa), bar: Common measurements for pressure in the English or Customary System, the International System of Units (SI), and the metric (non-SI) unit, respectively (Table 24.5). This manual uses psi (kPa) to describe pressure.
-
Figure 24.77 Atmospheric pressure measures the force exerted by the weight of the atmosphere. In this example, the greater the atmospheric pressure, the taller the column of mercury. Atmospheric pressure: Force exerted by the weight of the atmosphere at the surface of the earth. Atmospheric pressure is greatest at low altitudes; consequently, its pressure at sea level is used as a standard. At sea level, the atmosphere exerts a pressure of 14.7 psi (101 kPa). A common method of measuring atmospheric pressure is to compare the weight of the atmosphere with the height of a column of mercury: the greater the atmospheric pressure, the taller the column of mercury (Figure 24.77).
- Pressure at gauge: This describes a unit of pressure relative to the surrounding atmosphere. The Customary System unit is pounds per square inch gauge (psig). The International System of Units (SI) unit is kPaG; the metric (non-SI) unit is bar. For example, at sea level, a reading of 30 psig (207 kPaG){2.07 bar} on a tire gauge represents an absolute pressure of 44.7 psi (308 kPa){3.08 bar} because the gauge was calibrated to zero in atmospheric pressure of approximately 14.7 psi (101 kPa){1.01 bar}.
The sections that follow describe a variety of containers that first responders should be able to identify. Skill Sheet 24-1 provides steps to analyze a hazardous materials incident to identify potential hazards.
Containers by Transport Mode and Capacity
Hazmat containers are sometimes classified according to their transport mode (Table 24.6):
- Highway cargo trucks
- Rail cars
- Intermodal containers that transfer between modes
Containers can also be classified by their capacity. Bulk packaging refers to a packaging, other than that on a vessel (ship) or barge, in which materials are loaded with no intermediate form of containment. This packaging type includes a transport vehicle or freight container such as a cargo tank, railcar, or portable tank. Intermediate bulk containers (IBCs) and intermodal (IM) containers are also examples.
To meet the criteria for bulk packaging, one of the following must be met:
- Maximum capacity is greater than 119 gallons (475 L) as a receptacle for a liquid
- Maximum net mass is greater than 882 pounds (440 kg) or maximum capacity is greater than 119 gallons (475 L) as a receptacle for a solid
-
Figure 24.78 Bulk packaging allows large quantities of liquid, solid, or gas to be shipped. Water capacity is 1,001 pounds (500 kg) or greater as a receptacle for a gas
Non-bulk packaging is smaller than the minimum criteria established for bulk packaging (Figure 24.78). Drums, boxes, carboys, and bags are examples. Composite packages (packages with an outer packaging and an inner receptacle) and combination packages (multiple packages grouped together in a single outer container, such as bottles of acid packed inside a cardboard box) may also be classified as non-bulk packaging (Figure 24.79).
Highway Cargo Trucks
Highway vehicles that transport hazardous materials include:
-
Figure 24.79 Bottles of ethyl-alcohol are packaged inside a cardboard box, a form of non-bulk packaging. Cargo tank trucks (also called tank motor vehicles, cargo tanks, and tank trucks) (Figure 24.80)
- Dry bulk containers
- Compressed gas tube trailers
- Mixed load containers (also called box trucks or dry van trucks)
These vehicles transport all types of hazardous materials in a wide range of quantities. Depending on the type and quantity of hazardous material, these vehicles may have DOT/TC placards.Even unplacarded highway vehicles may be carrying quantities of hazardous materials, such as fuel in saddle tanks or other materials in levels below placarding requirements. Cargo tank trucks are recognizable because they have construction features, fittings, attachments, or shapes characteristic of their uses.

Even if first responders recognize one of the cargo tank trucks described in this section, the pro-cess of positive identification must proceed from placards to shipping papers or other formal sources of information. Cargo tank trucks commonly transport bulk amounts of hazardous materials via roadway. Most cargo tank trucks that haul hazardous materials are designed to meet government tank-safety specifications. These specifications set minimum tank construction material thicknesses, required safety features, and maximum allowable working pressures. Cargo tank specification and name plates provide information about the standards to which the container/tank was built (Figure 24.81).
These plates are usually found on the roadside/driver’s side of the vehicle near the dolly leg (landing gear). The two specifications in use are the motor carrier (MC) standards and DOT/TC standards.

Cargo tank trucks built to a given specification are designated using the MC or DOT/ TC initials followed by a three-digit number identifying the specification (such as MC 306 and DOT/TC 406). Emergency responders can recognize these cargo tank trucks by their required construction features, fittings, valves, attachments, and shapes, such as ring stiffeners on corrosive liquid tanks and bolted man-ways or manholes on high pressure tanks. Tanks not constructed to meet one of the common MC or DOT/TC specifications are commonly referred to as non-spec tanks.
Non-spec tanks may haul non-regulated hazardous materials if the tank was designed for a specific purpose and exempted from the DOT/TC requirements. Examples of non-regulated hazards include molten sulphur, asphalt, and milk. Nonhazardous materials may be hauled in either non-spec cargo tank trucks or cargo tank trucks that meet a designated specification (Figure 24.82). Rail Cars Rail tank cars carry the bulk of the hazardous materials transported by rail. Some railroad tank cars have capacities of 4,000 to 34,000 gallons (15 142 L to 128 704 L) (Figure 24.83).Because these cars carry large quantities, an accidental release of gases or liquids can cause many difficulties for responders.


By recognizing distinctive railroad cars, first responders can begin the identification process from the greatest possible distance. The type of car gives clues as to what material may be within, as well as the material’s weight and volume.
Tank cars are divided into the following three main categories:
- Low pressure tank cars, also known as general service tank cars and non-pressure tank cars
- Pressure tank cars
- Cryogenic liquid tank cars
**NOTE: Most of the following information on railroad tank cars is courtesy of A General Guide to Tank Cars, prepared by the Union Pacific Railroad, April 2009. **
Responders can receive valuable information from the markings on railroad tank cars as well as their contents:
- Reporting marks (railcar initials and numbers)
- Capacity stencil
- Specification marking
The ERG provides a key to these markings in the railcar identification chart, and more information is provided in sections that follow. Additionally, manufacturers’ names on cars may provide some contact information. Railcars are normally dedicated to transporting a single material. Dedicated tank cars may have the name of that material painted on the car. DOT/TC only requires a finite number of shipping names to be stencilled on the car. Some companies may also choose to include that information as a courtesy.
Reporting Marks
Tank cars, like all other freight cars, are marked with their own unique sets of reporting marks. Reporting marks (also called initials and numbers) may be used to obtain information about the car’s contents from the railroad’s computer, the shipper, CHEMTREC, CANUTEC, or SETIQ. Reporting marks should match the initials and numbers provided on the shipping papers for the car. They are stencilled on both sides (to the left when facing the side of the car) and both ends (upper centre) of the tank car tank (Figures 24.84 a and b). Some shippers and car owners also stencil the top of the car with the car’s reporting marks to help identify the car.



Capacity Stencil
The capacity stencil shows the volume of the tank car tank. The volume in gallons (and sometimes litres) is stencilled on both ends of the car under the car’s reporting marks. The capacity in pounds (and sometimes kilograms) is stencilled on the sides of the car under the car’s reporting marks. The term load limit may be used to mean the same thing as capacity in pounds or kilograms. For certain tank cars, the water capacity (water weight) of the tank, in pounds (and typically kilograms) is stencilled on the sides of the tank near the centre of the car (Figure 24.85).

Specification Marking
The specification marking indicates the standards to which a tank car was built. a The marking is stencilled on both sides of the tank. When facing the side of the car, the marking will be to the right (opposite from the reporting marks) (Figure 24.86). First responders can also get specification information from the railroad, shipper, car owner, or the Association of American Railroads by using the car’s reporting marks. Figure 24.87 provides a brief explanation of tank car specification markings.
Intermodal Containers
An intermodal container is a freight container that is used interchangeably in multiple modes of transport such as rail, highway, and ship.

The various types of intermodal containers can be divided into the following two main categories:
- Freight containers: Transport a wide range of products, from foodstuffs to dry goods. They come in a variety of types and sizes, most commonly in 20, 40, 45, 48, and 53 foot (6 m, 12 m, 14 m, 15 m, and 16 m) lengths.
- Several common types of freight containers are (Figure 24.88)
- Dry van intermodal containers (sometimes called box containers)
- Refrigerated intermodal containers (also called reefers)
- Open top intermodal containers
- Flat intermodal containers
- Several common types of freight containers are (Figure 24.88)
- Tank containers: Also called intermodal tanks (Figure 24.89).
- Three general classifications of intermodal tank containers are:
- Pressure intermodal tanks
- Specialized intermodal tanks such as cryogenic intermodal tanks and tube modules
- Low pressure intermodal tanks (also called non-pressure intermodal tanks)
- Three general classifications of intermodal tank containers are:


Some intermodal freight containers may contain hazardous materials (Figures 24.90a and b). Other intermodal freight containers may contain mixed loads that include both hazardous and nonhazardous materials. With many freight containers, you will not be able to determine by the shape of the container alone whether it contains hazardous materials. Instead, responders should use intermodal container markings or shipping papers (described later in this chapter) to identify the contents of these containers. Shipping papers may not be accurate, and hazardous materials may be shipped illegally in intermodal containers without proper identification. Intermodal tank containers generally have a cylinder enclosed at both ends. First responders may also see tube modules, cryogenic tanks, compartmentalized tanks, or other shapes. Table 24.7 provides examples of the most common types of intermodal tanks. The tank container is placed in frames to protect it and to allow stacking, lifting, and securing. The capacities of these containers ordinarily do not exceed 6,340 gallons (24 000 L) (Table 24.8).
In addition to required placards, Pressure Intermodal Tank 100 to 500 psi (689 kPa to 3 447 kPa). Reporting markings are generally found on the tank or container, on the right-hand side as you face it from either the sides or the ends. As with tank car reporting marks, you can use this information in conjunction with shipping papers or computer data to identify and verify the contents of the tank or container. Other markings on intermodal containers can also provide specification information (Figure 24.92).




Pressure Containers
Most people are familiar with com-pressed gas cylinders. Compressed gas cylinders are pressure containers, designed to hold product under pressure. The product may be a gas, liquefied gas, or a gas dissolved in a liquid (Figure 24.93). Pressure containers have the potential to release a great deal of energy if involved in an incident (Figure 24.94). For example, when stressed, pressure containers can rupture violently due to internal pressure. This can be accelerated if exposed to heat, flame, or mechanical damage.

When released, the product will expand rapidly and will travel based on the product’s physical and chemical properties and environmental conditions (Figure 24.95). You may not be able to see if the contents of a pressure container are leaking, nor where they might be going.
Pressure container examples are provided in Table 24.9. Regardless of size, transportation mode, or content, clues to pressure containers may include the following features:
- Rounded, almost spherical ends (Figure 24.96)
- Bolted manways (Figure 24.97)
- Bolted protective housings (Figure 24.98)
- Pressure relief devices (Figures 24.99 a and b)
- Pressure gauges (Figure 24.100)





First responders at hazmat incidents involving pressure containers need to consider the following common stressors:
- Thermal: Exposure to heat or flame can cause pressure containers to BLEVE.
- Chemical: Released corrosive gases can cause additional damage to the container; pressure on the container can increase by the reactions of the contents.
- Mechanical: Accidents may cause mechanical stress, particularly to the container fittings.
Pressure containers can experience any type of breach, although releases from pressure relief devices and/or damaged fittings are most common. Runaway cracking is associated with BLEVEs. Punctures, splits, and tears are rare, although violent accidents such as railway derailments or highway accidents may involve enough force to damage welded seams or cause punctures through pressure container walls. Pressure containers release rapidly expanding gases or liquids that quickly evaporate and expand into gases or vapours. Releases can occur through pressure relief devices (rapid relief) or as leaks through damaged attachments and fittings.
Common dispersion patterns from pressure containers include:
- Hemispheric pattern: BLEVE
- Cloud: A cloud above the container if there is little wind and the release is intermittent or short in duration
- Plume: Depending on vapour density, terrain (particularly if vapour density is greater than 1), and wind speed
- Cone: A steady release of product from a pressure container as it expands from the point of release outward. The cone will be directed downwind in accordance with the prevailing wind direction.

Bulk Facility Pressure Tanks
Fixed facility pressure tanks have pressures of 15 psi (105 kPa) or greater. Examples of pressure containers include horizontal pressure vessels and spherical pressure vessels (Table 24.10). These tanks typically release their products as gases and vapours during rapid relief events, slow leaks from valves and fittings, or violent ruptures (Figure 24.101). Pressure tanks may contain a variety of flammable, toxic, and/or corrosive gases. Pressure tanks are especially dangerous when subjected to heating or fire because they can BLEVE.
Contents leaking from these containers may expand rapidly and displace oxygen, especially in confined spaces. Flammable gases may travel far distances where they can ignite if exposed to an ignition source. Toxic gases may travel far distances and affect people and animals well away from the incident scene.

High Pressure Tank Trucks
High pressure tank trucks are also known as MC-331 (or equivalent) cargo tanks. These tank trucks have pressures typically between 100 to 500 psi (690 to 3 448 kPa) with typical capacities between 3,000 to 11,000 gallons (11 356 to 41 640 L). High pressure cargo tanks have a single, steel compartment. High pressure tank trucks transport liquefied gases, such as propane, anhydrous ammonia, and butane, or high vapour pressure liquids and highly hazardous materials such as parathion. High-pressure “Bobtail Tanks” are used for local delivery of liquefied petroleum gas and anhydrous ammonia (Figure 24.102)

MC-331 cargo tank trucks have the following features:
- Bolted manway
- Inlet and outlet valves
- White or other reflective paint scheme (typically)
- Large hemispherical heads on both ends
- Guard cage around the bottom loading/unloading piping (Figure 24.103)
- Uninsulated tanks, single-shell vessels
- Emergency shut-offs (typically located in the left front and right rear)
- Permanent markings such as flammable gas, compressed gas, shipping name, or identifiable manufacturer or distributor names

Compressed-Gas/Tube Trailers
Compressed-gas/tube trailers transport individual steel cylinders stacked and mounted together. Typical pressures in the tubes range from 2,400 to 5,000 psi (16 547 to 34 474 kPa) (gas only). Each cylinder typically has an overpressure device.
Compressed-gas/tube trailers carry helium, hydrogen, methane, oxygen, and other gases. Often, they are parked or located at the facility where the gas is used, much like a semi-permanent storage tank (Figure 24.105).
Compressed-gas/tube trailers typically have the following features:
- A pressure relief device (PRD) for each cylinder (Figure 24.106)
-
Figure 24.105 Compressed-gas/tube trailers may be permanently parked at a facility. Bolted manway at front or rear
- Valves in a protected housing (Figure 24.107)
- Valves manifolded together (Figure 24.108)
- Permanent markings for the material or ownership that is locally identifiable, including proper shipping name
Compressed-gas/tube trailers may experience disintegration, runaway cracking, damage to attachments, punctures, splits or tears. They may release via violent rupture, rapid relief, or leaks. When exposed to heat or flames, they may BLEVE. Flammable gases may explode/ignite when coming into contact with an ignition source. Because of the high pressures in the tubes, accidental releases from these trailers can be violent, and released gases will expand rapidly.

Pressure Tank Cars
Pressure tank cars typically transport flammable, nonflammable, and poisonous gases at pressures greater than 25 psi (172 kPa) at 68°F (20°C) (Figure 24.109). They also transport flammable liquids and liquefied compressed gases. Tank test pressures from these tank cars range from 100 to 600 psi (689 to 4 137 kPa). Pressure tank car capacities range from 4,000 to 34,000 gallons (15 142 to 128 704 L).
**NOTE: Though less common, some older jumbo cars can have a capacity of up to 50,000 gal (189 271 L).**
Pressure tank cars often have the following features:

- Cylindrical.
- Non-compartmentalized.
- Metal (steel or aluminum).
- Rounded ends (heads).
- Top-loading cars.
- Out-of-sight fittings (loading/unloading, pressure-relief, and gauging)
- Located inside the protective housings mounted on the man-way cover plates in the top centre of the tanks.
- Pressure tank cars typically have all fittings out of sight under the single protective housings on top of the tanks (Figure 24.110).
- May be insulated and/or thermally protected (Figure 24.111).


New pressure tank cars have greater accident protection features and will withstand greater damage without leaking. They feature thicker walls, a lower profile of protective housing, and higher tank test pressures. New pressure tank cars are significantly heavier than old cars, and they may also be equipped with GPS tracking devices and anti-tampering mechanisms (Figure 24.112).
** NOTE: Several highly hazardous liquids are shipped in pressure cars that have little to no vapour pressure. **

Pressure tanks are subject to thermal, mechanical, and chemical damage that will release expanding gases or vapours. Because capacities are so large, affected areas and evacuation zones may be quite large. When exposed to heat or flame, pressure tank cars may BLEVE. Per the ERG, the initial isolation zone for a pressure tank car involved in fire is one mile (1.6 km) (Figure 24.113).
Pressure Intermodal
Tanks A pressure intermodal tank container is less common in transport. DOT/TC classifies this tank as Spec. 51; internationally it is known as an IMO Type 5 tank container (Figure 24.114). This type of container is designed for MAWPs of 100 to 500 psi (689 to 3 447 kPa) and usually transports liquefied gases under pressure.


Pressure intermodal tanks may be damaged during transport, loading, and unloading. Leaks frequently involve the fittings, with the release of rapidly expanding gases or vapours. Pressure intermodal tanks exposed to heat and/or flame may BLEVE .



Ton Containers
Ton containers are pressure tanks that have capacities of 1 short ton or approximately 2,000 pounds (907 kg or 0.91 tonnes). They are typically stored on their sides (Figure 24.115). The ends (heads) of the containers are convex or concave, and they have two valves in the centre of one end, one above the other. One valve connects to a tube that extends into the liquid space; the other valve connects to a tube that extends into the vapour space above (Figure 24.116).

Ton containers may have pressure-relief devices or fusible plugs in case of fire or exposure to elevated temperatures. Ton containers holding chlorine are often found at locations such as water treatment plants and commercial swimming pools. Ton containers may also contain products such as sulfur dioxide, anhy-drous ammonia, or Freon® refrigerant. As pressure containers, ton containers typically release their contents as gases or vapours. Always evacuate responders and civilians to a safe distance to avoid the vapour cloud that escapes from these containers. Because products stored in ton containers are often highly toxic and/or corrosive, evaluate available PPE for effectiveness during incidents involving these containers (Figure 24.117).

Y Cylinders/Y Ton Containers
Y cylinders are a type of compressed gas cylinder that can be bulk or non-bulk, but they are typically classified as bulk (Figure 24.118). A typical Y ton container will have a specification such as DOT/TC 3AA-2400 or DOT/TC 3AA-480 (pressure is dependent on product). These containers are typically 7 feet (2 m) long, 2 ft (0.6 m) in diameter, have a wall thickness of about 0.6 inches (15 mm), and, when empty, weigh about 1,200 lbs (544 kg). These containers have a water capacity of approximately 120 gallons (454 liters), or 16 cubic feet (0.5 m3). Often used for refrigerants, they typically operate in a cascade system.
Y cylinders/Y ton containers have two specifications depending on size:
- DOT/TC–3AA: A seamless steel cylinder with a water capacity (nominal) of not over 1,000 lbs (454 kg) and a service pressure of at least 150 psig (1 034 kPaG).
- DOT/TC–3AAX: A seamless steel cylinder with a water capacity of not less than 1,000 lbs (454 kg) and a service pressure of at least 500 psig (3 447 kPaG).

Cylinders
A cylinder is a non-bulk, pressure vessel designed for pressures higher than 40 psi (276 kPa) and has a circular cross section, but it does not include any of the containers, tanks, or vessels described in previous sections. Cylinders are used to store, transport, and dispense large volumes of gaseous materials. Compressed-gas cylinders range in size from small lecture bottles (small bottles used for classroom demonstrations) to large cylinders and have varying pressures. All approved cylinders, with the exception of some that store poisons, are equipped with safety-relief devices. These devices may be spring-loaded valves that reclose after operation, heat-fusible plugs, or pressure-activated bursting disks that completely empty the container. All fittings and threads are standardized according to the material stored in the cylinder. As yet, there is no nationally regulated colour code that permits visual identification of cylinder materials by colour. Some manufacturers use a single colour for all their cylinders, while other manufacturers have their own colour-coding system. If local manufacturers and distributors use an identification system, it should be identified in emergency response plans.

Cryogenic Containers
Cryogenic containers are designed to store and transport cryogens. A cryogen (sometimes called refrigerated liquefied gas) is a gas that turns into a liquid at or below -130°F (-90°C) at 14.7 psi (101 kPa) {1.01 bar}. These containers may be pressurized, though not to the degree that pressure containers are. When released, cryogens may transition from a liquid state to a vapour state. This reaction may happen rapidly, and a spill or leak will boil into a much larger vapour cloud (Figure 24.119). These vapour clouds may be flammable, toxic, corrosive, or an oxidizer. Some cryogens may present multiple hazards. Additionally, cryogenic vapours can be extremely cold, potentially causing freeze burns, which are treated as cold injuries according to their severity. Any clothing saturated with a cryogenic material must be removed immediately. This action is particularly important if the vapour is flammable or an oxidizer. A first responder cannot escape flames from clothing-trapped vapours if they ignite.
Cryogenic container examples are provided in Table 24.11. Regardless of size, transportation mode, or content, indications of cryogenic containers may include the following:
- Contents such as liquid oxygen (LOX), nitrogen, helium, hydrogen, argon, and liquefied natural gas (LNG) (Figure 24.120)
- Box-like loading and unloading stations attached to transportation containers (Figure 24.121)
Like pressure containers, cryogenic containers are solidly constructed to prevent accidental releases. Insulation between the exterior and the interior walls of the container keeps the product cool but does not provide protection against breaches. The container’s external support structure is not designed to handle the temperatures inside the container.


Common stressors to consider at hazmat incidents involving cryogenic containers include:
- Thermal: If a breach occurs, the extreme cold of the released product may cause damage to the container or fittings. When ex-posed to heat or flame, cryogenic containers can BLEVE, although this is unusual. If vacuum is lost, the container will heat rapidly and may blow the rupture disc/ relief valve. If the system cannot relieve pressure quickly enough, the container may rupture. Damage to the outer jacket and insulation may result in loss of vacuum.
- Chemical: Normal stresses are due to exposure from the out-side contact on the container. An incorrect chemical added to a cryogenic tank may cause corrosion.
- Mechanical: Accidents may cause mechanical stress, particularly to the container fittings. Severe accidents may cause dam-age to container walls, creating loss of vacuum within the vacuum space of the container.
**NOTE: Venting is a function of some cryogenic containers and may not indicate a system failure. **

Cryogenic containers can experience any type of breach, although releases from pressure relief devices and/or damaged fittings are most common. Punctures, splits, and tears are rare, although violent accidents, such as railway derailments or highway accidents, may involve enough force to damage both exterior and interior container walls.
Cryogenic containers are designed to handle extremely cold temperatures; however, the external support struc-ture of the container is not designed to do so. If cryogenic materials leak, the support structure can fail without warning due to stress failures. If other containers are involved in a wreck or derailment with cryogenic containers, leaks from the cryogenic containers may cause failure of other containers due to cold stress. Cryogenic containers release cold liquids or vapours that rapidly boil into expanding gases (Figure 24.122).
Common releases occur through pressure relief devices (rapid relief) or as leaks through damaged attachments and fittings. Typical dispersion patterns from cryogenic containers include:

- Hemispheric
- Cloud
- Plume
- Pool
Bulk Facility Cryogenic Liquid
Tanks Cryogenic liquid storage tanks may have pressures of 15 psi (103 kPa){1.03 bar} or greater, with capacities from 300 to 400,000 gallons (1 136 to 1 514 165 L). They have insulated, vacuum-jacketed tanks with safety relief valves and rupture disks. These tanks may contain cryogenic carbon dioxide, liquid oxygen, liquid nitrogen, or other materials (Figures 24.123 a-c.).
**NOTE: Some new Liquefied Natural Gas (LNG) tanks have a capacity of 30 to 60 million gallons (114 to 227 million litres). **
Materials released from bulk cryogenic liquid tanks will be very cold, and therefore will tend to pool close to the ground. Typically, they will initially be visible as a fog or cloud. Most types of cryogenic leaks will displace oxygen. Some will create an explosive environment.
Cryogenic Tank Trucks
Cryogenic tank trucks are also known as MC338, TC338, or SCT-338 (or equivalent) cargo tanks. These tank trucks have pressures that can be less than 25 and up to 500 psi (172 to 3 447 kPa), and capacities of 8,000 to 10,000 gallons (30 283 to 37 854 L). These trucks have well-insulated aluminum or steel tanks with vacuum-sealed shells.

These tank trucks transport the following gases that have been liquefied by lowering their temperatures, including:
- Liquefied oxygen
- Liquefied nitrogen (Figure 24.124)
- Analyzing the Incident
- Liquefied carbon dioxide
- Liquefied hydrogen
When released, the product will be extremely cold and therefore will tend to pool close to the ground. Typically, the product will initially be visible as a fog or cloud because of the condensation of humidity and ice formation. As they warm, these liquids will change into gas and expand.

MC-338 cryogenic tank trucks have the following features:
- Relief valves that may be discharging nonhazardous vapour such as nitrogen or oxygen (Figure 24.125)
- Round tank with flat ends
- Large and bulky double shelling and heavy insulation
- Loading/unloading station attached either at the rear or in front of the rear dual wheels
- Permanent markings such as refrigerated liquid or an identifiable manufacturer name, proper shipping name
- Emergency shutoffs on the left-front and right-rear

Cryogenic tank trucks may experience disintegration, runaway cracking, damage to attachments, punctures, splits or tears. They may release via violent rupture, rapid relief, or leaks. When exposed to heat or flames, they may BLEVE (Figure 24.126).
Cryogenic Liquid Tank Cars
Cryogenic liquid tank cars carry low pressure (usually below 25 psi [172 kPa]) refrigerated liquids (-130°F and be-low [-90°C and below]). Materials found in these tanks include argon, hydrogen, nitrogen, and oxygen. Liquefied natural gas (LNG) and ethylene may be found in these containers at somewhat higher pressures. Cryogenic liquid tank cars often have fittings for loading/unloading, pressure relief, and venting in ground-level cabinets on the sides of the car or the end of the car (Figure 24.127).

A cryogenic liquid tank car is in the tank-within-a-tank category with a stainless steel inner tank supported within a strong outer tank. The space between the inner tank and outer tank is filled with insulation. This space is also kept under a vacuum. The combination of insulation and vacuum protects the contents from ambient temperatures for only 30 days. The shipper tracks these time-sensitive shipments. Per the ERG, the initial isolation zone for a cryogenic liquid tank car is 1⁄2 mile (1 km).

Cryogenic Intermodal
Container There are several types of specialized intermodal tank containers. Cryogenic-type containers are built to IMO Type 7 specifications (Figure 24.128). Cryogenic liquid tank containers carry refrigerated liquid gases, argon, oxygen, and helium.

Dewar
A dewar flask (vacuum flask) is a non-bulk, non-pressurized, insulated container that has a vacuum space between the outer shell and the inner vessel (Figure 24.129). The dewar flask is designed for the storage and dispensing of cryogenic materials such as liquid nitrogen, liquid oxygen, and helium. Dewars have a bulky appearance due to the insulation used to keep the cryogenic material at the desired temperature. The volume of dewar flasks is often between 4 gallons to 125 gallons (15 to 500 L). Some dewar flasks may be as large as 1,250 gallons (5,000 L).
Liquid-Holding Containers
Common liquid containers include bottles, gasoline containers, paint pails, and drums. However, at fixed facilities, liquids can be stored in containers that hold many millions of gallons (litres). Large quantities are also transported in tanks via highway, rail, and other modes.
Many liquid containers will have some pressure due to the liquid’s chemical and physical properties, but these pressures will be lower than a pressurized container’s. Although the pressures may be low, they can still be dangerous. Liquid containers may hold contents that have a variety of hazards including pressure, heat (often, their contents will burn), reactivity, corrosivity, and toxicity. Some liquid containers, when exposed to heat or flames, may rupture violently or explode.
Regardless of size, transportation mode, or content, indications of liquid containers may include the following features: (Figure 24.130):
- Flat (or less rounded) ends on tanks
- Access hatches secured with easily removed latching devices
- Low pressure rail tank cars may have multiple fittings visible on top
- Intermodal, flexible intermediate bulk containers (IBC), and rigid intermediate bulk containers are designed to be stacked
- Flexible bladders filled with fluids
- Highway cargo tanks will have oval, upside-down horseshoe-shaped, or circular-shaped ends with less round-ing than pressure tanks

Liquid-holding containers come in a variety of designs and construction types depending on:
- Size
- Mode of transport
- Material contained
- Use
- Other factors
Liquid-holding containers may have the following characteristics:
- Extremely durable, such as a tank car
- Fragile, such as a glass bottle
- May fail when subjected to fires
- Less likely to fragment as they BLEVE
- Transport materials that polymerize
- Uncontrolled polymerization (chemical stress) may create enough stress to cause container failure
- Explosive in nature
While streams and pools are common dispersion patterns for liquids, many liquids also release vapours that act like gases. All dispersion patterns can be associated with liquids depending on the product and container. Bulk Facility Low Pressure Storage Tanks Low pressure storage tanks have operating pressures from 0.5 to 15 psi (3.5 to 103 kPa).
Types of low pressure storage tanks include (Table 24.12):
- Dome roof tanks
- Spheroid tanks
- Noded spheroid tanks
Low pressure storage tanks typically contain flammable and combustible liquids with low vapour pressures, such as solvents. Flammability and/or toxicity are often hazards associated with the products stored in these containers. Low pressure tanks can release their products as liquids or as gases and vapours depending on the product contained. The priority is eliminating ignition sources at incidents involving these containers. Bulk Facility Non-pressure/ Atmospheric Storage Tanks Non-pressure/atmospheric storage tanks are designed to hold contents under little or no pressure (Table 24.13). The maximum pressure under which an atmospheric tank is capable of holding its contents is 0.5 psi (3.45 kPa).
Common types of atmospheric tanks include:
- Horizontal tanks
- Lifter roof tanks
- Ordinary cone roof tanks
- Vapour dome roof tanks
- Open and closed roof floating-roof tanks
Non-pressure/atmospheric storage tanks typically hold liquids, most often hydrocarbons. This liquid may be flammable/combustible such as fuel oil or other petroleum products, or corrosive and/or toxic, such as sulfuric acid and aniline.
Bulk Facility Low Pressure Storage Tanks
Low pressure storage tanks have operating pressures from 0.5 to 15 psi (3.5 to 103 kPa). Types of low pressure storage tanks include (Table 24.12):
- Dome roof tanks
- Spheroid tanks
- Noded spheroid tanks
Low pressure storage tanks typically contain flammable and combustible liquids with low vapour pressures, such as solvents. Flammability and/or toxicity are often hazards associated with the products stored in these containers. Low pressure tanks can release their products as liquids or as gases and vapours depending on the product contained. The priority is eliminating ignition sources at incidents involving these containers. Bulk Facility Non-pressure/ Atmospheric Storage Tanks Non-pressure/atmospheric storage tanks are designed to hold contents under little or no pressure (Table 24.13). The maximum pressure under which an atmospheric tank is capable of holding its contents is 0.5 psi (3.45 kPa).
Common types of atmospheric tanks include:
- Horizontal tanks
- Lifter roof tanks
- Ordinary cone roof tanks
- Vapourdome roof tanks
- Open and closed roof floating-roof tanks
Non-pressure/atmospheric storage tanks typically hold liquids, most often hydrocarbons. This liquid may be flammable/combustible such as fuel oil or other petroleum products, or corrosive and/or toxic, such as sulfuric acid and aniline.



Damaged non-pressure/atmospheric storage tanks release their contents via spilling or leaking through container walls, valves, fittings, and attachments. Depending on the product, vapours, which are often heavier than air, may travel some distance from their liquid source. Treat interiors of bulk non-pressure/atmospheric storage tanks as confined spaces. Even when empty, these containers are likely to have dangerous atmospheres (Figure 24.131). Follow special procedures when operating in and around them. Underground Storage Tanks Underground storage tanks are typically constructed of steel, fibreglass, or steel with a fibreglass coating (Figure 24.132).
Other features of underground storage tanks include:
- They usually contain liquids (typically, gasoline).
- They are classified as low pressure or non-pressure/atmospheric.
- More than ten percent of their surface areas are underground.
- They can be buried under or adjacent to a building or driveway.
Underground tanks have fill and vent connections located nearby (Figure 24.133). Vents, fill points, and occupancy type (gas/service stations, private garages, and fleet maintenance stations) provide visual clues to the presence of underground tanks.
Many commercial and private underground tanks have been abandoned, some with product still in them. Leaking underground storage tanks may go undetected until they leak into an undesirable location in liquid or vapour form. Fires and/or explosions can occur if flammable materials contact an ignition source.
** NOTE:Some horizontal propane pressure tanks have been buried underground. **

Low Pressure Chemical Tank
Trucks Low pressure chemical tank trucks are also known as MC-307 or DOT/TC-407 (or equivalent) cargo tanks de-pending on the specifications to which they were built (Figure 24.134). These tank trucks typically have a pressure of 25 to 35 psi (172 to 241 kPa), with typical capacities of 5,500 to 7,000 gallons (20 820 L to 26 500 L). Most have a stainless steel, mild steel, or aluminum tank and some may have a rubber lining, rubber coating, or polymer coating. Low pressure chemical tank trucks carry liquids, including flammable/combustible liquids, mild corrosives, and some toxics/poisons. Liquids and vapours may have a variety of hazards depending on the product(s) being transported.

MC-307 or DOT/TC-407
cargo tanks have the following features:
- Rounded or horseshoe-shaped ends
- Stiffening rings that may be visible or covered (Figure 24.135)
- Rollover/turnover protection
- Single or multiple compartments
- Manway assembly protected by the rollover/turnover protection (crash box)
- Discharge piping at midship or rear
- Rear or middle unloading
- Pressure and vacuum protection
- Drain hose from the rollover/turnover protection down the side of the tank
- Emergency shutoffs (hydraulic or pneumatic) located on the left front of the tank
Low pressure chemical tanks can be breached by damage to attachments, punctures, splits or tears. When involved in fire or unusual chemical reactions, they are unlikely to rupture violently. More commonly, these cargo tanks are involved in liquid spills or leaks (Figure 24.136).



Non-pressure Cargo Tank
Trucks Non-pressure cargo tank trucks are also known as MC-306 or DOT/TC-406 (or equivalent) cargo tanks depending on the specifications to which they were built. New tanks are constructed of aluminum or steel, but older tanks are made of steel. Typical pressure in these tanks is less than 4 psi (28 kPaG). The maximum capacity of these tanks is 14,000 gallons (53 000 L) in the U.S., with a typical capacity range between 1,500 to 10,000 gallons (5 678 to 37 854 litres). Non-pressure cargo tanks almost always carry flammable/combustible liquids such as gasoline, fuel oil, alcohol, or other nonhazardous liquids. Individual compartments may carry different products. Fire control will be a primary concern at incidents involving these vehicles (Figure 24.137).
MC-306 or DOT/TC-406 cargo tanks have the following features:
- Oval shape
- Manways located in overturn protection areas
- Bottom valves
- Longitudinal rollover protection
- Valve assembly and unloading control box under tank (Figure 24.138)
- Vapour-recovery system on curb side and rear, if present
- Multiple compartments
- Manway assemblies and vapour-recovery valves on top for each compartment
- Emergency shut-off systems
Non-pressure cargo tanks can be breached by punctures, splits, tears, or damage to attachments (Figure 24.139). When involved in fire, steel tanks can rupture violently; aluminum tanks will melt. More commonly, these cargo tanks are involved in liquid spills or leaks.

Corrosive Liquid Tank Trucks
Corrosive liquid tank trucks are also known as MC-312 or DOT/TC-412 (or equivalent) cargo tank trucks de-pending on the specifications to which they were built. These tank trucks typically have a pressure range of 35 to 55 psi (241 to 379 kPa) and may have a much higher maximum allowable working pressure (MAWP). Typical tank capacities are from 3,300 to 6,300 gallons (12 492 to 23 848 liters). Aluminum, mild steel, stainless steel, and fibreglass reinforced plastics (FRP) tanks can be rubber or polymer lined. The outer jacket may be aluminum or stainless steel and often covers a layer of insulation. Usually, these tank trucks only have one compartment.

Corrosive liquid tank trucks carry corrosives, typically acids such as acetyl chloride, hydrochloric acid, and sodium hydroxide (Figure 24.140). Avoid contact with corrosive liquids and vapours. Be aware that corrosives can damage tools and equipment, including firefighter protective clothing.
MC-312 or DOT/TC-412 corrosive liquid tank trucks may have the following features:
- Small-diameter round shape
- Exterior stiffening rings (may be visible on uninsulated tanks)
- Top unloading on the rear of the tank with exterior piping extending to the bottom of the tank.
- Rollover protection around the valve assembly
- A pressure relief device (PRD) typically located in turnover protection.
- Discoloured loading/unloading area
- An area painted or coated with corrosive-resistant material (Figure 24.141)

Corrosive liquid tank trucks can be breached by damage to attachments, punctures, splits or tears (Figure 24.142). Most commonly, these cargo tanks are involved in liquid spills or leaks, but on rare occasions chemical reactions can cause violent ruptures.

Low Pressure Tank Cars
Low pressure tank cars transport hazardous and nonhazardous solids and liquids with vapour pressures below 25 psi (172 kPa) at 105°F to 115°F (41°C to 46°C) (Figure 24.136). Tank test pressures for low pressure tank cars are
60 and 100 psi (414 and 689 kPa). Capacities range from 4,000 to 34,000 gallons (15 142 to 128 704 litres) in newer tanks made of aluminum, mild steel, or stainless steel. NOTE: Though less common, some older jumbo cars can have a capacity of up to 45,000 gal (170 344 L).

Low pressure tank cars transport hazardous materials, such as:
- Flammable liquids
- Reactive liquids
- Oxidizers (Figure 24.144)
- Poisons
- Flammable solids
- Reactive solids
- Organic peroxides
- Irritants
- Corrosive materials

They also transport nonhazardous materials, such as:
- Fruit and vegetable juices
- Wine and other alcoholic beverages
- Tomato paste
- Other agricultural products
Low pressure tank cars have the following features:
- Cylindrical with rounded ends (heads)
- At least one manway for access
Figure 24.145 This low pressure tank car has two tanks. These may carry separate products. Courtesy of Rich Mahaney. to the tank’s interior
- Compartmentalized with up to six compartments constructed as distinct tanks, each with its own set of fit-tings, capacity, and ability to transport a different commodity (Figure 24.145)
- Fittings for loading/unloading, pressure and/or vacuum relief, gauging, and other purposes visible at the top and/or bottom of the car (Figure 24.146)
For many years, one method for identifying low pressure tank cars was to look for multiple fittings and equipment on top of the tank car. However, some new DOT/TC 111 tank cars enclose some or all of those fittings inside a protective housing similar to a pressure car (see previous section). First responders must now look at the top of the car and, if a single protective housing is present, they must verify whether it is a high-pressure tank car or a DOT 111 tank car by identifying the DOT/TC specifications stencilled on the right-hand side of the car (Figures 24.147 a and b)



Trains transporting multiple low pressure tank cars containing ethanol, crude oil, and other Class 3 products may be called High-Hazard Flammable Trains (HHFT) (Figures 24.148 a and b). When involved in accidents, these tank cars can release their products, ignite, and violently rupture. These types of accidents are primarily attributed to human error. In addition to DOT/TC 111 tank cars, new DOT/TC 117 and DOT/TC 120 tanks cars may be encountered (Figures 24.149 a-c).


Low Pressure Intermodal Tank
This tank is the most common intermodal tank used in transportation. Even though they are often called non-pressure intermodal tanks, these tanks may have pressures as high as 100 psi (689 kPa). They are also called intermodal portable tanks or IM portable tanks.
The two common groups of low pressure/non-pressure intermodal tank containers are:
- IM 101 portable tanks: Internationally, these are called International Maritime Organization (IMO) Type 1 tank containers (Figure 24.150). They are built to withstand maximum allowable working pressures (MAWP) of 25.4 to 100 psi (175 to 689 kPa). They transport both hazardous and nonhazardous materials.
- IM 102 portable tanks: Internationally, these are called IMO Type 2 tank containers. They are designed to handle maximum allowable working pressures (MAWP) of 14.5 to 25.4 psi (100 to 175 kPa). These contain-ers are gradually being removed from service. They transport materials such as alcohols, pesticides, resins, industrial solvents, and flammables with flashpoints between 32 and 140°F (0° to 60°C). Most commonly, they transport non-regulated materials such as food commodities.
Low pressure intermodal tanks may be damaged during transport, loading, and unloading, including dam-age to fittings and container walls. Releases are commonly in the form of spilled liquids, often flammable or combustible.
Carboys and Jerricans
A carboy is a large, non-bulk, glass or plastic bottle encased in a basket or box, primarily used to store and trans-port corrosive liquids, although its use has expanded to nonhazardous materials (such as water) as well. The outer packaging may be made of such materials as polystyrene or wood, and carboys may be round or rectangular. Their capacities may exceed 20 gallons (76 L), but 5-gallon (19 L) containers are more common. Jerrican is another name for a nonbulk, rectangular plastic carboy and is the term used in UN regulations. Some organizations differentiate between carboys and jerricans, defining jerricans as rectangular metal containers typically transporting flammable and combustible liquids and carboys as transporting corrosives.

Solids-Holding Containers
Many containers used to hold liquids may also be used for solids, for example, drums and bottles. Some transportation containers are specially designed for loading and unloading solids, and certain fixed facilities may store solids that are not typically deemed “hazardous” but may present a threat anyway, such as grain silos and storage facilities.
Hazardous solids may be dusts, powders, or small particles. Solids containers typically do not carry any pressure. A powder pesticide is an example of a potentially toxic solid. Boric acid and sodium hydroxide are corrosive solids. Dynamite is an energy-releasing solid. Calcium carbide is a reactive material that, when in contact with moisture, will release a flammable gas. Small, airborne particles that burn (but may otherwise be harmless) can be dangerous if ignited in an enclosed location, causing a dust explosion. Grain, flour, sugar, coal, metal, and saw dust are examples of these particles. For that reason, you should be aware that fixed facilities where these materials are used, processed, or stored should be considered “containers” for purposes of this section. Solid materials can also engulf you, causing suffocation and/or crushing injuries. These situations are typically associated with soil/dirt, sand, and gravel, but are also a concern at incidents involving large containers of grain, powdered substances, or any “flowing” solids.

Regardless of size, transportation mode, or content, indications of solids containers may include the following features:
- Transportation containers and systems designed for pneumatic loading and unloading (Figure 24.151 a and b)
- Open tops on hoppers, bins, or other containers, sometimes covered with tarps or plastic (Figure 24.152)
- V-shaped sloping sides with bottom outlets
Most solids-holding containers will be damaged via mechanical stressors rather than the physical properties of the materials contained in them. Exceptions include reactive materials such as oxidizers, peroxides, explosives, and water reactive materials. Common breaches of solids holding containers include punctures, splits, and tears. Pneumatic loading and unloading attachments may be damaged in accidents.

Common releases result in the following:
- Spills and leaks (Figure 24.153): Materials release at a steady pace without explosive force
- Detonation: Occurs when oxidizers, peroxides, explosives, and water-reactive materials are involved
- Violent ruptures: Reactive solids release
- Clouds, cones, or via irregular dispersion: Solids may disperse
- Explosions: Detonated explosives disperse in a hemispheric dispersion

Dry Bulk Cargo Trailers Dry bulk cargo trailers transport solids, including hazardous solids such as oxidizers, corrosive solids, cement, plastic pellets, and fertilizers (Figure 24.154). While contents are not usually under pressure, low pressures between 15 to 20 psi (103 to 138 kPa) may be used to discharge or transfer the product from the container. These cargo trailers are constructed to transport heavy loads, but damage to attachments, punctures, splits, or tears may occur if they are involved in an accident.
Dry bulk cargo trailers have the following features:
- Typically not under pressure
- Varying shapes that often include bottom valves with V-or W-shaped bottom-unloading compartments (Figure 24.155)
- Rear-mounted, auxiliary-engine-powered compressor or tractor-mounted power-take-off air compressor
- Air-assisted, exterior loading and bottom unloading pipes
- Top manway assemblies

Dry Bulk Railroad Cars
Other railroad cars include hopper cars and miscellaneous cars such as boxcars and gondolas. Descriptions of these cars are as follows:
- Covered hopper cars: Often transport dry bulk materials suchas grain, calcium carbide, ammonium nitrate, and cement (Figure 24.156).
- Uncovered (or open top) hopper cars: May carry coal, sand, gravel, or rocks (Figure 24.157).
- Pneumatically unloaded hopper cars: Unloaded by air pressure and used to transport dry bulk loads such as ammonium nitrate fertilizer, dry caustic soda, plastic pellets, and cement. Pressure ratings during unload-ing range from 20 to 80 psi (69 to 552 kPa) (Figures 24.158 a and b).
- Miscellaneous cars: Boxcars and gondolas, well cars, and spine cars often used to carry containers of hazardous materials. These cars can include mixed cargos of a variety of products in different types of packaging (Figure 24.159), so responders may have to deal with gas, liquid, or solids releases.


** NOTE: Cars may be fumigated, presenting additional hazards. Bags A bag is a non-bulk flexible packaging made of paper, plastic film, textiles, woven material, or other similar materials. **

Bags may transport:
- Explosives
- Flammable solids
- Oxidizers
- Fertilizers
- Pesticides
- Other regulated materials
- Organic peroxides
Bags can be sealed in a variety of ways, including ties, stitching, gluing, heat sealing, and crimping with metal. Typically, bags are stored and transported on pallets.
**NOTE: Dry bulk intermodal containers carry materials such as fertilizer, cement, and plastic pellets.**

Dry Bulk Railroad Cars
Other railroad cars include hopper cars and miscellaneous cars such as boxcars and gondolas. Descriptions of these cars are as follows:
- Covered hopper cars: Often transport dry bulk materials such as grain, calcium carbide, ammonium nitrate, and cement (Figure 24.156).
- Uncovered (or open top) hopper cars: May carry coal, sand, gravel, or rocks (Figure 24.157).
- Pneumatically unloaded hopper cars: Unloaded by air pressure and used to transport dry bulk loads such as ammonium nitrate fertilizer, dry causticsoda, plastic pellets, and cement. Pressure ratings during unload-ing range from 20 to 80 psi (69 to 552 kPa) (Figures 24.158 a and b).
- Miscellaneous cars: Boxcars and gondolas, well cars, and spine cars often used to carry containers of hazardous materials. These cars can include mixed cargos of a variety of products in different types of packaging (Figure 24.159), so responders may have to deal with gas, liquid, or solids releases.
** NOTE:Cars may be fumigated, presenting additional hazards. **
Bags
A bag is a non-bulk flexible packaging made of paper, plastic film, textiles, woven material, or other similar materials. Bags may transport:
- Explosives
- Flammable solids
- Oxidizers
- Fertilizers
- Pesticides
- Other regulated materials
- Organic peroxides
Bags can be sealed in a variety of ways, including ties, stitching, gluing, heat sealing, and crimping with metal. Typically, bags are stored and transported on pallets.
Radioactive Materials Containers
Table 24.14 provides examples of radioactive materials containers. All shipments of radioactive materials (sometimes called RAM) must be packaged and transported according to strict regulations. These regulations protect the public, transportation workers, and the environment from potential exposure to radiation. The type of packaging used to transport radioactive materials is determined by the activity, type, and form of the material to be shipped.
Depending upon these factors, radioactive material is shipped in one of the following five basic types of containers listed in order of increasing level of radioactive hazard:
- Excepted: This packaging is used to transport materials that have limited radioactivity, such as articles manufactured from natural or depleted uranium or natural thorium. Excepted packagings are only used to transport materials with low levels of radioactivity that present no risk to the public or environment. Empty packaging is excepted. Excepted packaging is not marked or labeled as such. Because of its low risk, excepted packaging is exempt from several labeling and documentation requirements.
- Industrial: This container design retains and protects its contents during normal transportation activities. Industrial packages are not identified as such on the packages or shipping papers. Industrial packages contain materials that present a limited hazard to the public and the environment.
- Examples of these materials include:
- Slightly contaminated clothing
- Laboratory samples
- Smoke detectors
- Examples of these materials include:
- Type A: This container de-sign protects its contents and maintains sufficient shielding under conditions normally encountered during transportation. These packages must demonstrate their ability to withstand a series of tests without releasing their contents. The package and shipping papers will have the words Type A on them. Radioactive materials with relatively high specific activity levels are shipped in Type A packages.
- Examples of these materials include:
- Radio pharmaceuticals (radioactive materials for medical use)
- Certain regulatory qualified industrial products
- Examples of these materials include:
- Type B: These packages must not only demonstrate their ability to withstand tests simulating normal shipping conditions, but they must also withstand severe accident conditions without releasing their contents. Type B packages are identified as such on the package itself as well as on shipping papers. The size of these packages range from small containers to those weighing over 100 tons (91 tonnes). These large, heavy packages provide shielding against radiation. Radioactive materials that exceed the limits of Type A package requirements must be shipped in Type B packages.
- Examples of these materials include:
- Materials that would present a radiation hazard to the public or the environment if there were a major release — Materials with high levels of radioactivity such as spent fuel from nuclear power plants
- Examples of these materials include:
- Type C: These are rare packages used for high-activity materials (including plutonium) transported by air-craft. They are designed to withstand severe accident conditions associated with air transport without loss of containment or significant increase in external radiation levels. The Type C package performance requirements are significantly more stringent than those for Type B packages.
Pipelines
According to PHMSA, as of the year 2015 there are over 2.5 million miles (4 million km) of pipelines in North America. These pipelines transport a variety of flammable and nonflammable hazardous gases and liquids, including:
- Natural gas
- Propane
- Hydrogen
- Gasoline
- Jet fuel
- Crude oil
- Diesel
- Home heating oils
- Carbon dioxide
- Anhydrous ammonia


Pipelines are usually buried, but they may be located aboveground as well, especially in cold climates where the ground is often frozen. In some cases, multiple products may be pushed through the same pipeline at the same time, or separated by a pipeline pig. Hydrocarbons are often commingled (Figure 24.160). Pipelines also come in a variety of sizes and pressures depending on the product and the function of the line. For example, large natural gas transmission pipelines operate under extreme pressure, while smaller distribution lines typically operate under much lower pressures. Figure 24.161 provides an overview of a basic pipeline system for crude oil and natural gas.
Pipeline breaches can be caused by:
- Excavation
- Corrosion
- Equipment, material, joint, or weld failures
- Operation errors
- Natural disasters such as earthquakes and floods
- Vehicle collisions
Emergency responders can view the transmission pipelines in their area via the National Pipeline Mapping System, available online. This system does not provide data on gathering and distribution lines. Pipeline releases can be violent, particularly if gases and/or high pressure transmission lines are involved. Spills and leaks can involve large quantities of product. Since most products transported by pipelines are flammable or combustible, fire control should always be a priority consideration at pipeline incidents.
Some indications of pipeline leaks and ruptures include:
- Visible vapour clouds or liquid spills
- Hissing, roaring, or explosive sounds
- Strong odours such as rotten eggs or petroleum smells
- Liquids bubbling up from water or soil with no obvious source
- High pressure gas blowing out of water or soil
- Dead vegetation or discoloured snow above a pipeline right-of-way
Pipeline markers in the U.S. and Canada include the signal words Caution, Warning, or Danger, representing an increasing level of hazard. They also contain information describing the transported commodity, the carrier’s (operator’s) name, and an emergency telephone number. Establishing good communication and cooperation with pipeline operators before an emergency occurs is an important element of emergency response preparedness.
Pipeline operators are required to provide a wealth of information to emergency responders that can help reduce the impact of an actual release, including:
- Location of transmission pipelines that cross their area
- Name of the pipeline operator and emergency contact information
- Products carried and their hazards
- Location of pipeline emergency response plans
- How to contact the pipeline operator regarding questions, concerns, or emergencies
- How to safely respond to a pipeline emergency
**NOTE:General considerations for responding to a pipeline emergency are provided on pages 23-25 of the 2016 Emergency Response Guidebook.**

Many industrial, commercial, and institutional facilities have piping carrying everything from water and steam to hazardous materials. Pipes carrying hazardous materials should be appropriately marked and labeled. Many facilities in the U.S. and Canada follow ASME’s A13.1-2007, Scheme for Identification of Piping Systems, to mark and label pipes. Where pipelines cross under (or over) roads, railroads, and waterways, pipeline companies must provide markers. These markers are often the best way to identify that pipelines are present, as well as to identify their contents (Figure 24.162). Markers must be in sufficient numbers along the pipeline to identify the pipe’s location. However, pipeline markers do not always mark the pipeline’s exact location, and you should not assume that the pipeline runs in a perfectly straight line between markers.
Vessel Cargo Carriers
Marine vessels transport over ninety percent of the world’s cargo, and that amount is expected to increase in the future. Hazardous materials incidents involving vessels can be minor, such as a small spill at a port during loading or unloading, or major, such as a spill contaminating miles (kilometres) of river or coastline waters. Statistics on oil spills show that most spills are relatively small and result from routine operations such as loading and unloading, which normally occur in ports or at oil/ chemical terminals.
Vessels that transport hazardous materials include the following:
- Tankers (tank vessel): These vessels may transport very large quantities of liquid products.
- Tankers often carry different products in segregated tanks.
- There are three tanker types (Figure 24.163):
- Petroleum carriers transport crude or finished petroleum products.
- Chemical carriers transport many different chemical products.
- Liquefied flammable gas carriers transport liquefied natural gas (LNG) and liquefied petroleum gas (LPG).

-
Figure 24.164 Container vessels transport intermodal containers, including intermodal tanks. Cargo Vessel
- Cargo is shipped in the following four vessel types:
- Bulk carriers may transport liquids or solids.
- Break bulk carriers may transport a variety of materials in many different containers such as pallets, drums, bags, boxes, and crates.
- Container vessels transport cargo in standard intermodal containers with standard widths and varying heights and lengths (Figure 24.164).
- Roll-on/roll-off vessels have large stern and side ramp structures that are lowered to allow vehicles
- to be driven on and off the vessel (Figure 24.165)
Figure 24.165 Roll-on/roll-off vessels have large stern and side ramp structures that are lowered to allow vehicles to be driven on and off the vessel.
- Cargo is shipped in the following four vessel types:
- Barges: Barges are typically box-shaped, flat-decked vesselsused for transporting cargo (Figures 24.166).
- Towing or pushing vessels are usually used to move barges because they are not self-propelled.
- Virtually anything can be transported on a barge.
- Some barges are configured as floating barracks for military or construction crews; some are designed as bulk oil and chemical tankers.
- Other barges carry LNG in cylinders that may not be visible until a person is aboard.
- Barges may serve as floating warehouses with hazardous goods, vehicles, or rail cars inside.

Unit Loading Devices
Unit loading devices (ULDs) are containers and aircraft pallets used to consolidate air cargo into a single, trans-portable unit (Figure 24.167). ULDs are designed and shaped to fit into airplane decks and compartments (particularly, commercial cargo planes), and in some cases they may be stacked. Hazardous materials may be shipped in ULDs provided they are in accordance with governmental regulations, including packaging and label-ing requirements.

Intermediate Bulk Containers
Per the U.S. DOT, an intermediate bulk container (IBC) is either rigid or flexible portable packaging (other than a cylinder or portable tank) designed for mechanical handling (Figure 24.168). Design standards for IBCs in the U.S., Canada, and Mexico are based on United Nations Recommendations on the Transportation of Dangerous Goods. The maximum capacity of an IBC is not more than 3 m3 (3,000 L, 793 gal, or 106 ft3). The minimum capacity is not less than 0.45 m3 (450 L, 119 gal, or 15.9 ft3) or a maximum net mass of not less than 400 kilograms (882 lbs).
** NOTE:These metric measurements were established by the UN. There is no weight limit on solid products. **

IBCs are authorized to transport a wide variety of materials and hazard classes, including:
- Aviation fuel (turbine engine)
- Gasoline
- Hydrochloric acid
- Methanol
- Toluene
- Corrosive liquids
- Solid materials in powder, flake, or granular forms
IBCs are divided into two types:
- Flexible intermediate bulk containers (FIBCs)
- Rigid intermediate bulk containers (RIBCs).
Both types are often called totes.

Flexible Intermediate
Bulk Containers (FIBC) FIBCs are sometimes called bulk bags, bulk sacks, supersacks, big bags, or tote bags. They are flexible, collapsible bags or sacks that are used to carry both solid materials and fluids (Figure 24.169). The designs of FIBCs are as varied as the products they carry. Often the bags used to transport wet or hazardous materials are lined with polypropylene or some other high-strength fabric. Others may be constructed of multi-wall paper or other textiles. A common-sized supersack can carry the equivalent of four to five 55-gallon (208 L) drums and (depending on design and the material inside) can be stacked one on top of another. Sometimes FIBCs are transported inside a rigid exterior container made of corrugated board or wood.

Rigid Intermediate Bulk Containers (RIBC)
RIBCs are typically made of steel, aluminum, wood, fibreboard, or plastic; and they are often designed to be stacked. RIBCs can contain both solid materials and liquids. Some liquid containers may look like smaller ver-sions of intermodal non-pressure tanks with metal or plastic tanks inside rectangular box frames. Other RIBCs may be large, square or rectangular boxes or bins (Figure 24.170). Rigid portable tanks may be used to carry liquids, fertilizers, solvents, and other chemicals; and they may have capacities up to 400 gallons (1 514 L) and pressures up to 100 psi (689 kPa).
Drums
A drum is a non-bulk, flat-ended or convex-ended cylindrical packaging made of the following materials:
- Metal
- Plywood
- Fibreboard
- Other suitable materials
Plastic Drum
capacities range up to 119 gallons (450 L), but 55-gallon (208 L) drums are the most common. Drums may contain a wide variety of hazardous and nonhazardous materials in both liquid and solid form. Typically, metal drums carry flammables and solvents, and plastic/poly drums carry corrosives.
Drums have the following two types of tops:
- Open heads: Removable tops
- Tight (or closed) heads: Non-removable tops with small openings plugged by bungs (stoppers)
- Transportation Placards, Labels, and Markings
Lesson 9
Outcomes:
- Describe ways that transportation placards, labels, and markings indicate the presence and hazards of hazardous materials.
Transportation Placards, Labels, and Markings
The U.S., Canada, and Mexico use a placarding, labeling, and marking system to identify hazmat during transportation. All three countries use the same source for their systems: the United Nations Model Regulations, also known as, The Transport of Dangerous Goods (UN Recommendations). Therefore, with a few country-specific variations, the placards, labels, and markings used to identify hazardous materials during transport are very similar in all three countries. Generally speaking, transportation labels are designed for non-bulk packages, whereas transportation placards are designed for bulk packages. They look similar and convey similar information. However, there are certain unique labels for which there are no equivalent placards.
Under the UN system, nine hazard classes are used to categorize hazardous materials:
- Class 1: Explosives
- Class 2: Gases
- Class 3: Flammable liquids
- Class 4: Flammable solids
- substances liable to spontaneous combustion
- substances that emit flammable gases on contact with water
- Class 5: Oxidizing substances and organic peroxides
- Class 6: Toxic and infectious substances
- Class 7: Radioactive materials
- Class 8: Corrosive substances
- Class 9: Miscellaneous dangerous substances and articles
** NOTE:Because most North American first responders primarily deal with DOT or Transport Canada (TC) placards, labels, and markings, the unique UN placards are not detailed in the sections that follow. **
Examples of the UN class placards and labels with brief explanations are found in Appendix C, UN Class Placards and Labels. Placards, labels, markings, and colours associated with other systems (such as NFPA 704, Standard System for the Identification of the Hazards of Materials for Emergency Response, and military markings) are explained in the section, Other Markings and Colours.
Four-Digit Identification Numbers
In addition to establishing hazard classes, the UN has assigned each individual hazardous material a unique four-digit number. This number is often displayed on placards, orange panels, and certain markings in association with materials being transported in cargo tanks, portable tanks, tank cars, or other containers and packages.

The four-digit identification (ID) number must be displayed on bulk containers in one of the three ways illustrated by Figure 24.171. In North America, the numbers must be displayed on the following containers/ packages:
- Rail tank cars
- Cargo tank trucks
- Portable tanks
- Bulk packages
- Table 1 materials, regardless of quantity (see DOT Chart 15)
- Certain non-bulk packages (for example, poisonous gases in specified amounts)
The Emergency Response Guidebook (ERG) provides a key to the four-digit identification (ID) numbers in the yellow-bordered section. Therefore, if the four-digit identification number is identified, first responders can use the ERG to determine appropriate initial response information based on the material involved. The four-digit identification number will also appear on shipping papers, and it should match the numbers displayed on tank or shipping container exteriors. Common reference materials such as the ERG do not list all four-digit UN identification numbers. For example, the ERG does not list any numbers below 1,000. In the U.S., the entire list is included in 49 CFR 172.101.
** NOTE: NA numbers (North America), also known as DOT numbers, are issued by the United States Department of Transportation and are identical to UN numbers, except that some substances without a UN number may have an NA number. These additional NA numbers use the range NA8000 – NA9999. **

Placards Shippers provide diamond-shaped, colour-coded signs (placards) on transportation containers to identify their contents. Each hazard class has a specific placard that identifies the material’s hazard class. A material’s hazard class is indicated either by its class (or division) number or name. Figure 24.173, provides the required dimensions of transportation placards and summarizes the information conveyed by them.
Placards may be found on the following types of containers:
- Bulk packages
- Rail tank cars
- Cargo tank vehicles
- Portable tanks
- Unit load devices containing hazardous materials over 640 cubic feet (18 m3) in capacity
- Certain non-bulk containers
You may see containers with more than one placard, indicating that more than one hazard or product is present. Figure 24.174 provides the U.S. DOT’s Chart 15, Hazardous Materials Placarding Guide. Unfortunately, improperly marked, unmarked, and otherwise illegal shipments are common. These shipments may include incompatible products, products that contravene local, state/provincial, and federal laws, and waste products shipped and disposed of without a permit.
The following are important facts related to placards:
- A placard is not required for shipments of infectious substances, other regulated materials for domestic trans-port only (ORM-Ds), materials of trade (MOTs), limited quantities, 4-Digit small-quantity packages, radioactive materials (white label I or yellow label II; see Labels section), or combustible liquids in non-bulk packaging
-
Figure 24.174 The U.S. Department of Transportation has a chart showing the different hazardous materials placards that might be posted on a container. Some private agriculture and military vehicles may not have placards, even though they are carrying significant quantities of hazardous materials. For example, farmers may carry fertilizer, pesticides, and fuel between fields of their farms or to and from their farms without any placarding.
- The hazard class or division number corresponding to the primary or subsidiary hazard class of a material must be displayed in the lower corner of a placard (Figure 24.175).
- The DANGEROUS placard is for mixed loads where the transport vehicle contains non-bulk packages with two or more categories of hazardous materials that require different placards (Figure 24.176).
- Other than Class 7 or the DANGEROUS placard, text indicating a hazard (for example, the word FLAMMABLE) is not required. Text may be omitted from the Oxygen placard only if the specific ID number is displayed.
- Drivers may have varying degrees of information about the hazardous materials in their vehicles.
- Containers may have placards even though they appear “empty” until they are certified as “clean.”



Labels
Labels provide similar information as vehicle placards. Labels are 3.9-inch (100 mm), square-on-point diamonds, which may or may not have written text that identifies the hazardous material within the packaging. Figure 24.177 shows the U.S. DOT’s Chart 15, Hazardous Materials Labeling Guide.
Class 7 Radioactive labels must always contain text. Most labels for the nine hazard classes and subdivisions are essentially the same as their placarding counterparts.
Packages with more than one label have more than one hazard or product. These packages contain a primary label and a subsidiary label for materials that meet the definition of more than one hazard class. In Figure 24.178, the toxic label is the primary label, while the flammable liquid label is the subsidiary.

The “Cargo Aircraft Only” label is not associated with a particular hazard class. This label is used to indicate materials that cannot be transported on passenger aircraft.
Markings
A marking is a descriptive name, an identification number, a weight, or a specification and includes instructions, cautions, or UN marks (or combinations thereof) required on the outer packaging of hazardous materials. This section, however, shows only those markings found on DOT Chart 15 (Figure 24.179). Markings on intermodal containers, tank cars, and other packaging are discussed in later sections.


One marking you should note is the “Hot” marking for elevated-temperature materials. Elevated temperature materials, such as molten sulfur and molten aluminum, can present a thermal hazard in the form of heat (Figure 24.180). Molten aluminum, for example, is generally shipped at temperatures above 1,300°F (705°C). First responders must be extremely cautious around these materials to avoid being burned. Molten aluminum and other high-temperature materials can ignite flammable and combustible materials (including wood). Working around or near elevated-temperature materials can increase the effect of wearing personal protective equipment due to high ambient air temperatures.
The U.S. Department of Transportation (DOT) defines an elevated-temperature material as one that when offered for transportation or transported in bulk packaging has one of the following properties:
- Liquid phase at a temperature at or above 212°F (100°C)
- Liquid phase with a flash point at or above 100°F (38°C) that is intentionally heated and offered for transportation or transported at or above its flash point
- Solid phase at a temperature at or above 464°F (240°C)
Hazard Classes
Transportation hazard classes are easier to understand once you have a better understanding of the basic physical and chemical properties explained in the previous sections. In general, a product’s hazard class is assigned based on its most dangerous chemical and/or physical properties. Flammable gases combine the physical hazard of a gaseous state, which expands rapidly, spreads easily, and is difficult to confine, with flammability.

This section describes:
- Class 1: Explosives
- Class 2: Gases
- Class 3: Flammable liquids (and combustible liquids in the U.S.)
- Class 4: Flammable solids, spontaneously combustible, and dangerous when wet
- Class 5: Oxidizers and organic peroxides
- Class 6: Poisons, poison inhalation hazards, and infectious substances
- Class 7: Radioactive
- Class 8: Corrosives
- Class 9: Miscellaneous hazardous materials
- Canadian Placards

Class 1: Explosives
Explosives are reactive. An explosive is any substance or article with a great deal of potential energy that may rapidly expand and release upon activation (undergo an explosion) (Figure 24.181). Explosives may release energy in the form of light, gas, and/or heat. Some explosives may not be specifically designed to explode. Explosive placards list both a division number and a compatibility group letter on them. First responders should pay particular attention to the division number, which assigns the level of explosion hazard to the product. Compatibility group letters categorize different types of explosive substances and articles for purposes of stowage and segregation (Figure 24.182).

Explosives will typically be packaged as solids in individual packages or boxes. However, some explosives are liquids such as certain binary explosives. Some transportation vehicles and certain storage areas are specifically designed for explosives (Figure 24.183). The primary hazards of explosives are thermal and mechanical. Table 24.15 provides the U.S. DOT’s explosive divisions’ definitions, with examples (49 CFR 173.50, 2017).

These hazards may manifest in the following conditions:
- Blast-pressure wave (shock wave): Rapidly released gases can create a shock wave that travels outward from the centre. As the wave increases in distance, the strength decreases. This blast-pressure wave is the primary reason for injuries and damage. The blast-pressure wave has a positive and negative phase, both of which can cause damage (Figures 24.184 a-c).
- Shrapnel and fragmentation: Small pieces of debris thrown from a container or structure that ruptures during an explosion from containment or restricted blast pressure. Shrapnel and fragmentation may be thrown over a wide area and great distances, causing personal injury and other types of damage to surrounding structures or objects. Shrapnel and fragmentation can result in bruises, punctures, or even avulsions (part of the body being torn away) when they strike a person.
- Seismic effect: Vibration is similar to an earthquake. Explosions can cause a seismic effect. When a blast occurs at or near ground level, the air blast creates a ground shock or crater. As the shock waves move across or underground, they form a seismic disturbance. The distance the shock wave travels depends on the type and size of the explosion and type of soil.
- Incendiary thermal effect: Occurs during an explosion when thermal heat energy forms a fireball. Fireballs result from the interactions among burning combustible gases or flammable vapours and ambient air at high temperatures. The thermal heat fireball is present for a limited time after the explosive event.
Additional hazards unrelated to the explosion include:
- Chemical hazards will probably result from the production of toxic gases and vapours.
- Explosives may self-contaminate as they age, which increases their sensitivity and instability.
- Explosives may have high sensitivity to shock and friction.
Class 2: Gases

Gases are materials that are in a gaseous state at normal temperatures and pressures (Figure 24.185). Gases are transported or stored in pressure containers or cryogenic containers (Figures 24.186 a and b). Gas division numbers are assigned according to the type of potential hazard gases pose, such as flammability. The potential hazards of gas include energy, toxicity (including asphyxiation), and corrosivity (Figure 24.187).
Other potential hazards include:
- Heat hazards: Fires, particularly associated with Division 2.1 and oxygen; gases can travel great distances to an ignition source
- Asphyxiation hazards: Leaking or released gases displacing oxygen in a confined space
- Cold hazards: Exposure to Division 2.2 cryogens
- Mechanical hazards: A BLEVE (boiling liquid expanding vapour explosion) for containers exposed to heat or flame; a ruptured cylinder rocketing after exposure to heat or flame
- Chemical hazards: Toxic and/or corrosive gases and vapours, particularly associated with Division 2.3



Class 3: Flammable Liquids (and Combustible Liquids [U.S.])
Flammable and combustible liquids ignite and burn with relative ease (Figure 24.188). Most hazmat incidents, such as gasoline and diesel fuel spills, involve this hazard class. In addition to burning, all flammable and combustible liquids exhibit varying degrees of toxicity. Some flammable liquids are also corrosive. While these materials are transported in liquid containers, they may give off hazardous vapours, much like gases, that may travel from their source. These vapours will burn if ignited. The primary hazards of flammable and combustible liquids are energy, corrosivity, and toxicity.
They often manifest in the following conditions:
- Thermal hazards (heat): Fires and vapour explosions (Figure 24.189)
- Asphyxiation: Heavier-than-air vapours displacing oxygen in low-lying and/or confined spaces
- Chemical hazards: Toxic and/or corrosive gases and vapour
Figure 24.189 While flammable liquids may be corrosive and/ or toxic, their primary hazard is flammability. Courtesy Brent Gaspard, Williams Fire and Hazard Control Inc. s; these may be produced by fires
- Mechanical hazards: A BLEVE, for containers exposed to heat or flame; caused by a vapour explosion
- Vapours: Can mix with air and travel great distances to an ignition source
- Environmental hazards (pollution): Caused by runoff from fire control
Class 4: Flammable Solids, Spontaneously Combustible, and Dangerous When Wet
Class 4 materials are divided into three different divisions (Figure 24.190):
- 4.1 Flammable Solids
- 4.2 Spontaneously Combustible Materials
- 4.3 Dangerous When Wet
It may be difficult for responders to extinguish fires involving Class 4 materials.

Class 4 materials are often solids (metals) that react violently in unexpected ways such as:
- Some flammable solids will react to friction.
- Spontaneously combustible materials may ignite after contact with air.
- Dangerous when wet materials, if involved in a fire, may burn more intensely if firefighters attempt to extinguish the fire with water (Figure 24.191).
Fires involving Class 4 materials may be difficult to extinguish. Incidents involving these materials can be difficult to manage. Even more experienced responders may not fully understand the hazards, and the typical response may make the situation worse. The primary hazards of Class 4 materials are: chemical energy, mechanical energy, corrosivity, and toxicity.
Some examples include:
- Thermal hazards (heat)
- Fires that may start or reignite spontaneously or upon contact with air or water
- Fires and vapour explosions
- Molten substances
- Chemical hazards from irritating, corrosive, and/or highly toxic gases and vapours produced by fire or decomposition
- Severe chemical burns
- Mechanical effects from a BLEVE (if containers exposed to heat, or flame or Division 4.3 contaminated with water) or other unexpected, violent chemical reactions and explosions
-
Figure 24.191 Some Class 4 materials react violently when contacted by water. Chemical hazards from:
- Production of hydrogen gas from contact with metal
- Production of corrosive solutions on contact with water, for Division 4.3
- Production of flammable gas on contact with water, for Division 4.3 (such as calcium carbide)
- Environmental hazards (pollution) caused by runoff from fire control
Class 5: Oxidizers and Organic Peroxides
Class 5 is divided into two divisions (Figure 24.192):
-
Figure 24.192 Class 5 materials are oxidizers and organic peroxides. The illustration provides the U.S. DOT’s Class 5 divisions, placards, definitions, and examples (49 CFR 173.127 and 128, 2017). 5.1 Oxidizers(Typically solids or aqueous solutions)
- 5.2 Organic Peroxides (Liquids or solids)
Oxidizers vigorously support combustion, may be explosive, and when combined with fuel, may burn continuously. Some oxidizers, in conjunction with a fuel, have the ability to burn continuously without air being present. Oxidizers may also be explosive. Oxygen is an example of an oxidizer. Organic peroxides are oxidizers with a specific chemical composition that makes them prone to reactivity. When these materials are involved in an incident, you will need a small amount of heat to start a fire or explo-sion. Organic peroxides are both a fuel and an oxidizer. Because of this, they are reactive. Store organic peroxides below the maximum safe storage temperature (MSST). If organic peroxides reach the self-accelerating decomposition temperature (SADT), they undergo a chemical change and may violently release from their packaging. The time before reaction depends upon how much the SADT is exceeded, which can greatly accelerate the decomposition.
Organic peroxides are not the only materials to have SADTs. Many polymerization initiators or reactive chemicals have an SADT. The responder should recognize these materials by using an SDS or other reference source to obtain this data. Many times the SADT is written into the SDS as decomposition temperature. The primary hazards of Class 5 materials are thermal, mechanical, chemical.
Some examples include:
Thermal hazards (heat) from fires that may explode or burn hot and fast or materials’/substances’ sensitivity to heat, friction, shock, and contamination.
- Explosive reactions to contact with hydrocarbons (fuels)
- Mechanical hazards
- Violent reactions and explosions
- Sensitivity to heat, friction, shock, and/or contamination with other materials
- Chemical hazards
- From toxic gases, vapours, and dust
- From products of combustion
- Resulting in burns
- Thermal hazards from ignition of combustibles (including paper, cloth, and wood)
- Asphyxiation hazards from accumulation of toxic fumes and dusts in confined spaces

Class 6: Poisons, Poison Inhalation Hazards, and Infectious Substances
Class 6 materials and substances include poisons, poison inhalation hazards, and infectious substances (Figure 24.193). Poisonous materials are known to be toxic to humans. Avoid contact with these materials (Figure 24.194). Inhalation hazards are toxic vapours that can be lethal if inhaled. These materials can be extremely dangerous at hazmat incidents because they can travel great distances and harm or kill anyone who breathes them (Figure 24.195). Infectious substances and biohazards are materials that have the potential to cause disease in humans or animals. Infectious materials are typically shipped in small containers, so there is no placard for them, only a label. A biohazard label is used for large and small quantities of regulated medical waste.


The secondary hazards of Class 6 materials are:
- Toxic hazards
- Chemical hazards from toxic and/or corrosive products of combustion
- Thermal hazards (heat) from substances transported in molten form
- Thermal hazards (heat) from flammability and fires

Class 7: Radioactive Materials
Radioactive materials cannot be detected with the senses (Figure 24.196). While Class 7 placards and labels can indicate that radioactive materials are present, without specialized monitoring and detection equipment, it is not possible to determine if a container is actually emitting radiation. It is impossible to tell if radiation is involved in an incident, such as a terrorist attack, where no placards or labels are evident. Small packages of radioactive materials must be labeled on two opposite sides, with a distinctive warning label.
Each of the three label categories:
- Radioactive white-I
- Radioactive yellow-II
- Radioactive yellow-III (bears the unique trefoil symbol for radiation.)

Class 7 Radioactive I, II and III labels must always contain the following additional information (Figure 24.197):

- Isotope name (Figure 24.198)
- Radioactive activity
Radioactive II and III will also provide the Transport Index (TI), which indicates the carrier’s degree of control during transportation. The number in the transport index box indicates the maximum radiation level mea-sured in (mrem/hr) at one meter from the surface of the package. Packages with the Radioactive I label have a Transport Index of 0. Table 24.16, provides the U.S. DOT’s Class 7 unique labels, definitions, and examples (49 CFR 173.403, 2017).
** NOTE: Items placarded as Radioactive II and III have a maximum allowed TI rating of 50 mrem/hr at 1 metre. **
Class 8 Corrosives
Corrosives are either a liquid or solid that cause full thickness destruction of human skin at the site of contact within a specific period of time, or a liquid that has a severe corrosion rate on steel or aluminum (Figure 24.199). Corrosives can also cause a fire or an explosion if they come in contact with other materials because their corrosive actions can generate enough heat to start a fire. Some can react with metal to form (explosive) hydrogen gas. Different types of corrosives (acids and bases) can react violently when mixed together or when combined with water.

The primary hazards of class 8 materials are chemical, toxic, thermal and mechanical.

Some examples include:
- Chemical hazards such as chemical burns
- Toxic hazards due to exposure via all routes of entry into a body
- Thermal hazards (heat), including fire, caused by chemical reactions generating heat
- Mechanical hazards caused by BLEVEs and violent chemical reactions

Class 9: Miscellaneous Hazardous Materials
A miscellaneous dangerous good is a material that (Figure 24.201):
- Has an anesthetic, noxious, or other similar property that could cause distraction or discomfort to crew members during transportation
- Is a hazardous substance or a hazardous waste
- Is an elevated temperature material
- Is a marine pollutant
Miscellaneous dangerous goods will primarily have thermal and chemical hazards. For example, elevated temperature materials may present some thermal hazards, and polychlorinated biphenyls (PCBs) are carcinogenic. However, hazardous wastes may present any of the hazards associated with the materials in normal use.
Canadian Placards, Labels, and Markings Transport Canada (TC) and the Dangerous Goods Act
govern transportation placards, labels, and markings in Canada. Like the U.S. HMR, the Dangerous Goods Act is based on the UN Recommendations and, therefore, is very similar. The nine hazard classes in both documents are identical. Table 24.17, provides Canadian placards, labels, and markings divided by class. There are some differences, however, between Canadian and U.S. placards, labels, and markings such as the following:
- Most Canadian transport placards do not have any signal words written on them.
- Labels and markings may be in both English and French.
- Canada requires a unique placard for anhydrous ammonia and Inhalation Hazards.
- Radiation placard may have the four-digit UN number.

Mexican Placards, Labels, and Markings
Like Canada and the U.S., Mexican transportation placards, labels, and markings are based on the UN Recommendations and have the same hazard classes and subdivisions. In fact, Canadian and Mexican placards and labels are virtually the same, although Mexico does not recognize the Inhalation placard. Because international regulations authorize the insertion of text (other than the class or division number) in the space below the symbol, as long as the text relates to the nature of the hazard or precautions to be taken in handling, placards and labels in Mexico may have text that is in Spanish (Figure 24.202).
Likewise, information provided on markings is likely to be written in Spanish. English-speaking first responders in Mexico or along the U.S./Mexican border should familiarize themselves with the more common Spanish hazard warning terms such as peligro (danger).
Lesson 10
Outcomes:
- Identify other markings and colours that indicate the presence of hazardous materials.
Other Markings and Colours
In addition to DOT placards, labels, and markings, a number of other markings, marking systems, labels, label-ing systems, colours, colour-codes, and signs may indicate the presence of hazardous materials at fixed facilities, on pipelines, on piping systems, and on other containers.

These other markings may be as simple as the word chlorine stencilled on the outside of a fixed-facility tank or as complicated as a site-specific hazard communication system using a unique combination of labels, placards, emergency contact information, and colour codes (Figure 24.203). Some containers may be marked with special information. For example, non-odourized means that the product will not have an intense smell by itself. Some fixed-facility containers may have identification numbers that correspond to site or emergency plans that provide details on the product, quantity, and other pertinent information.
The sections that follow highlight the most common specialized systems in North America, including the following:
- NFPA 704 System
- Globally Harmonized System
- HMIS and other U.S. Hazard Communications labels and markings
- Canadian Workplace Hazardous Materials Information System
- Mexican Hazard Communication System
- CAS® numbers
- Military markings
- Pesticide labels
- Other symbols and signs
- ISO safety symbols
- Colour codes

NFPA 704 System
The information in NFPA 704, Standard System for the Identification of the Hazards of Materials for Emergency Response, gives a widely recognized method for indicating the presence of hazardous materials at commercial, manufacturing, institutional, and other fixed-storage facilities. Use of this system is commonly required by local ordinances for all occupancies that contain hazardous materials. It is designed to alert emergency responders to health, flammability, instability, and related hazards (specifically, oxidizers and water-reactive materials) that may present as short-term, acute exposures resulting from a fire, spill, or similar emergency. Specifically, the NFPA 704 system uses a rating system of numbers from 0 to 4. The number 0 indicates a minimal hazard, whereas the number 4 indicates a severe hazard. The rating is assigned to three categories: health, flammability, and instability. The rating numbers are arranged on a diamond-shaped marker or sign. The health rating is located on the blue background, the flammability hazard rating is positioned on the red background, and the instability hazard rating appears on a yellow background (Figure 24.204). As an alternative, the backgrounds for each of these rating positions may be any contrasting colour, and the numbers (0 to 4) may be represented by the appropriate colour (blue, red, and yellow).
Special hazards are located in the six o’clock position and have no specified background colour; however, white is most commonly used. Only two special hazard symbols are presently authorized for use in this position by the NFPA: W, indicating unusual reactivity with water, and OX, indicating that the material is an oxidizer. However, you may see other symbols in the white quadrant on old diamonds, including the trefoil radiation symbol. If more than one special hazard is present, multiple symbols may be seen.
** NOTE:The NFPA 704 system may be used differently in countries outside of North America. For example, NFPA 704 symbols might be used on transportation containers. **
Globally Harmonized System
The U.S. and many other countries throughout the world have developed a Globally Harmonized System of Classification and Labeling of Chemicals (GHS). The purpose of GHS is to promote common, consistent criteria for classifying chemicals according to their health, physical, and environmental hazards and encourage the use of compatible hazard labels, safety data sheets (formerly known as material safety data sheets) for employees, and other hazard communication information based on the resulting classifications. Appendix D provides an in-depth summary of the GHS system.
Several key harmonized information elements of GHS are as follows:
- Uniform classification of hazardous substances and mixtures
- Uniform labeling standards
- Allocation of label elements
- Symbols and pictograms (Table 24.18)
- Signal words: danger (most severe hazard categories) and warning (less severe hazard categories)
- Hazard statements
- Precautionary statements and pictograms
- Product and supplier identification
- Multiple hazards and precedence of information
- Arrangements for presenting GHS label elements
- Special labeling arrangements

Uniform safety data sheet (SDS) content and format HMIS and Other U.S. Hazard Communications Labels and Markings
OSHA’s Hazard Communication Standard (HCS) requires employers to identify hazards in the workplace and train employees how to recognize those hazards. It also requires the employer to ensure that all hazardous material containers are labeled, tagged, or marked with the identity of the substances contained in them along with appropriate hazard warnings. The standard does not specify what system (or systems) of identification must be used, leaving that to be deter-mined by individual employers. First responders, then, may encounter a variety of different (and sometimes unique) labeling and marking systems in their jurisdictions (Figure 24.205). Conducting pre-incident surveys should assist responders in identifying and understanding these systems. HMIS (Hazardous Materials Information System) is a commonly used proprietary system developed by the American Coatings Association in order to comply with HCS standards. It utilizes a numerical rating and color code system similar to NFPA 704 to convey the relative hazards of the product to employees.
Canadian Workplace Hazardous Materials Information System
Like the U.S. HCS, the Canadian Workplace Hazardous Materials Information System (WHMIS) requires that hazardous products be appropriately labeled and marked. It also spells out requirements for safety data sheets. As with the HCS, there are different ways for Canadian employers to meet the requirements of WHMIS; however, two types of labels will most commonly be used: the supplier label (Figure 24.206) and the workplace label. These labels will include information such as the product name, a statement that an SDS is available, and other information that will vary depending on the type of label (supplier labels will include information about the sup-plier). Table 24.19 shows the old WHMIS Symbols and Hazard Classes, which are being replaced by GHS (CCOHS, 2017).


Mexican Hazard Communication System
Mexico’s equivalent to HCS is NOM-018-STPS-2015. It, too, requires employers to ensure that hazardous chemical substances in the workplace are appropriately and adequately labeled. Essentially, it adopts NFPA 704 and a related hazard communication label system as the official label and marking systems. However, employers can opt to use alternative systems so long as they comply with the objectives and purpose of the standard and are authorized by the Secretary of Labor and Social Welfare.
NOM-026-STPS-1998 (“Signs and Colors for Safety and Health”) authorizes the use of some ISO safety sym-bols (ISO-3864, “Safety Colors and Safety Signs”) on signs to communicate hazard information. General caution symbols in Mexico are triangular rather than round like those in Canada (WHMIS) or rectangular as typically found in the U.S. (Figure 24.207).

CAS® Numbers Chemical Abstract Service®
(CAS®, a division of the American Chemical Society) registry numbers (often called CAS® numbers, CAS® #s, or CAS® RNs) are unique numerical identifiers assigned to individual chemicals and chemical compounds, polymers, mixtures, and alloys (Figure 24.208). They may also be assigned to biological sequences. Over 100 million chemical substances and biological sequences have been registered. Most chemical databases are searchable by CAS® number. They are typically included on safety data sheets (see Safety Data Sheets section) and other chemical reference materials such as the NIOSH Pocket Guide.

Military Markings
The U.S. and Canadian military services have their own marking systems for hazardous materials and chemicals in addition to DOT and TC transportation markings (Figure 24.209). These markings are used on fixed facilities, and they may be seen on military vehicles, although they are not required. Exercise caution, however, because the military placard system is not necessarily uniform. For security reasons, some buildings and areas that store hazardous materials may not be marked. Table 24.20 provides the U.S. and Canadian military markings for explosive ordnance and fire hazards, chemical hazards, and PPE requirements.

Pesticide Labels
The EPA regulates the manufacture and labeling of pesticides. In accordance with GHS, pesticide labels in the U.S. and Canada now include the following (Figure 24.210):
- EPA number or Canadian PCP number
- Hazard statement(s)
- Phrase assigned to each hazard category that describes the nature of the hazard.
- Examples of hazard statements are: “Harmful if swallowed,” “Highly flammable liquid and vapour,” and “Harmful to aquatic life.”
- GHS hazard statements are based in part on current EPA requirements and are generally similar, but there are some differences.
- Pictogram(s): A symbol inside a diamond with a red border, denoting a particular hazard class such as acute toxicity/lethality, and skin irritation/corrosion.
- Precautionary statements: Phrases that describe recommended measures that should be taken to minimize or prevent adverse effects resulting from exposure to a hazardous product, or improper storage or handling of a hazardous product. These phrases cover prevention, response, storage, and disposal of products. GHS provides guidance on precautionary statements and includes a list of statements that may be used. These statements are similar to the precautionary statements that EPA currently uses. Work to increase standardization of precautionary statements may be undertaken in the future.
- Product identifiers: Names or numbers used on a hazardous product label or in a safety data sheet. They provide a unique means by which the product user can identify the chemical substance or mixture. Under the GHS, labels for substances should include the chemical identity of the substance. Labels for mixtures should include the identities of the ingredients that are responsible for certain hazards on the label, except that regulatory authorities may establish rules for protection of Confidential Business Information that preclude ingredient disclosure. (The hazard information still appears on the label even if the ingredients are not named.) Current EPA requirements for product identifiers are consistent with GHS.
- Signal word: One word used to indicate the relative severity of hazard and alert the reader to a potential hazard on the label and safety data sheet.
- The GHS includes two signal words:
- “Warning” for less severe hazard categories
- Danger” for more severe hazard categories
- The GHS includes two signal words:
- Supplier identification: Under the GHS supplier identification, it would include the name, address and telephone number of the manufacturer or supplier of the substance. Current EPA requirements for product identifiers are generally consistent with GHS. EPA encourages, but does not require, telephone contact numbers on pesticide labels.
** NOTE: Lower categories of classification and unclassified products would not require pictograms or signal words under GHS. The current EPA system includes a third signal word “Caution” which is used in addition to “Warning” and “Danger.” **
Other Symbols and Signs
Every facility may have its own system and its own symbols, signs, and markings. Responders should familiarize themselves with the signs and symbols used in their areas. The EPA requires a warning label on any containers, transformers, or capacitors that contain polychlorinated biphenyl (PCB), which is considered hazardous because it may cause cancer. Figures 24.211a, shows a typical U.S. PCB warning label, whereas Figure 24.211b, shows a Canadian PCB warning label.

ISO Safety Symbols
The International Organization for Standardization (ISO) defines the design criteria for international safety signs in their standard, ISO-3864. These symbols are being used more frequently in the U.S. in conjunction with OSHA-required hazard signs (designed per ANSI Standard Z535.4, “Product Safety Signs and Labels”) as well as in Mexico, so first responders should be able to recognize the more common symbols that are used to indicate hazardous materials (Table 24.21).
Colour Codes
Colours can sometimes provide clues to the nature of hazardous materials in North America. For example, even if a DOT placard is too far away to clearly read the number, a first responder can deduce that the material inside is some kind of oxidizer if the placard background colour is yellow. If the placard colour is red, the material is flammable. Pre-incident surveys can assist in identifying colour systems used by local industries, for example, to identify materials used in piping systems.
ANSI Z535.1 sets forth the following safety colour code that is recommended for use in the U.S. and Canada:
- Red = Danger or Stop
- Is used on containers of flammable liquids, emergency stop bars, stop buttons, and fire protection equipment
- Orange = Warning
- Is used on energized equipment or hazardous machinery with parts that can crush or cut
- Yellow = Caution
- Solid yellow, yellow and black stripes, or yellow and black checkers may be used to indicate physical hazards such as tripping hazards; also used on containers of corrosive or unstable materials
- Green = Marks safety equipment such as first-aid stations, safety showers, and exit routes
- Blue = Marks safety information signage such as labels or markings indicating the type of required personal protective equipment (PPE)
Lesson 11
Outcomes
- Describe ways written resources are used to identify hazardous materials and their hazards.
Written Resources
A variety of written resources are available to assist responders in identifying hazardous materials at both fixed facilities and transportation incidents. Fixed facilities should have safety data sheets, inventory records, and other facility documents in addition to signs, markings, container shapes, and other labels. At transportation incidents, first responders should be able to use the current ERG as well as other written resources.
Emergency Response Guidebook (ERG)
The Emergency Response Guidebook (ERG) is a guide to aid emergency responders in quickly identifying the initial hazmat hazards involved in a transportation emergency incident. This allows you to help protect yourself and others during the incident’s initial response phase by avoiding and minimizing hazards.
The Emergency Response Guidebook (ERG) was developed to provide guidance to firefighters, law enforcement, and other emergency services personnel who may be the first to arrive at the scene of a transportation incident involving hazardous materials. Isolation and protective distances in the ERG are based on conditions commonly associated with transportation incidents in open areas and may not be useful when applied to fixed-facility locations or in urban settings.
The ERG will help you identify the material’s specific or generic hazards, and it will also provide you with basic guidance on how to protect yourself and the general public during the incident’s initial response phase. The ERG does not address all possible circumstances that may be associated with a hazardous materials incident. It is primarily designed for use at incidents occurring on a highway or railroad. There may be limited value in its application at fixed-facility locations.
Operations level responders at the scene of a hazmat incident should seek additional, specific information about any material in question as soon as possible. The information received by contacting the appropriate emergency response agency, calling the emergency response number on the shipping document, or consulting the information on or accompanying the shipping document may be more specific and accurate than the guidebook in providing direction for managing the materials involved.

You can locate the appropriate initial action guide page in the ERG in several different ways:
- Identify the four-digit UN identification number on a placard or shipping papers and then look up the appropriate guide in the yellow-bordered pages.
- Reference the name of the material involved (if known) in the blue-bordered pages. Many chemical names differ only by a few letters, so exact spelling is important when using this method (Figure 24.212).
- Identify the material’s transportation placard and then reference the three-digit guide code associated with the placard in the Table of Placards and Initial Response Guide to Use On-Scene located in the front of the ERG.
-
Figure 24.213 As a last resort, if placards or 4-digit ID numbers are not visible, first responders can use container profiles to identify the proper ERG page. Courtesy of Rich Mahaney. Reference the container profiles provided in the white pages in the front of the book.
- First responders can identify container shapes, and then cross-reference the guide number to the orange-bordered page provided in the nearest circle (Figure 24.213).
Using the four-digit ID number or the chemical name allows responders to locate the most specific initial action guide. Skills associated with identifying indicators and hazards present at a hazardous materials incident using approved reference sources are shown in Skill Sheet 24-2. The sections that follow describe the ERG’s design and layout.
ERG Instructions (White Pages)
The white pages provide instructions for using the ERG. There are two white-page sections, one in front and one in back.
The front section provides information on the following:
- Shipping documents (papers)
- How to use the guidebook
- Local emergency telephone numbers
- Safety precautions (see Safety Box)
- Notification and request for technical information
- Hazard classification system
- Introduction to the Table of Markings, Labels, and Placards
- Table of Markings, Labels, and Placards and Initial Response Guide to use on-scene
- Rail Car Identification Chart
- Road Trailer Identification Chart
- Globally Harmonized System of Classification and Labeling of Chemicals (GHS)
- Hazard information numbers displayed on some intermodal containers
- Pipeline transportation The back section provides information about:
- ERG User’s Guide
- Protective clothing
- Fire and spill control
- BLEVE safety precautions
- Criminal/terrorist use of chemical/biological/radiological agents
- Improvised Explosive Device (IED) safe standoff distances
- Glossary
- Canada and United States National Response Centres
- Emergency Response Assistance Plans (ERAP)
- Emergency response telephone numbers

ERG ID Number Index (Yellow-Bordered Pages)
The ERG’s yellow-bordered pages provide a four-digit UN/NA ID number index list in numerical order. The four-digit ID number is followed by its assigned three-digit Emergency Response Guide number (referred to hereafter as the “Guide,”) and the material’s name (Figure 24.214).
The yellow-bordered section in the ERG enables first responders to identify the Guide number to consult for the substance involved. Green highlighting in the yellow-bordered index indicates that the substance releases gases that are toxic inhalation hazard (TIH). These materials require enhanced emergency response distances. A “P” following the Guide number indicates that a material polymerizes. Polymerization is a violent reaction that releases great amounts of heat and energy.

ERG Material Name Index (Blue-Bordered Pages)
The blue-bordered pages of the ERG provide an index of dangerous goods in alphabetical order by material name so that the first responder can quickly identify the Guide to consult for the name of the material involved. This list displays the material’s name followed by its assigned three-digit Guide and four-digit UN/NA ID number (Figure 24.215). The user needs to be very careful when looking up a product’s name because a subtle mistake in the spell-ing can lead a responder toward a substantial misunderstanding of a product’s behaviour. As in the yellow-bordered pages, green highlighting on substances listed in the blue-bordered pages indicates the release of TIH gases, and a “P” following the Guide number indicates that the material polymerizes.
ERG Initial Action Guides (Orange-Bordered Pages)
The book’s orange-bordered section is the most useful be-cause it provides safety recommendations and general hazards information. The orange-bordered pages comprised of individual Guides presented in a two-page format, featuring three sections (Figure 24.216). The left-hand page lists potential hazards and public safety information. The right-hand page provides emergency response information. Each Guide is designed to cover a group of materials that possess similar chemical and toxicological characteristics.

The Guide title identifies the general hazards of the materials or dangerous goods addressed.
Potential Hazards Section
The Potential Hazards section addresses two hazard types under separate headers: Health hazards and Fire or Explosion hazards (Figure 24.217). The highest potential hazard is listed first. This section should be consulted first because it will assist in making decisions regarding the protection of individuals at the incident.
Types of warnings found in this section include:
- TOXIC
- HIGHLY FLAMMABLE
- CORROSIVE.
Toxic Inhalation Hazard (TIH):Volatile liquid or gas known to be a severe hazard to human health during transportation.


Public Safety Section
The Public Safety section provides general information regarding immediate isolation of the incident site and protective clothing and respiratory protection recommendations. This section also lists suggested evacuation distances for small and large spills and for fire situations such as distances for fragmentation hazards for tanks that might explode.
Isolation distances are provided in the bullet points immediately below the Public Safety section heading (Figure 24.218). The initial isolation distance is a distance within which all persons should be considered for evacuation in all directions from the hazmat spill or leak source (Figure 24.219). This distance can be used to identify and establish an initial isolation zone. If safe to do so, you should evacuate people from the initial isolation zone to outside the safe distance (at a minimum) (Figure 24.220). You should then secure the scene and deny entry/access to the isolation zone from anyone on the outside.




The protective clothing section describes the type of personal protective clothing and equipment that should be worn at incidents involving these products (Figure 24.221).
Examples include the
following:
- Street clothing and work uniforms
- Structural firefighters’ protective clothing (also called bunker gear or turnouts)
- Positive pressure self-contained breathing apparatus (SCBA)
- Chemical protective clothing (CPC)
The evacuation section provides evacuation recommendations for spills and fires (Figure 24.222). When the material is a green-highlighted chemical in the yellow-bordered and blue-bordered pages, this section also directs the reader to consult the tables on the green-bordered pages listing TIH materials and water-reactive materials (see ERG Table of Initial Isolation and Protective
Action Distances [Green Pages] section). Awareness level personnel will probably not be involved in evacuations beyond the initial isolation phase.Emergency Response Section. The third section, Emergency Response, describes emergency response topics, including pre-cautions for incidents involving fire, spills or leaks, and first aid. Several recommendations are listed under each section to further assist in the decision-making process. The first aid information provides general guidance before seeking medical care. The Fire section recommends the extinguishing agent to use on large fires, small fires, and fires involving bulk containers (Figure 24.223). Examples might include foam or water, or a specific type of fire extinguisher for small fires.

If foam is recommended, it will specify the type of foam to be used.Recommendations vary by Guide, but may include such things as cooling containers with flooding quantities of water or using unmanned hose holders.
The Spill or Leak section provides actions to take in regards to spills and leaks (Figure 24.224). If a flammable liquid is involved, for example, it would recommend eliminating all ignition sources. It will also provide basic information needed to mitigate a spill, such as what materials to use to absorb the spill.
The First Aid section section provides basic steps to help victims affected by the hazardous material involved (Figure 24.225). Common recommendations include calling for emergency medical service assistance, moving victims to fresh air, and flushing contaminated skin and eyes with running water (decontamination). Avoiding direct contact with the hazardous material is also emphasized.
Many recommendations provided in this section will be beyond the scope of Awareness Level personnel due to the need for specialized training and personal protective equipment, the dangers of cross contamination, and the necessity of decontaminating victims before first aid is provided. For example, Awareness Level personnel should never enter hazardous atmospheres or potentially contaminated areas.



Victims at hazmat incidents may present serious hazards to rescuers because they may be contaminated with the hazardous material (Figure 24.226). Only first responders with appropriate training and wearing the appropriate personal protective equipment should touch or handle these victims. Awareness Level personnel should not handle or touch contaminated or potentially contaminated victims at hazmat incidents, even to provide basic first aid.
ERG Tables of Initial Isolation and Protective Action Distances (Green-Bordered Pages)
The green-bordered section consists of three tables:
- Table 1, Initial Isolation and Protective Action Distances
- Table 2, Water Reactive Materials which Produce Toxic Gases
- Table 3, Initial Isolation and Protective Action Distances for Different Quantities of Six Common TIH (PIH in the U.S.)

Gases Table 1, Initial Isolation and Protective Action Distances
Table 1 lists TIH materials by their 4-digit UN/NA ID number. The table provides two different types of recommended safe distances: initial isolation distances and protective action distances (Figure 24.227). These materials are highlighted for easy identification in both numeric (yellow-bordered) and alphabetic (blue-bordered) ERG indexes (Figure 24.228).

The table provides isolation and protective action distances for both small and large spills (Figure 24.229). A small spill (approximately 55 gallons [220 L] or less) involves a single, small package, small cylinder, or small leak from a large package. A large spill (more than 55 gallons [220 L]) is one that involves a spill from a large package or multiple spills from many small packages. The list is further subdivided into daytime and night time situations because atmospheric conditions are often different depending on the time of day. Atmospheric conditions can significantly affect the size of a chemically hazardous area.
The warmer, more active atmosphere common during the day disperses chemical contaminants more readily than the cooler, calmer conditions common at night. Therefore, during the day, lower toxic concentrations may be spread over a larger area than at night when higher concentrations may exist in a smaller area. The quantity of material spilled or released and the area affected are both important, but the single most critical factor is the concentration of the contaminant in the air.
As with the isolation distances provided in the orange-bordered pages, the initial isolation distances provided in the green-bordered pages are the distance within which all persons should be considered for evacuation in all directions from an actual hazardous materials spill/leak source. This distance will always be at least 100 feet (30 m).

Protective actions are those steps taken to preserve the health and safety of emergency responders and the public. People in this area could be evacuated and/or sheltered in-place.
If hazardous materials are on fire or have been leaking for longer than 30 minutes, this ERG table does not apply. Seek more detailed information on the involved material on the appropriate orange-bordered page in the ERG. Also, the orange-bordered pages in the ERG provide recommended isolation and evacuation distances for non-highlighted chemicals with poisonous vapours and situations where the containers are exposed to fire.
Materials with the text, “when spilled in water,” following their names in Table 1 are considered water reactive and are covered in more detail in Table 2. Table 1 lists the chemicals produced when the material is spilled into water. Some Water Reactive materials are also TIH materials themselves (Bromine trifluoride, Thionyl chloride). In these instances, entries are provided in Table 1 to differentiate water-based spills from land-based spills (“when spilled on land”).
Table 2, Water Reactive Materials which Produce Toxic Gases
Table 2 lists water reactive materials which produce large amounts of TIH gases when the material is spilled in water. Table 2 also identifies the TIH gases produced as a result of the spill. The materials are listed in ID number order. If the water reactive material is NOT a TIH and this material is NOT spilled in water, Table 1 and Table 2 do not apply and safety distances will be found within the appropriate orange guide.
Table 3, Initial Isolation and Protective Action Distances for Different
Quantities of Six Common TIH (PIH in the U.S.) Gases. Table 3 lists Toxic Inhalation Hazard materials that may be more commonly encountered.
The selected materials are:
- Ammonia (UN1005)
- Chlorine (UN1017)
- Ethylene oxide (UN1040)
- Hydrogen chloride (UN1050) and Hydrogen chloride, refrigerated liquid (UN2186)
- Hydrogen fluoride (UN1052)
- Sulfur dioxide/Sulphur dioxide (UN1079)
The materials are presented in alphabetical order and provide Initial Isolation and Protective Action Distances for large spills involving different container types (therefore different volume capacities) for daytime and night-time situations and different wind speeds. Shipping Papers Shipments of hazardous materials must be accompanied by shipping papers that describe them. The information can be provided on a bill of lading, waybill, or similar document. The general location and type of paperwork change according to the mode of transport. However, the exact location of the documents varies. Hazardous waste shipments must be accompanied by a Uniform Hazardous Waste Manifest document that is typically attached to the shipping papers.
The Basic description provided in shipping papers will follow a sequence best remembered by the acronym, ISHP:
- I = Identification Number
- S = Proper Shipping Name
- H = Hazard Class or Division
- P = Packing Group

When you know that a close approach to an incident is safe, you can then examine the cargo shipping papers. The information provided, such as proper shipping name and the hazard class, can then be used to identify hazards such as potential fire, explosion, and health hazards. Precautions to protect emergency responders and the public can be identified using the Emergency Response Guidebook or other reference source. You may need to check with the responsible party in order to locate shipping papers. If the responsible party is not carrying them, you will need to check the appropriate locations. In trucks and airplanes, these papers are placed near the driver or pilot. On ships and barges, the papers are placed on the bridge or in the pilothouse of a controlling tugboat. The train crew should have train consists (entire train’s cargo lists), train list, and/or wheel reports. Look for the train crew first, as they should have the paperwork (train list), however, if they cannot be located, contact the railroad through their emergency phone number for a copy of the train list. It is possible there may also be a copy of the current train list in the engine. On the train list, most railroad companies will count and list their train cars from the front of the train to the back. During pre-incident surveys, the location of the papers (and how to read them) for a specific rail line can be determined. Figure 24.230 provides a summary of shipping paper requirements.
** NOTE: Shipping paper information may be provided in a variety of formats such as FAX and email. **
Trans-border shipments between the U.S. and Mexico may be accompanied by shipping documents in both English and Spanish. To satisfy the emergency response information requirements in the U.S. or Mexico, a ship-per may attach a copy of the appropriate guide page from the current ERG to the shipping papers. The information must be provided in Spanish when the material is shipped to Mexico and in English when shipped to the U.S. so that emergency responders in each country will be able to understand the appropriate initial response procedures in the event of a hazardous material release.

Safety Data Sheets (SDSs)
A safety data sheet (SDS) is a detailed information bulletin prepared by a chemical’s manufacturer or importer that provides specific information about the product.
SDSs are formatted according to Globally Harmonized System (GHS) specifications. SDSs are often the best sources of detailed information about a particular material to which emergency responders have access. The sheets can be acquired from the manufacturer of the material, the supplier, the shipper, an emergency response centre such as CHEMTREC®, or the facility hazard communication plan (Figure 24.231). SDSs are sometimes attached to shipping papers and containers. SDS sheets are used worldwide.
Relevant sections of SDSs can be used to identify potential fire, explosion, and health hazards as well as precautions to be taken to protect responders and the public.
Per OSHA, the list below describes SDS sections:
- Section 1: Identification
- This section identifies the chemical on the SDS as well as the recommended uses. It also provides the essential contact information of the supplier.
- Section 2: Hazard(s) identification
- This section identifies the hazards of the chemical presented on the SDS and the appropriate warning information associated with those hazards.
- Section 3: Composition/information on ingredients
- This section identifies the ingredient(s) contained in the product indicated on the SDS, including impurities and stabilizing additives. This section includes information on substances, mixtures, and all chemicals where a trade secret is claimed.
- Section 4: First aid measures
- This section describes the initial care that should be given by untrained responders to an individual who has been exposed to the chemical.
- Section 5: Fire fighting measures
- This section provides recommendations for fighting a fire caused by the chemical.
- Section 6: Accidental release measures
- This section provides recommendations on the appropriate response to spills, leaks, or releases, including containment and cleanup practices to prevent or minimize exposure to people, properties, or the environment. It may also include recommendations distinguishing between responses for large and small spills where the spill volume has a significant impact on the hazard.
- Section 7: Handling and storage
- This section provides guidance on the safe handling practices and conditions for safe storage of chemicals.
- Section 8: Exposure controls/personal protection
- This section indicates the exposure limits, engineering controls, and personal protective measures that can be used to minimize worker exposure.
- Section 9: Physical and chemical properties
- This section identifies physical and chemical properties associated with the substance or mixture.
- Section 10: Stability and reactivity
- This section describes the reactivity hazards of the chemical and the chemical stability information. This section is broken into three parts: reactivity, chemical stability, and other.
- Section 11: Toxicological information
- This section identifies toxicological and health effects information or indicates that such data are not available.
- Section 12: Ecological information
- This section provides information to evaluate the environmental impact of the chemical(s) if it were released to the environment.
- Section 13: Disposal considerations
- This section provides guidance on proper disposal practices, recycling or reclamation of the chemical(s) or its container, and safe handling practices. Tominimize exposure, refer to Section 8 (Exposure Controls/Personal Protection) of the SDS.
- Section 14: Transport information
- This section provides guidanceon classification information for ship-ping and transporting of hazardous chemical(s) by road, air, rail, or sea.
- Section 15: Regulatory information
- This section identifies the safety, health, and environmental regulations specific for the product that is not indicated anywhere else on the SDS.
- Section 16: Other information
- This section indicates when the SDS was prepared or when the last known revision was made. The SDS may also state where the changes have been made to the previous version. Other useful information also may be included here.

Facility Documents The Hazard Communication Standard (HCS) requires U.S. employers to maintain Chemical Inventory Lists (CILs) of all their hazardous substances (Figure 24.232). Because CILs usually contain information about the locations of materials within a facility, they can be useful tools in identifying containers that may have damaged or missing labels or markings (such as a label or marking made illegible because of fire damage).
Several other documents and records may provide information about hazardous materials at a facility such as the following:
- Shipping and receiving documents
- Inventory records
- Risk management and hazardous communication plans
- Chemical inventory reports (known as Tier II reports)
- Facility Pre-plans
The Local Emergency Planning Committee (LEPC) is another potential source of information. LEPCs were designed to provide a forum for emergency management agencies, responders, industry, and the public to work together to evaluate, understand, and communicate chemical hazards in the community and develop appropriate emergency plans in case these chemicals are accidentally released. These plans are called Local Emergency Response Plans (LERPs).
Electronic Technical Resources
Technical resources and references have advanced with technology. Many common written resources and references are now available in an electronic format, for example, the ERG. Electronic resources have the added benefit of search features that allow information to be accessed in a more efficient manner than print resources. If the product has been identified, some of these resources can be used to determine precautions to be taken to protect responders and the public.
Many references can also be accessed on smartphones or mobile devices. While electronic resource use is increasing, it may still be necessary to have print resources available should there be issues in accessing the electronic data. There are a variety of mobile weather applications (apps) that can be used. These provide up-to-date weather information on mobile devices.
Computer-Aided Management of Emergency Operations (CAMEO)
Computer-Aided Management of Emergency Operations (CAMEO) is a resource designed by the National Oceanic and Atmospheric Administration (NOAA). CAMEO is a system of software applications that helps emergency responders develop safe response plans. It can be used to access, store, and evaluate information critical in emergency response.
Wireless Information System for Emergency Responders (WISER)
The Wireless Information System for Emergency Responders (WISER) is an electronic resource that brings a wide range of information to the hazmat responder including:
- Risk management and hazardous communication plans
- Chemical inventory reports (known as Tier II reports)
- Facility Pre-plans
The Local Emergency Planning Committee (LEPC) is another potential source of information. LEPCs were designed to provide a forum for emergency management agencies, responders, industry, and the public to work together to evaluate, understand, and communicate chemical hazards in the community and develop appropriate emergency plans in case these chemicals are accidentally released. These plans are called Local Emergency Response Plans (LERPs).
Electronic Technical Resources
Technical resources and references have advanced with technology. Many common written resources and references are now available in an electronic format, for example, the ERG. Electronic resources have the added benefit of search features that allow information to be accessed in a more efficient manner than print resources. If the product has been identified, some of these resources can be used to determine precautions to be taken to protect responders and the public.
Many references can also be accessed on smartphones or mobile devices. While electronic resource use is increasing, it may still be necessary to have print resources available should there be issues in accessing the electronic data. There are a variety of mobile weather applications (apps) that can be used. These provide up-to-date weather information on mobile devices.
Computer-Aided Management of Emergency Operations (CAMEO)
Computer-Aided Management of Emergency Operations (CAMEO) is a resource designed by the National Oceanic and Atmospheric Administration (NOAA). CAMEO is a system of software applications that helps emer-gency responders develop safe response plans. It can be used to access, store, and evaluate information critical in emergency response.
Wireless Information System for Emergency Responders (WISER)
The Wireless Information System for Emergency Responders (WISER) is an electronic resource that brings a wide range of information to the hazmat responder including:
- Chemical identification support
- Characteristics of chemicals and compounds
- Health hazard information
- Containment advice
WISER is available in different formats depending on the operating system. It may be downloaded free of charge. 911 Toolkit Available only for Apple devices, the 911 Toolkit app provides a variety of information that may be useful for first responders. It provides information on hydraulics, water delivery, EMS, hazmat, NIMS/ICS. It also provides checklists and quizzes. Hazmat IQ eCharts Based on the popular HazMat IQTM training course, the Hazmat IQ eCharts app provides the charts used to determine the appropriate response to chemical incidents. The app is available for Android and Apple devices.
Using Resources to Transition to Planning the Incident
After identifying a hazardous material/substance, use the following sources to gather information about its physi-cal and chemical properties:
- Emergency Response Guidebook (ERG)
- Shippers and shipping papers
- Safety Data Sheets (SDS) (available at fixed facilities where the products are stored or used)
- Pipeline operators
- Computer apps such as CAMEO and WISER
- Placards and labels
Manufacturers Responders can use the previous sources listed to determine a product’s hazards and the way it is likely to behave based on its chemical and physical properties.
Additional information gathered from these sources may include:
- Potential health hazards
- Signs and symptoms of exposure
- Responsible party contact information
- Precautions for safe handling and control measures including PPE and spill cleanup procedures
- Emergency and first aid procedures
Chapter Review
- Describe the APIE process as it relates to hazardous materials incidents.
- a) Assess, Plan, Implement, Evaluate
- b) Analyze, Plan, Implement, Evaluate
- c) Assess, Prepare, Initiate, Execute
- d) Analyze, Prepare, Initiate, Evaluate
- How do hazmat incidents differ from other emergency incidents?
- a) They involve more personnel
- b) They require specialized equipment and training
- c) They are less dangerous
- d) They are more common
- Explain the difference between acute, chronic, and delayed health effects.
- a) Acute effects are long-term; chronic effects are immediate; delayed effects happen after 24 hours
- b) Acute effects are immediate; chronic effects are long-term; delayed effects happen after 24 hours
- c) Acute effects are immediate; chronic effects are delayed; delayed effects are long-term
- d) Acute effects are short-term; chronic effects are long-term; delayed effects happen after 24 hours
- What are the four main routes of entry through which hazardous materials can enter the body and cause harm?
- a) Inhalation, ingestion, absorption, injection
- b) Inhalation, absorption, ingestion, exposure
- c) Inhalation, exposure, absorption, penetration
- d) Inhalation, penetration, ingestion, exposure
- What are the three main mechanisms by which hazardous materials can cause bodily harm?
- a) Chemical, biological, physical
- b) Physical, thermal, chemical
- c) Biological, chemical, radiation
- d) Chemical, radiation, thermal
- What are the different hazards for gases, liquids, and solids?
- a) Gases can be flammable; liquids can be toxic; solids can be corrosive
- b) Gases can be explosive; liquids can spill; solids can emit radiation
- c) Gases can be toxic; liquids can be corrosive; solids can be flammable
- d) Gases can leak; liquids can evaporate; solids can dissolve
- List the physical properties of materials and explain how they help to determine hazards.
- a) Density, viscosity, hardness
- b) Density, flammability, reactivity
- c) Flammability, reactivity, toxicity
- d) Density, solubility, flammability
- List the chemical properties of materials and explain how they help to determine hazards.
- a) Reactivity, pH, corrosivity
- b) Toxicity, reactivity, flammability
- c) pH, reactivity, density
- d) Corrosivity, flammability, toxicity
- How does the General Hazardous Materials Behavior Model help predict hazards at hazmat incidents?
- a) By providing a step-by-step guide to handling hazmat
- b) By identifying possible scenarios of material behavior
- c) By evaluating the material’s chemical structure
- d) By assessing the environmental impact
- List the seven clues to the presence of hazardous materials.
- a) Occupancy, container shape, transportation placards, labels, markings, documentation, senses
- b) Labels, markings, containers, documentation, senses, location, color
- c) Senses, documentation, color, container shape, occupancy, location, transportation placards
- d) Transportation placards, labels, documentation, senses, occupancy, location, markings
- What types of occupancies and locations are most likely to have hazardous materials?
- a) Schools, hospitals, residential areas
- b) Industrial sites, laboratories, transportation hubs
- c) Parks, office buildings, retail stores
- d) Restaurants, hotels, stadiums
- List the major types of containers of hazardous materials and the various hazards that these containers may pose.
- a) Drums, cylinders, tanks
- b) Drums, tanks, boxes
- c) Cylinders, boxes, drums
- d) Tanks, boxes, cylinders
- How does the U.S. transportation system of placards, labels, and markings indicate the hazards posed by the hazardous materials carried?
- a) By colour coding
- b) By numerical ratings
- c) By symbols and codes
- d) By written descriptions
- What are the nine hazard classes used by the UN to categorize hazardous materials?
- a) Explosives, gases, flammable liquids, flammable solids, oxidizers, toxic materials, radioactive materials, corrosives, miscellaneous
- b) Explosives, gases, flammable liquids, toxic materials, radioactive materials, corrosives, reactive materials, organic peroxides, miscellaneous
- c) Explosives, gases, flammable solids, oxidizers, toxic materials, radioactive materials, corrosives, reactive materials, miscellaneous
- d) Explosives, gases, flammable liquids, flammable solids, oxidizers, toxic materials, radioactive materials, corrosives, reactive materials
- How do the Canadian and Mexican systems of placards, markings, and labels differ from each other and from the U.S. system?
- a) They use different colours
- b) They have different shapes and symbols
- c) They use different languages
- d) They categorize materials differently
- Describe the colour and number system used in NFPA 704, Standard System for the Identification of the Hazards of Materials for Emergency Response.
- a) Red for flammability, blue for health, yellow for reactivity, white for special hazards, numbers indicate severity
- b) Blue for flammability, red for health, yellow for reactivity, white for special hazards, numbers indicate severity
- c) Yellow for flammability, blue for health, red for reactivity, white for special hazards, numbers indicate severity
- d) Red for flammability, yellow for health, blue for reactivity, white for special hazards, numbers indicate severity
- What are the key elements of the Globally Harmonized System?
- a) Uniform classification, labeling, safety data sheets
- b) Color coding, hazard symbols, safety procedures
- c) Safety data sheets, colour coding, uniform classification
- d) Hazard symbols, uniform classification, safety procedures
- How do pesticide labels differ from other hazardous materials labeling systems?
- a) They include specific application instructions
- b) They use different colorus
- c) They have more detailed hazard information
- d) They include environmental impact data
- Where might you find other symbols and signs for hazardous materials not covered above?
- a) In international transport regulations
- b) In workplace safety manuals
- c) In local building codes
- d) In environmental protection guidelines
- Describe common symbols and colours that indicate the presence of hazardous materials as set forth by ANSI Standard Z535.4.
- a) Yellow with a black triangle for caution, red with a white diamond for danger
- b) Yellow with a black diamond for warning, red with a black circle for danger
- c) Yellow with a black diamond for caution, red with a white diamond for warning
- d) Yellow with a black triangle for warning, red with a white circle for danger
- What are the sections of the ERG and what information do the different sections contain?
- a) Yellow section for location guide, blue section for chemical names, orange section for response guides, green section for evacuation distances
- b) Yellow section for chemical names, blue section for location guide, orange section for response guides, green section for evacuation distances
- c) Yellow section for response guides, blue section for chemical names, orange section for location guide, green section for evacuation distances
- d) Yellow section for evacuation distances, blue section for location guide, orange section for chemical names, green section for response guides
- What written resources are first responders most likely to utilize? Why?
- a) Emergency Response Guidebook (ERG), Safety Data Sheets (SDS) for quick reference to hazards and responses
- b) Local fire department manuals for specific procedures
- c) Environmental protection guidelines for regulations
- d) Building codes for structural information
Answers
- b) Analyze, Plan, Implement, Evaluate
- b) They require specialized equipment and training
- b) Acute effects are immediate; chronic effects are long-term; delayed effects happen after 24 hours
- a) Inhalation, ingestion, absorption, injection
- a) Chemical, biological, physical
- c) Gases can be toxic; liquids can be corrosive; solids can be flammable
- d) Density, solubility, flammability
- a) Reactivity, pH, corrosivity
- b) By identifying possible scenarios of material behaviour
- a) Occupancy, container shape, transportation placards, labels, markings, documentation, senses
- b) Industrial sites, laboratories, transportation hubs
- a) Drums, cylinders, tanks
- c) By symbols and codes
- a) Explosives, gases, flammable liquids, flammable solids, oxidizers, toxic materials, radioactive materials, corrosives, miscellaneous
- b) They have different shapes and symbols
- a) Red for flammability, blue for health, yellow for reactivity, white for special hazards, numbers indicate severity
Bottom of Form
Top of Form
Bottom of Form
Top of Form
Bottom of Form
Top of Form
Bottom of Form
Top of Form
Bottom of Form
Top of Form
Bottom of Form