60 Basic Tools
Learning Objectives
- Identify tools
- Describe the purpose and safe use of tools
Key Question
What is a standard set of tools needed to perform basic small engine repair and maintenance?
Introduction
In this chapter, you will learn about different basic tools that will be necessary to work with basic engines. Always follow safety procedures when working with any materials and tools.
Identify Screwdrivers & Their Use
Screwdrivers are available in a variety of lengths and sizes. The length of a screwdriver is measured from the tip to where the handle joins the shank. Lengths range from 38 mm to 60 cm (11/2 in. to 12 in.) or more, with the shorter lengths known as “stubbies.”
Parts of a Screwdriver
The parts of a screwdriver are the head, handle, ferrule, shank, and tip (Figure 1). The size of a screwdriver is indicated by the length of the shank.
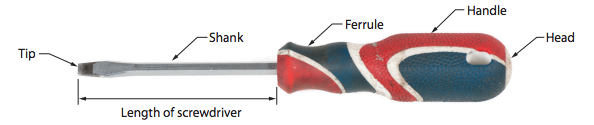
Types of Screwdriver
Screwdriver types include:
- cabinet tip
- round shank
- square shank
- ratchet
- stubby and offset
- multiple bit
Cabinet-Tip Screwdriver
The cabinet-tip screwdriver has a long shank length—150 mm (6 in.) to 200 mm (8 in.)—that is straight on both sides. Regular screwdrivers have a swaged end just above the tip; the cabinet-tip screwdriver does not have this feature (Figure 2). It is designed for attaching cabinet hardware when a screwdriver with a swaged portion would be in the way of the hardware.
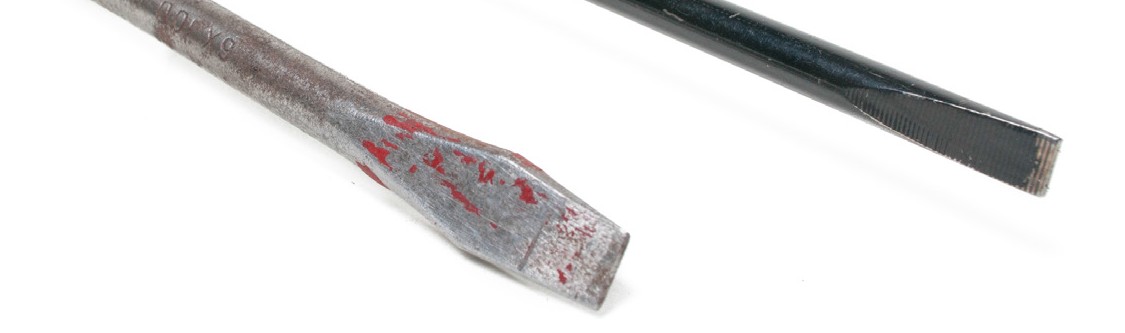
Square-Shank Screwdriver
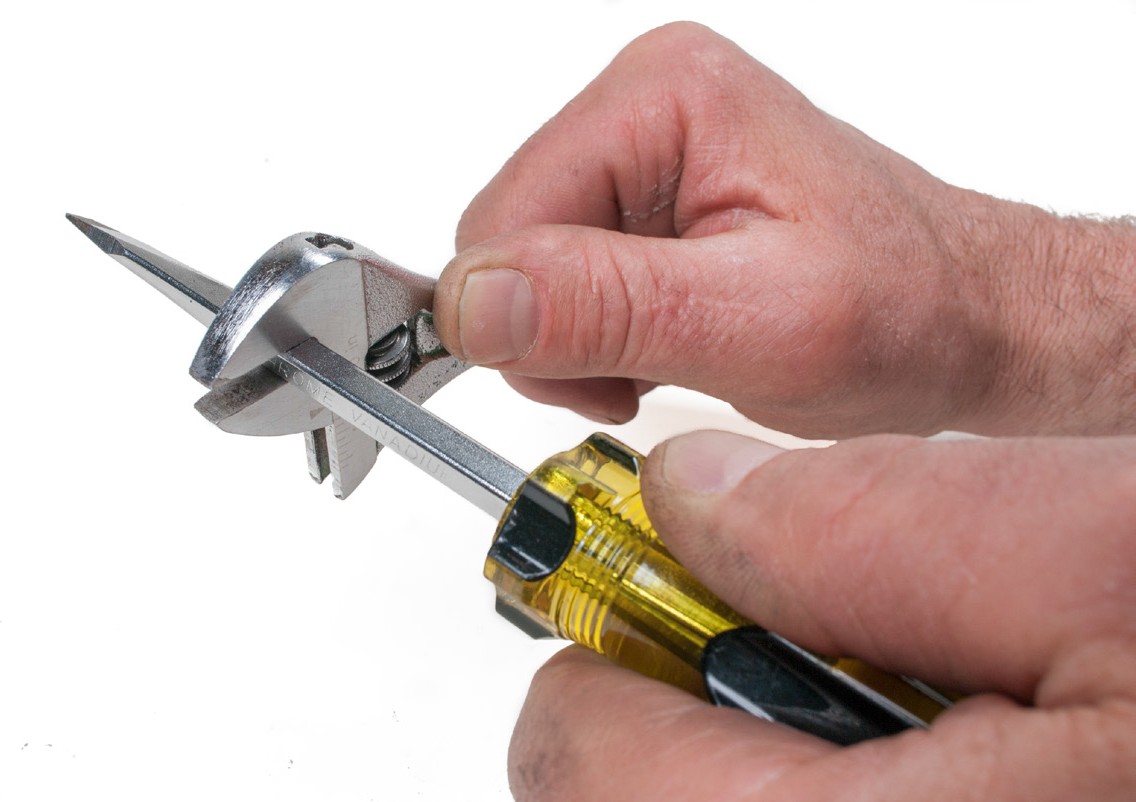
The square-shank screwdriver (Figure 3) is useful for driving large screws because a wrench can be used on the square shank for extra leverage.
Ratchet Screwdriver
The ratchet screwdriver has different tips for fitting into slot, Robertson, and Phillips screws. To speed up a job, the ratchet on the ferrule of the driver can be set to turn or remove a screw. It can also be set to a locked position to permit the driver to be operated as an ordinary screwdriver.
Stubby and Offset Screwdrivers
The stubby screwdriver (Figure 5) is available in all sizes of slot, Robertson, and Phillips tips. The shank and handle are very short—70 mm (23/4 in.) to 85 mm (31/4 in.) long—which is why it is called “stubby.” Stubby screwdrivers are used only when space will not permit use of longer screwdrivers.
Another design that allows the operator to reach into tight spaces is the offset screwdriver (Figure 4). One offset design is Z-shaped, with the tips at a right angle to the shank.
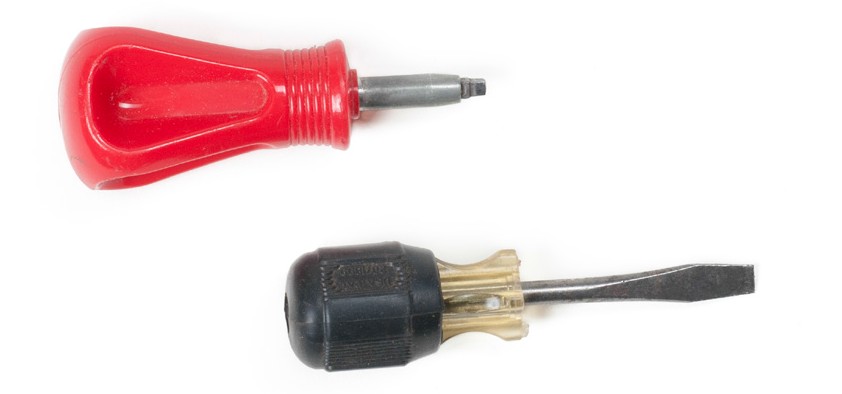
Multiple-Bit Screwdrivers
Multiple-bit screwdrivers are designed to accept different types of tips, enabling a single screwdriver to potentially turn any type of screw. These multi-bit screwdrivers may include storage for extra bits in the handle (Figure 5).
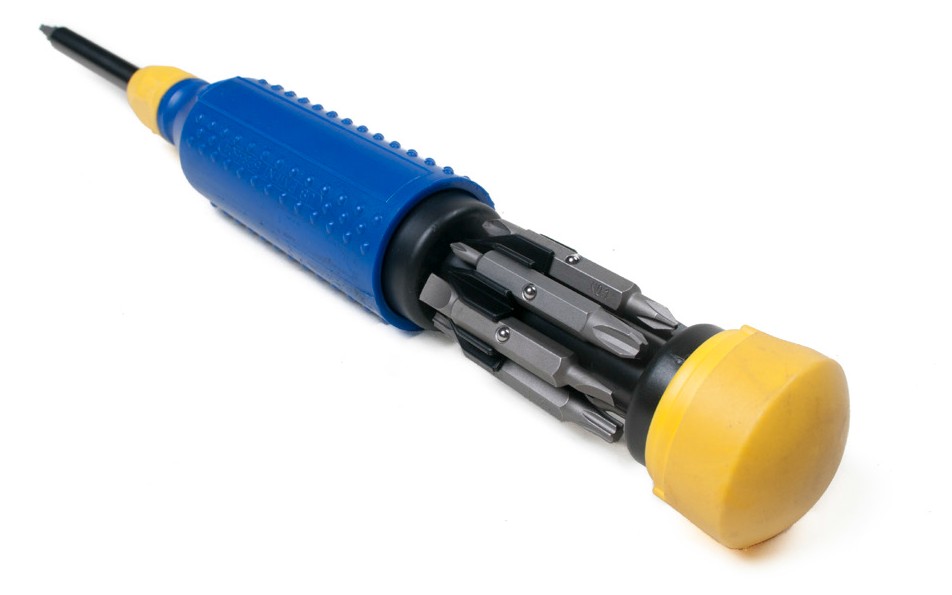
Tip Types
Some common screwdriver tip types include:
- slot
- Phillips
- clutch
- Torx
- hex (Allen)
- Robertson
Slot Tip
The slot tip screwdriver is the most commonly used type of screwdriver, and sometimes it is referred to as the “conventional screwdriver.” It comes in many lengths and tip sizes. When you select a screwdriver for slot screws, make sure that the tip is as wide as the diameter of the screw head and that it is as thick as the slot size. Figure 6 shows the correct fit for slot screwdrivers.
Too small | Too large | Good fit | Good fit | Too narrow |
Figure 6 — Correct and incorrect fits for slot screwdrivers
If the tip of the screwdriver becomes worn and rounded, it should be reshaped by filing or grinding. Figure 7 shows correctly and incorrectly ground tips.
Phillips Tip
The Phillips screwdriver (Figure 8) has a cross tip for fastening screws, and the screws have a cross recess for accepting the driver.
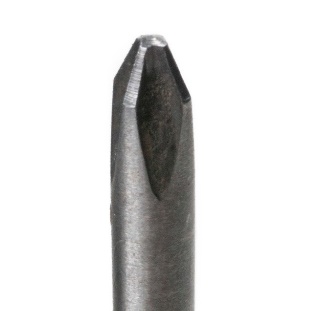
The Phillips screwdriver is available in the following sizes from smallest to largest: No. 00, No. 0, No. 1, No. 2, No. 3, and No. 4. The Phillips screw is often selected for finish hardware.
Torx and Clutch Tips
The tip of the Torx screwdriver is extremely strong and hard, and especially designed for power tools. It is available in the following sizes: T7, T8, T9, Tl0, T15, T20, T25, T27, T30, and T40. Figure 9 shows the Torx and clutch screwdriver tips.
NOTE: Never use an Allen wrench on a Torx screw. The head of the Torx screw may appear to fit an Allen wrench, but you will find that as soon as force is applied, the corners of both the wrench and screw will be damaged.
The clutch screwdriver and screw are used in the automotive and manufacturing industries. The driver tip must exactly match the size of the head. The head of the screw is held firmly by the driver tip. If a slot or Phillips screwdriver is used with it, the screw might slip out.
TorxClutch
Figure 9 — Torx and clutch driver tips
Hex (Allen) Tip
Similar to a hex wrench, hex (or Allen) screwdrivers are used to drive smaller size hex screws that don’t require the same leverage available when using a hex wrench. Hex tips are often available for the multiple-bit screwdrivers.
Robertson Tip
The square tip of the Robertson screwdriver fits into the hole of the Robertson screw (Figure 10).
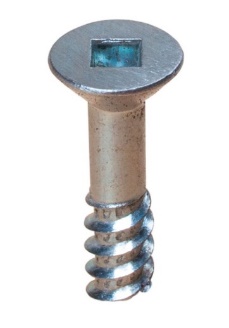
Robertson screwdrivers follow a sizing system that matches the colour of the handles to the tip size and screw sizes (Figure 11). The size is indicated on the handle. The smallest tip size is No. 00; the largest is No. 3.
Color | Tip Size | Screw Sizes |
Orange | No. 00 | #1 & #2 |
Yellow | No. 0 | #3 & #4 |
Green | No. 1 | #5, #6 & #7 |
Red | No. 2 | #8, #9, #10 |
Black | No. 3 | #12 and larger |
Figure 11 — Robertson screw and driver classifications.
The advantage of the Robertson screwdriver is that its end can hold a screw without a clip or magnet. This leaves the operator free to position an object with one hand and fasten it with the other.
Screwdriver Sockets and Bits
Screwdriver sockets (Figure 12) are also available to provide a more positive drive for loosening and tightening screws. Some screw tip fasteners may need to be torqued in place; screwdriver sockets provide a means of attaching a torque wrench.
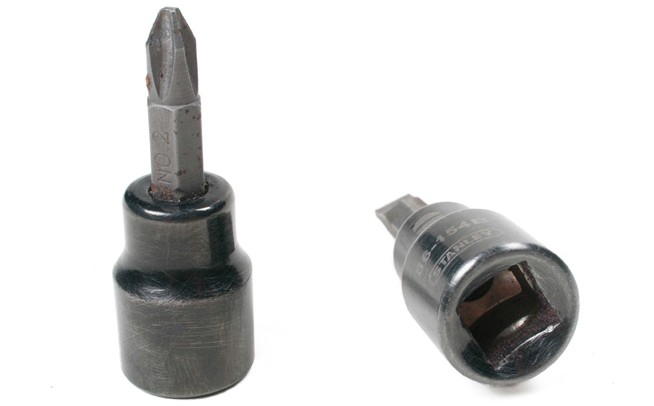
Bits similar to those used in a multiple-bit screwdriver are also available for use in electric drills (Figure 13).
Care and Maintenance of Screwdrivers
Screwdrivers should be kept clean and free of grease, oil, and dirt. The handle should be intact and well secured, and the tip should not be worn. The tip of a slot screwdriver can be filed to shape, but other types must be replaced.
Screwdrivers should never be used as prying tools, punches, scrapers, can openers, or chisels. These misuses will make the screwdriver useless for driving a screw.
Torque Wrenches
Torque is the amount of twisting action at a given point. Without some way of measuring torque, it is impossible to tighten a series of bolts, nuts, or screws to an exact predetermined tension.
Torquing of bolts, nuts, and screws is a very critical operation. Applying too little torque will cause leaks. Applying too much torque will also cause leaks but will also cause distortion and major damage to expensive parts. Torque wrenches (Figure 3) are designed to measure the amount of torque being applied.
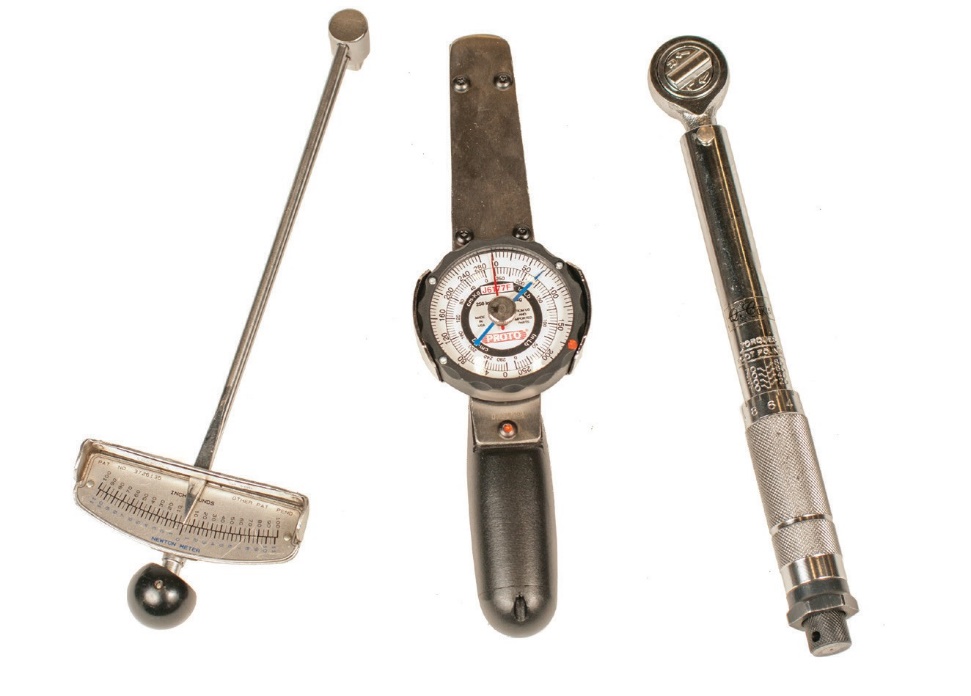
Deflecting-beam | Dial-indicating | Audible-click |
The audible-click type and the dial-indicating type are preferable to the deflecting-beam type. The audible-click torque wrench can be used where it is difficult to read a dial or scale while performing the tightening sequences.
Some torque wrenches have a ratchet drive. Torque wrench square drives vary from 1/4 in. up to 1 in. in size (these measurements are a de facto international standard with no metric equivalents) for standard uses and in larger sizes for heavy industrial applications. Some ratchet drivers operate in both directions, while others operate only in a right-hand rotation.
Pullers
Gear and bearing pullers (Figure 4) are designed for hundreds of applications. Their main purpose is to remove a component from a shaft (such as a gear, pulley, or bearing) or to remove a shaft from inside a hole.
Gear pullers come in a range of sizes and shapes, all designed for particular applications. They consist of three main parts:
- jaws
- cross arm
- centre-forcing screw
There are normally two or three jaws on a puller. The jaws are designed to work either externally around a pulley, or internally. The forcing screw is a long-fine-threaded screw that is applied to the centre of the shaft. When the forcing screw is turned, it applies many tonnes of force through the component you are removing.
The cross arm attaches the jaws to the forcing screw. There may be two, three, or four arms.
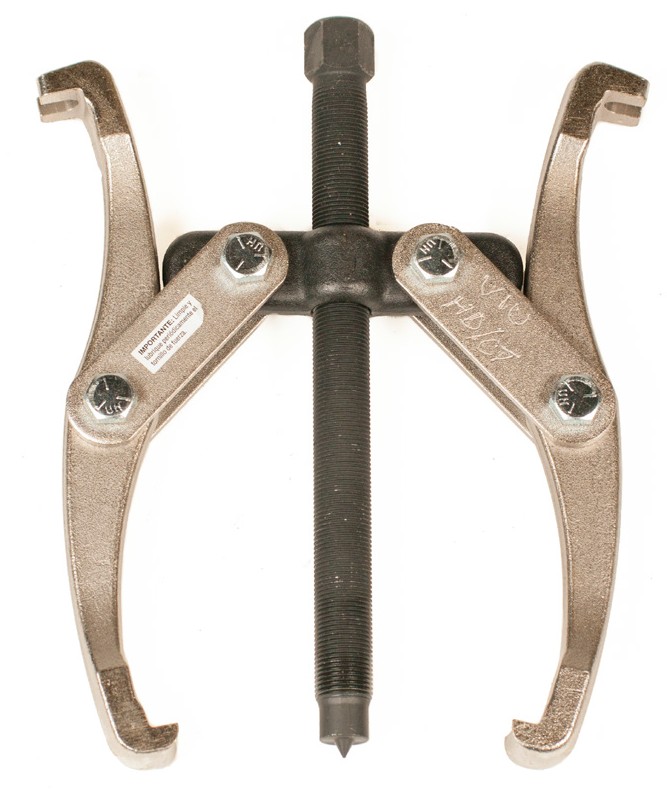
Puller Safety
Pullers (especially hydraulic pullers) can exert a tremendous amount of force, often up to 100 metric tonnes (imperial: 110 tons). Careful attention must be given to the correct choice of puller and to the safe use of that puller.
Place a shaft protector over the end of shaft before installing a puller. When the puller is installed, be sure the set-up is rigid and the puller is square with the work. Apply force gradually. The component should give a little at a time. Do not try to speed the removal by using an impact wrench on the screw. If you have applied maximum force and the part does not move, use a larger capacity puller.
Tools that are in contact with hard metal surfaces and subject to high loads should be regularly inspected. Pullers receive a great deal of abuse when used under some circumstances. The points or hooks on the jaws may become rounded and worn and require replacement or repair. The pressure screw threads should be lightly oiled and clean and free of burrs. The screw end should have a clean point so that it will seat properly into the recess on the adapter plates. Jaw pins should be kept in good condition and properly maintained.
NOTE: Always wear safety glasses.
Wire Brushes
Wire brushes (Figure 5) are used to remove scale, rust, dirt, loose slag, and spatter from metal surfaces. The metal of the brush should match the base metal; for example, a stainless steel brush should be used on stainless steel and a steel brush on mild steel.
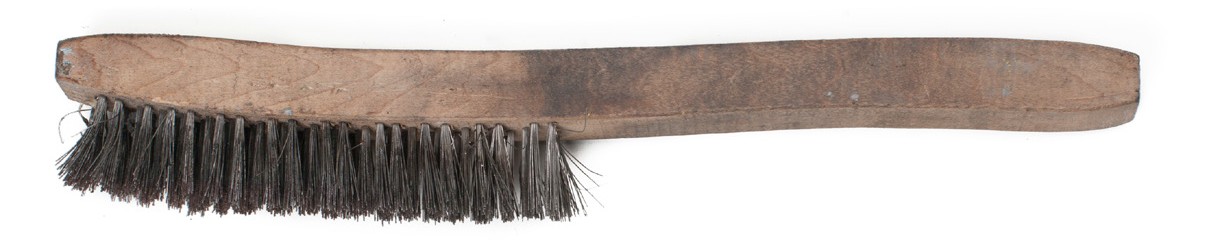
Take care that the sparks from welding or cutting do not fall onto the brushes as the bristles will melt together in lumps and make the brush useless. Wire brushes should be stored so that their bristles will not be bent or damaged by the weight of other tools.
Hand-Operated Grease Guns
There are many different styles of grease guns for different applications (Figure 7). These hand guns are capable of pumping grease at pressures of up to 10 000 psi into grease fittings on components requiring lubrication. They can be equipped with different styles of ends, from straight, fixed extensions to flexible extensions.
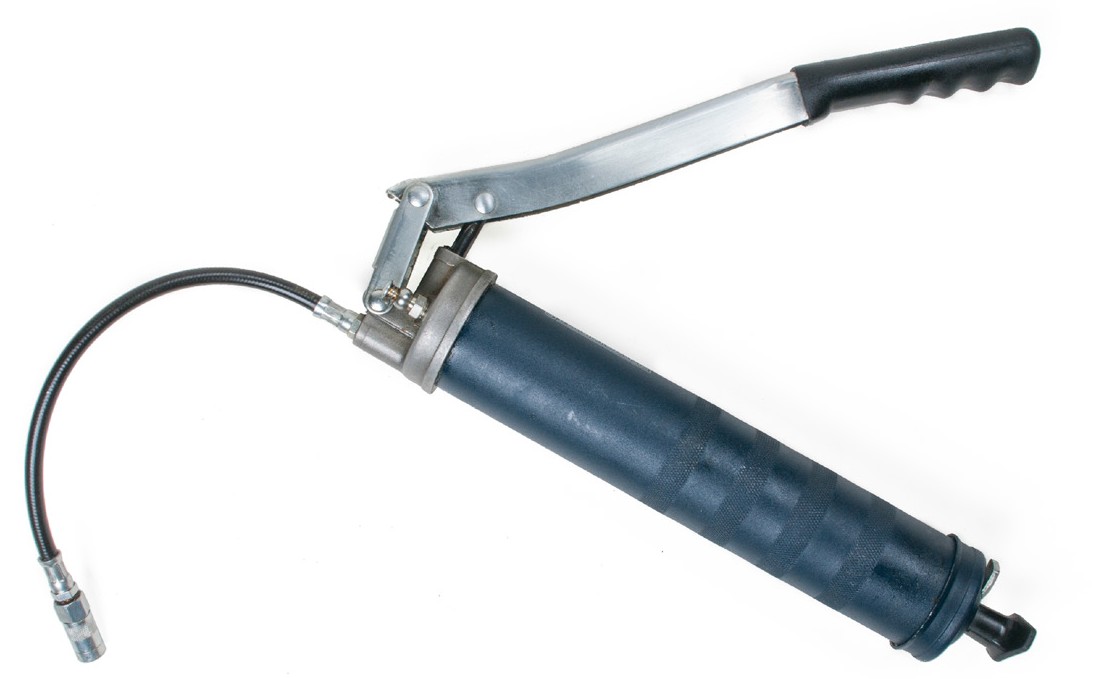
Taps and Dies
Threads are cut on screws, bolts, nuts, studs, and inside holes to allow components to be attached and assembled. Taps cut threads inside holes or nuts, whereas dies cut threads onto the outside of bolts, screws, or studs (Figure 9).
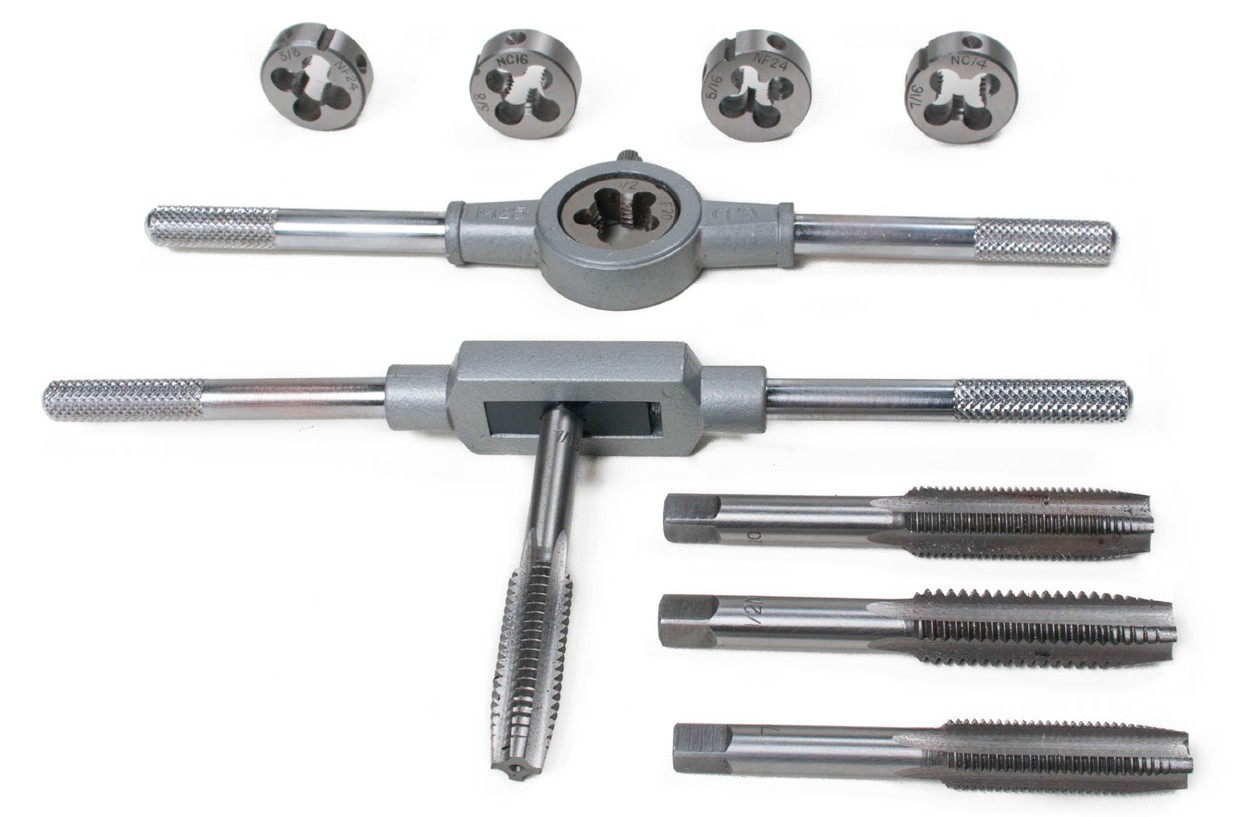
Die nuts, also known as “rethreading dies,” are made for cleaning up damaged threads
(Figure 10). They have no split for resizing and are made from a hexagonal bar so that a wrench or shifter spanner can be used to turn them. Die nuts cannot be used to cut new threads.
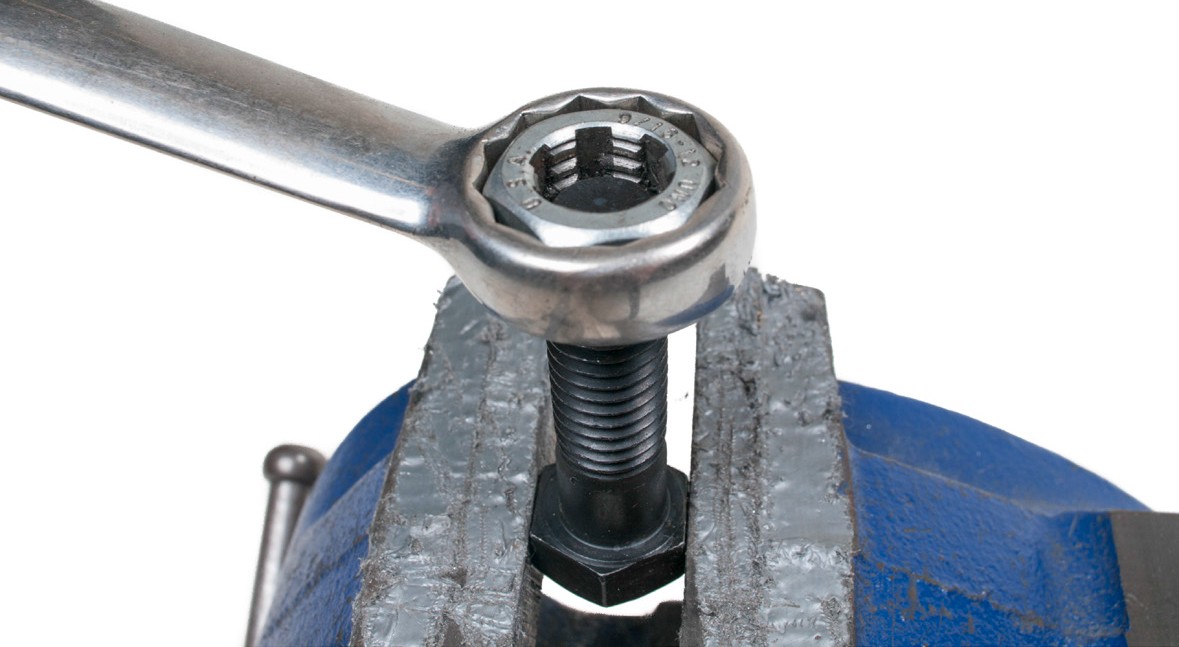
Line C: Tools and Equipment: Competency C-1: Describe Common Hand Tools and Their Uses (BCcampus) Copyright © 2015 by Camosun College is licensed under a Creative Commons Attribution 4.0 International License, except where otherwise noted.